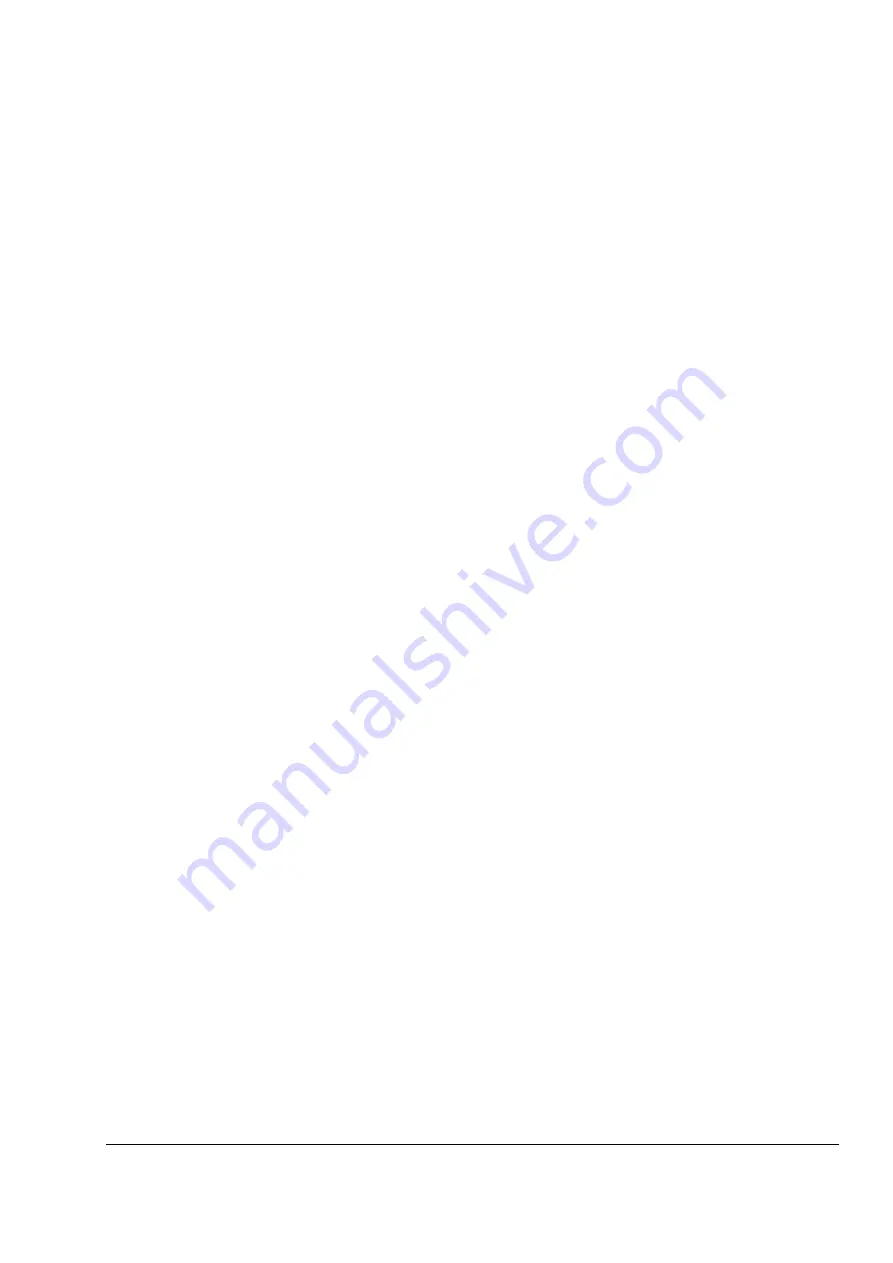
Chapter 3 – AC 80 Software
AC 80 User’s Manual
3-3
AC 80 Software
Support on PC
The AC 80 software support on the PC can be divided into CPU
support and NCB support.
Follow the installation instructions included with each software
package.
AC 80 CPU Support
CPU support requires an RS-232 serial cable between a COM port of
the PC and the Service port of the AC 80.
AC 80 CPU support includes:
•
AC 80 Loader
•
AdvaBuild for Windows (not included with AC 80 deliveries; must be
ordered and installed separately)
•
AC 80 libraries
– Contain the PC and database (DB) elements.
AC 80 Loader
The AC 80 loader downloads the PROM_080.IMG file. This file
contains the current base software.
AdvaBuild
The AdvaBuild for Windows software package contains the Application
Builder (APB), Function Chart Builder (FCB), and Bus Configuration
Builder (BCB) tools. Several versions (but not revisions) of each tool
can be installed on the same PC.
The Application Builder is used for
– creating and modifying projects, or nodes for the AC 80
– invoking the Type Circuit Editor
– invoking the FCB and the BCB
– defining the location of the AC 80 on the AF 100 bus
– selection of AC 80 library version
– selection of required options.
The Function Chart Builder is used for
– creating and modifying application programs
– downloading and saving the application program
– displaying and forcing application program variables (in on-line mode)
– debugging and changing the application program (in on-line mode).
The application program exists on the FCB tool as target code and/or
AMPL source code. The source code can be created from target code
and vice versa.
The Bus Configuration Builder is used for
– getting an overview of targets and messages on the AF 100
– supporting AdvaCommand.
AC 80 Libraries
These libraries include PC and database (DB) elements. The PC and
DB element libraries are delivered in one package including options.
The libraries can be installed together with AdvaBuild. It is also
possible to install them later on using the Application Builder tool.
Summary of Contents for Advant Controller 80
Page 1: ...ABB Drives User s Manual Advant Controller 80 ...
Page 2: ......
Page 4: ......
Page 10: ...vi AC 80 User s Manual ...
Page 34: ...Chapter 2 AC 80 Hardware and Connections 2 20 AC 80 User s Manual ...
Page 51: ...AC 80 User s Manual 4 13 Figure 4 8 The ACSRX PC element ...
Page 82: ...Chapter 5 Diagnostics 5 6 AC 80 User s Manual ...
Page 83: ......