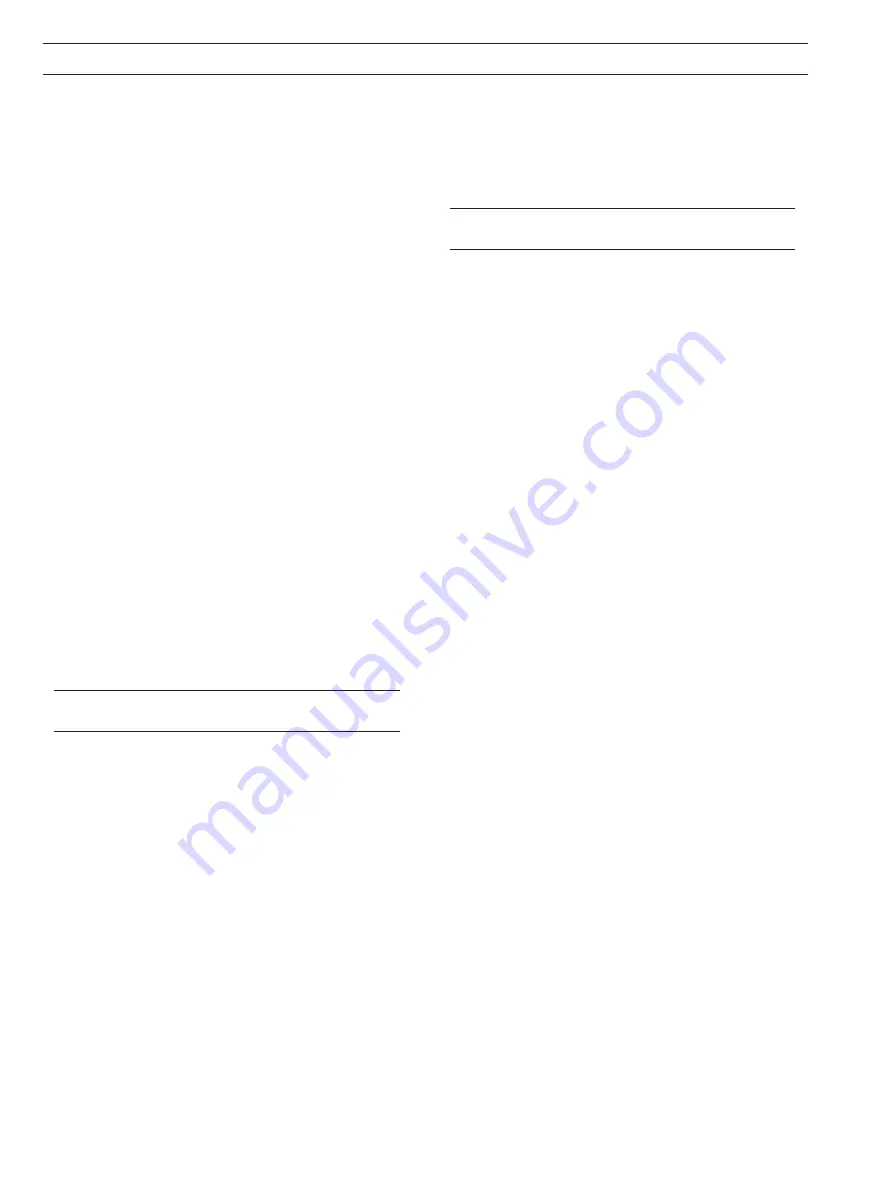
16
6
ROUTINE MAINTENANCE
6.1
‘O’ Ring Seals
Whenever the electrode system is opened at any point, all
'O' rings (especially the lower sensor holder 'O' ring), seals,
washers, etc. should be checked for damage, wear and flexibility,
and unserviceable rings must be replaced. Serviceability very
much depends on the particular application, but regular checking
soon determines an average ring life.
A spare set of 'O' rings is supplied with each system, and
replacement 'O' rings, etc. are available in a Service Pack. Spares
are listed in Section 7.
6.2
Cleaning
When the performance of the electrodes begins to deteriorate,
cleaning may help to restore their original condition. If the cleaning
actions described in this section do not eliminate the deterioration,
either the glass (or redox) electrode, or the sealed reference
electrode or both should be replaced. These steps are described
in Section 6.4.
If the system is fitted with a mechanical or ultrasonic electrode
cleaning device, refer to the instruction manual IM/7600-CLN for
details of cleaning procedures.
During cleaning, avoid rough handling of the pH glass electrode
membrane. Wiping with a soft cloth or tissue soaked in an
appropriate solvent to remove the deposit, or washing with a
strong jet of water are preferred methods – this can be carried out
by removing the electrode holder unit from the process fitting; it
should be unnecessary to remove the electrodes from the sensor
holder. However, where the following cleaning operation requires
an extended period it is advisable to replace the electrode during
cleaning with a new one so that there is a minimum interruption to
the on-line process measurement.
Caution
. Hydrochloric acid is corrosive. Wear
appropriate protective clothing.
1) For general sludge and loosely adhering matter wipe the glass
membrane with cotton wool soaked in 1.0M hydrochloric acid
(or a buffer solution) and then wash in water. Now calibrate the
pH meter.
2) For greasy organic deposits, wipe the glass membrane with
cotton wool soaked in a detergent and rinse thoroughly. If a
sluggish response to pH changes still occurs soak the
electrode for a few hours in 0.1M hydrochloric acid (or a buffer
solution) and then wash in water.
3) For heavy non-greasy deposits, e.g. rust, dip the electrode
briefly in concentrated hydrochloric acid to remove the deposit
and wash thoroughly. Soak the electrode for a few hours in
0.1M hydrochloric acid (or a buffer solution) and then wash in
water. Very heavy deposits formed during effluent
neutralisation are often best removed by using a 1 : 1 mixture
of concentrated hydrochloric acid and water. Pepsin digested
in hydrochloric acid may also be used for protein removal.
4) The Reference Junction of the reference electrode may be
cleaned by washing in water and wiping with a clean cloth.
5) Redox electrodes may be cleaned by any of the previously
described methods; they may also be cathodically cleaned as
follows:
Caution
. Sulphuric acid is corrosive. Wear
appropriate protective clothing.
Degrease the electrode, e.g. with a detergent. Connect the
redox electrode cable to the negative pole of a 6V battery or
power supply. Connect a piece of platinum wire to the positive
pole of the battery or power supply, and dip both electrodes
into a beaker containing 2 to 5% sulphuric acid solution.
Continue electrolysis for approximately 10 minutes. If after
this period the bubbles rising from the redox electrode are not
small and evenly distributed on the immersed parts of the
electrode, repeat the electrolysis.
6.3
Checking the Electrolyte Level
Periodically check the level of electrolyte (about every three
months).
For sealed units remove the electrode holder from the system.
Refer to Fig. 3.8a. Invert the holder and remove the reference
junction. View the electrolyte level through the plug hole and top
up if necessary.
6.4
Replacing Electrodes
6.4.1
Measuring Electrodes
If the pH or redox electrode is no longer serviceable (see Section
6.5) fit a new electrode. The procedure is as follows:
1) For a flow system isolate the system to enable safe access to
the sensors. In the case of a dip system, remove it from its
installed position in the fixing clamp(s).
2) Remove the electrode holder unit from the process fitting (the
protective skirt on a dip system), and take out the sensor
holder from the bottom end of the electrode holder unit.
3) Replace the electrode with a new one following the steps
outlined in Section 3.3.3.
4) Calibrate the pH meter or electrode system as outlined in the
pH meter instruction manual.
5) Install the electrode holder unit.