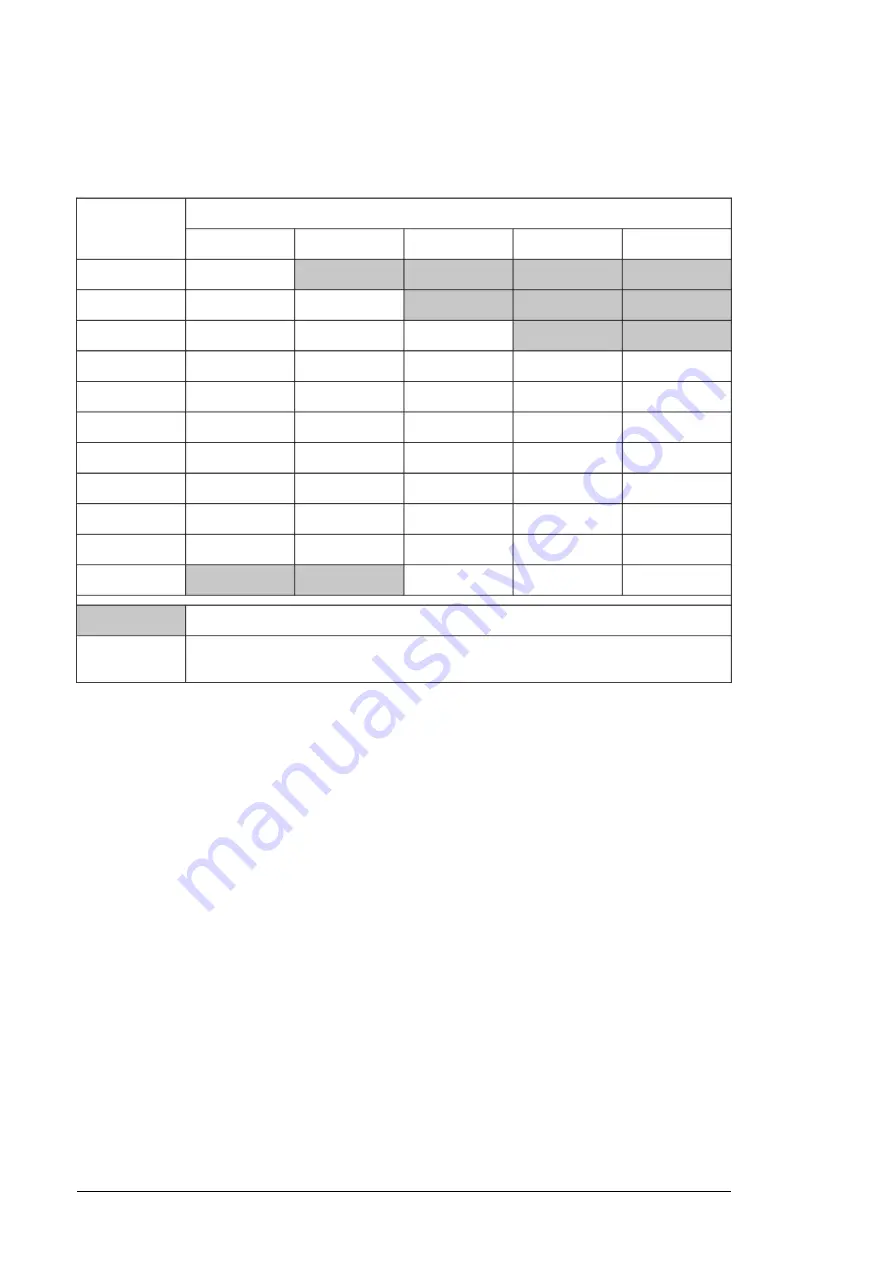
Condensation is not allowed. The minimum coolant temperature to avoid condensation (at
an atmospheric pressure of 1 bar) is shown below as a function of relative humidity (RH)
and ambient temperature (
T
air
).
Min. T
coolant
(°C)
T
air
(°C)
RH = 40%
RH = 50%
RH = 65%
RH = 80%
RH = 95%
-7.4
-4.5
-0.9
1.9
4.3
5
-3.0
-0.1
3.7
6.7
9.2
10
1.5
4.6
8.4
11.5
14.2
15
6.0
9.4
13.2
16.5
19.2
20
10.5
13.8
17.9
21.4
24.1
25
15.0
18.4
22.7
26.2
29.1
30
19.4
23.0
27.4
31.1
34.1
35
23.8
27.6
32.2
35.9
39.0
40
28.2
32.1
36.8
40.8
44.0
45
32.8
36.7
41.6
45.6
49.0
50
37.1
42.2
46.3
50.4
53.9
55
= Not allowed as standard but the coolant temperature must be 0 °C (32 °F) or above.
At an air temperature of 45 °C and relative humidity of 65% the coolant temperature may
not be below +36.8 °C
Example:
Maximum temperature rise:
Depends on heat losses and mass flow. Typically 10 °C (18
°F) with nominal losses and flow.
■
Pressure limits
Base pressure:
250 kPa (recommended); 300 kPa (maximum). “Base pressure” denotes
the pressure of the system compared with the atmospheric pressure when the cooling circuit
is filled with coolant.
Air counterpressure in expansion vessel (with ACS880-1007LC cooling unit):
80 kPa
Design pressure (PS):
600 kPa
Nominal pressure difference:
120 kPa with Antifrogen® L 25% coolant solution, 140 kPa
with Antifrogen® L 50% coolant solution. This has to be taken into account when
dimensioning the liquid cooling circuit.
Maximum pressure difference:
160 kPa
■
Coolant flow rate limits
The maximum coolant flow rate for all drive equipment is 1.3 × nominal. See the technical
data chapter for nominal values.
■
Cooling circuit materials
Materials used in the internal cooling circuit are listed below. These are also the only materials
that can be used in the external cooling circuit.
86 Internal cooling circuit
Summary of Contents for ACS880-607LC
Page 1: ... ABB INDUSTRIAL DRIVES ACS880 607LC 3 phase dynamic brake units Hardware manual ...
Page 2: ......
Page 4: ......
Page 10: ...10 ...
Page 30: ...30 ...
Page 34: ...34 ...
Page 46: ...46 ...
Page 56: ...56 ...
Page 72: ...7 After the module has drained disconnect the piping from the module 72 Maintenance ...
Page 88: ...88 ...
Page 95: ... Bottom entry and exit of cables Dimensions in mm 1 mm 0 0394 in Technical data 95 ...
Page 96: ...Dimensions in mm 1 mm 0 0394 in 96 Technical data ...
Page 97: ... Top entry and exit of cables Dimensions in mm 1 mm 0 0394 in Technical data 97 ...
Page 104: ...Brake unit with bottom exit Dimensions in mm 1 mm 0 0394 in 104 Dimension drawings ...
Page 105: ...Brake unit with top exit Dimensions in mm 1 mm 0 0394 in Dimension drawings 105 ...
Page 106: ...Bottom Top Dimensions in mm 1 mm 0 0394 in 106 Dimension drawings ...