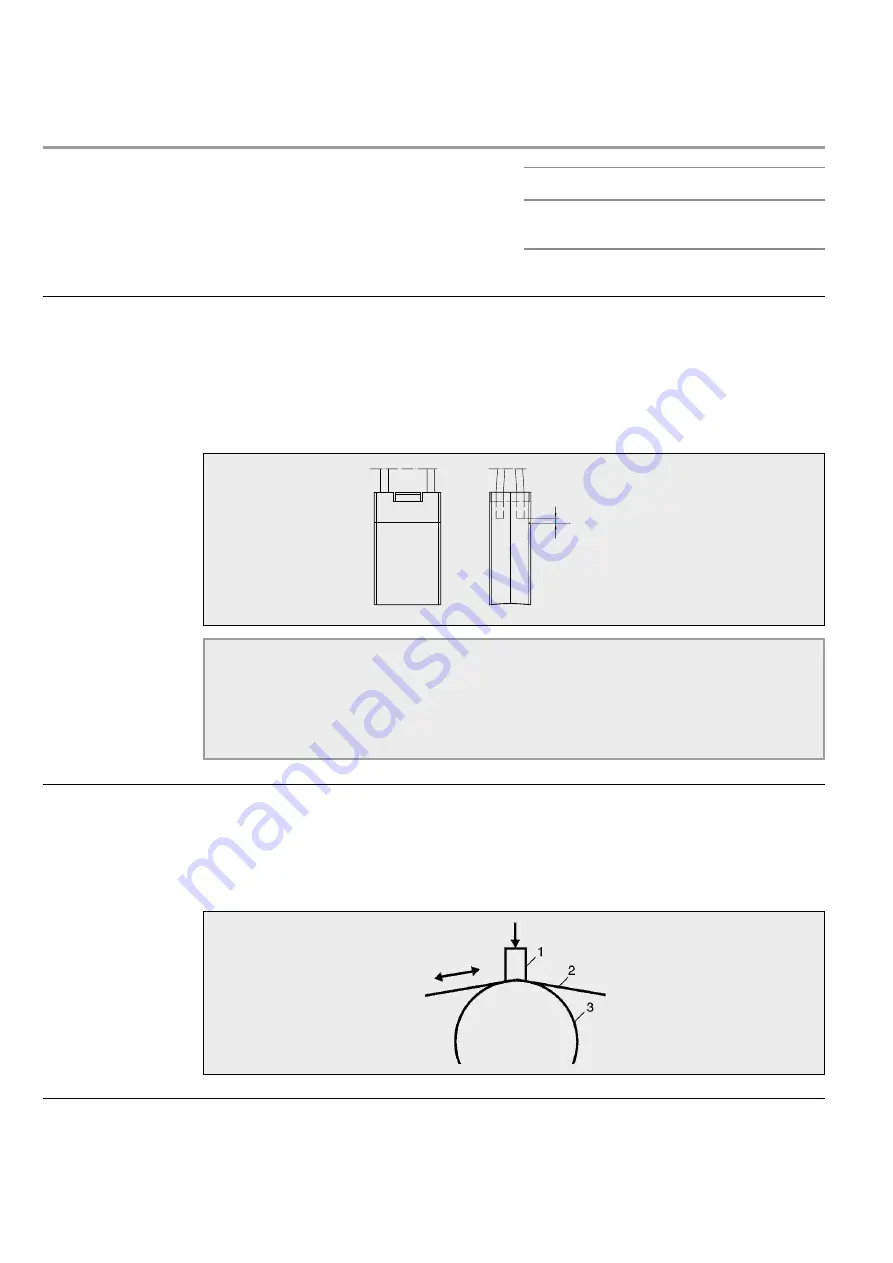
Brush wear
Brushes and commutation
Brush wear is influenced by both mechanical
and electrical factors, and differs greatly from
one brush grade to another. It is therefore not
possible to give universal, definitive figures for
brush wear. The figures given here are indica-
tive only but should not be exceeded by ma-
chines in this range.
The carbon brushes must be changed when
they have worn down to the wearmark on the
brush surface. They must be replaced by
carbon brushes of the same grade as the
original ones.
Commutator peripheral speed
Approximate
brush wear
below 0 m/s
mm/1000 h
0 – 0 m/s
mm/1000 h
0 – 0 m/s
mm/1000 h
Replacing worn
brushes
Worn brushes must be exchanged as a
complete set. All brushes must be bedded-in
after they have been placed into their holders
(refer to “Bedding-in brushes” below).
Only after bedding-in and cleaning of the entire
brush gear may the machine be started.
Fig 12 Brush.
Caution
All brushes must be present for each commutator track surface in use, otherwise brush wear will be
increased. Use only one brush grade per DC machine.
Commutation problems and consequential damage to machines equipped with different type of brush
grade than the original type or the type suggested by ABB is not covered by warranty.
Bedding-in
brushes
A medium-coarse emery cloth is used for bed-
ding-in the carbon brushes. This is done when
the machine is stationary. The emery cloth is
inserted between brushes and commutator with
the abrasive surface facing the brushes and
should slide over the curvature of the
commutator.
Fig 13 Shaping a brush.
1 Brush
2 Emery cloth
3 Commutator
After bedding-in, the commutator and the brush
gear must be cleaned, the brushes removed
from their pockets, blown clean and checked to
see that there are no abrasive particles on the
brush surface.
2
Groove or painted line on
one side shows limit of wear.
mm