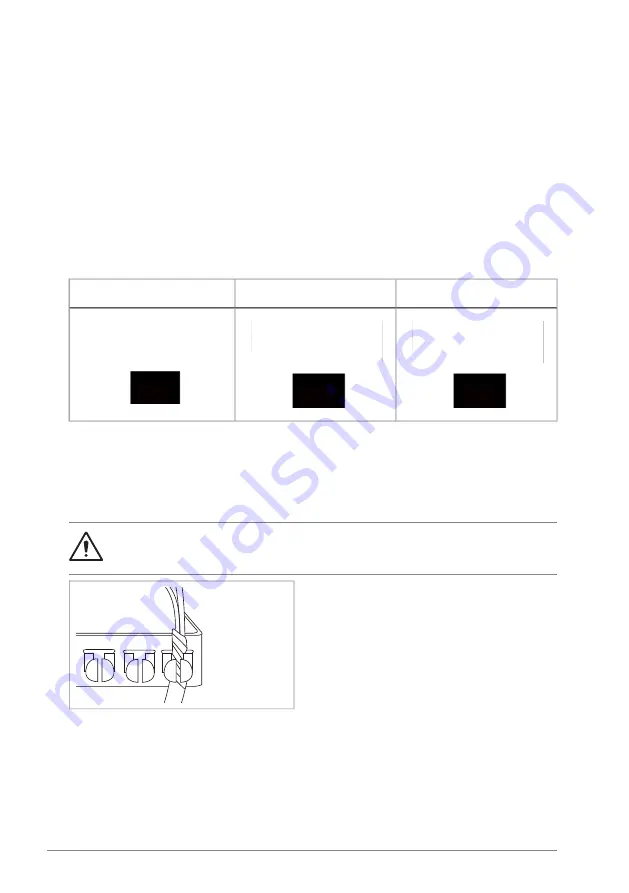
5. The information of RTD cabling inside the MACHsense-R are defined in the
ABB Ability™ Smart Sensor mobile application during commissioning. For more
information, see section
Commission the MACHsense-R (page 32)
.
Make the connections inside the MACHsense-R similar to the predefined order
set in the mobile application, otherwise there may be KPI mismatch in the
Smart Sensor portal. The default configuration for temperature sensors support
the following five RTDs:
•
three stator RTDs, one per phase
•
two bearing RTDs, one for each Drive end and Non-drive end.
6. The wiring of RTD/BTD connections inside the MACHsense-R supports the
following configurations. Connect the cables as per the required configuration.
2-wire
3-wire
4-wire
Note: The RTD temperature sensor for MACHsense-R cannot be shared with
other temperature-measured systems or devices. The connection can be
terminated in the terminal box, from where it can be wired inside the DAU.
7.
Place the cable shield in the clamp for EMI protection.
WARNING! Make sure the clamp has proper earthing for EMI protection.
60 Connecting temperature sensors
Summary of Contents for Ability MACHsense-R
Page 1: ...ABB MOTION SERVICES ABB Ability MACHsense R MSR1608 Data acquisition unit User manual...
Page 2: ......
Page 4: ......
Page 8: ...8...
Page 12: ...12...
Page 18: ...18...
Page 20: ...Process overview diagram 20 Getting started...
Page 26: ...26...
Page 34: ...34...
Page 42: ...42...
Page 46: ...46...
Page 50: ...50...
Page 58: ...58...
Page 66: ...66...