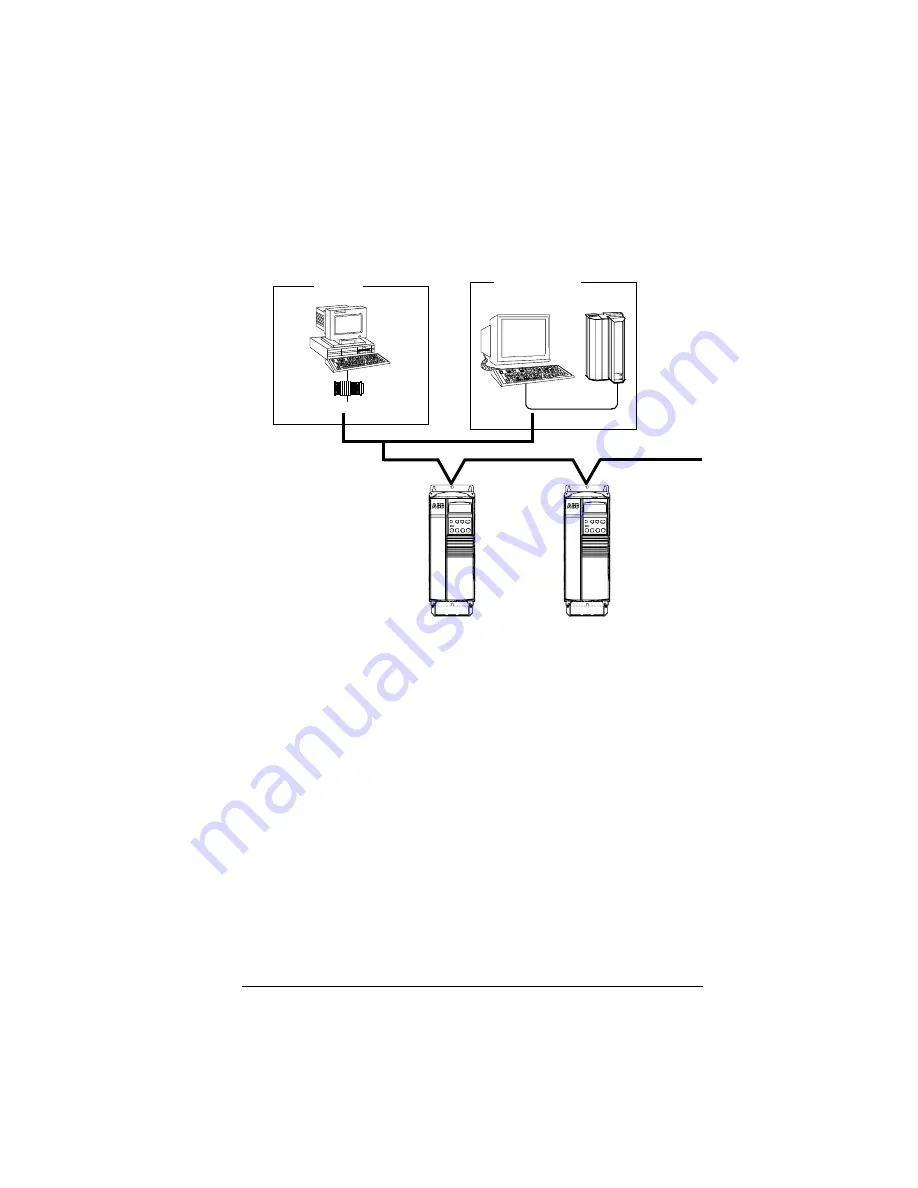
Chapter 2 – Overview of the N2 Connection
ACS/ACH 400 Direct N2 Bus Interface
2-3
Figure 2-2 “ABB and Metasys Companion
Integration” shows the drives’ integration to the
Johnson Controls Metasys Companion system.
Figure 2-2 ABB and Metasys Companion Integration
On the N2 Bus each ACS/ACH 400 drive can
be accessed by the full complement of Metasys
FMS features, including Change-of-State
(COS) monitoring, alarm notification,
scheduling, trend, and totalization.
The ACS/ACH 400 drive has a pre-defined set
of Analog and Binary I/O points. A complete list
of these points is in Appendix A of this manual.
On one N2 Bus segment there can be up to 32
nodes while integrating ACS/ACH 400 drives
with Johnson Controls Metasys. This is less
than the 50 nodes which is the recommended
maximum by Johnson Controls.
Device Type
For the Metasys and Metasys Companion
products, the device type for the ACS/ACH 400
drive is VND.
PC-Version
Converter
Panel Version/LTD
N2 Bus
Summary of Contents for ACH 400
Page 1: ...User s Guide N2 Protocol ACS ACH 400 AC Drives ABB Drives ...
Page 2: ......
Page 4: ......
Page 8: ...Safety Instructions vi ACS ACH 400 Direct N2 Bus Interface ...
Page 36: ...Chapter 5 Fault Tracing 5 4 ACS ACH 400 Direct N2 Bus Interface ...
Page 43: ......