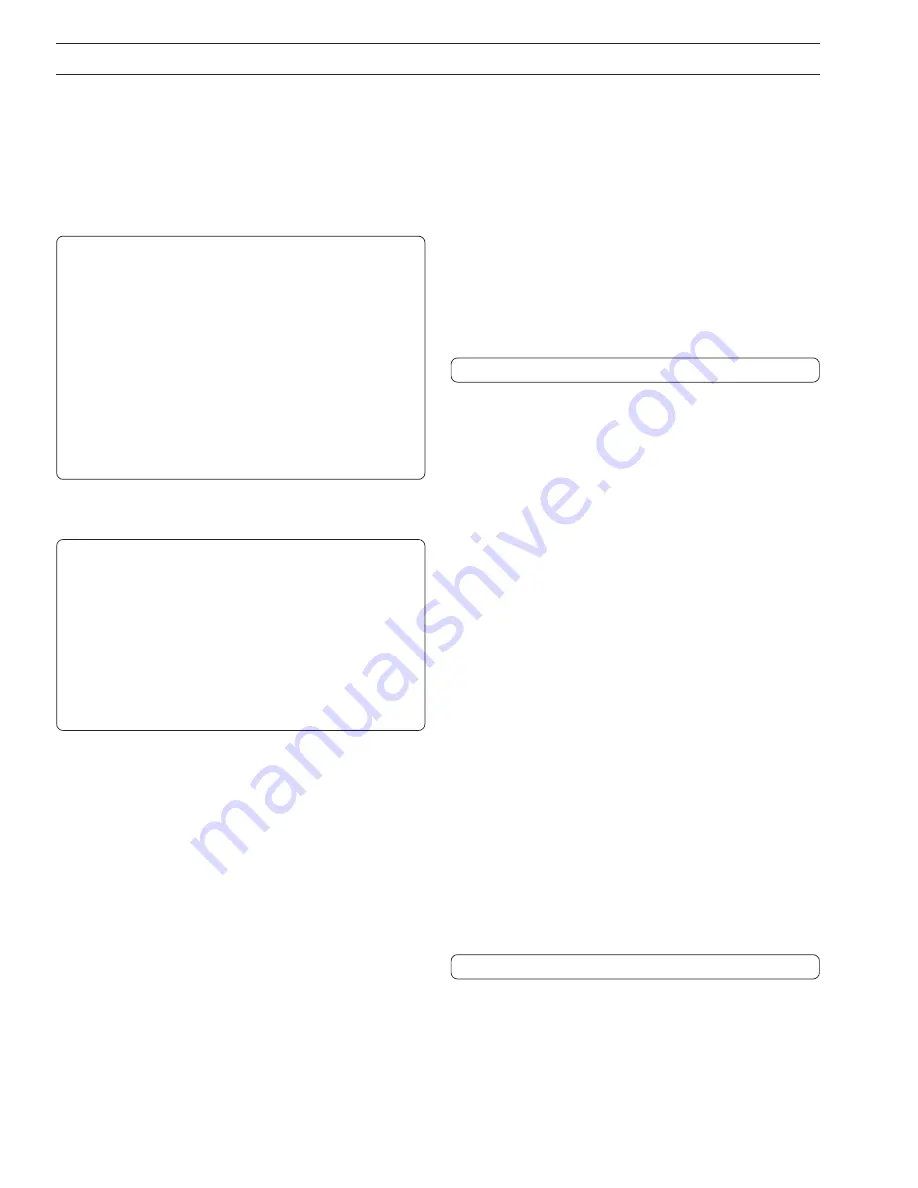
28
8.1
Introduction
No routine maintenance is required for this instrument other than
periodic calibration – see Section 6.2.2. However, if following a
calibration the sensor output shows one flashing bar, the sensor
capsule has therefore become exhausted and needs replacing
immediately.
If the output shows two bars, replace the sensor capsule in the
near future.
Storage
DO:
— use sensors in date rotation to prevent them being
stored longer than necessary.
— at all times, store sensors in a dry and cool environment.
— store sensors in a refrigerator to extend their life, but DO
NOT allow them to freeze.
DO NOT:
— allow sensors to dry out, either in storage or in use.
— leave sensors in vehicles where they are likely to freeze
or be exposed to high temperatures.
— leave sensors on-site without protection from direct sun
or high temperatures.
— use the sensor if it's sealed environment has dried out.
A dirty membrane may also be the cause of the low sensor
output. To clean the sensor proceed with the following.
Caution.
• Only install the oxygen sensor immediately prior to use,
otherwise leave it stored in its protective container.
• Take special care to line up the two pins in the oxygen
sensor with their respective sockets before making the
connection and tightening.
• Take care not to damage the delicate membrane on the
end of the oxygen sensor.
• Ensure that the mating surfaces (carrying the electrical
connection) of the oxygen sensor and connector body are
clean and
completely
dry.
8.2
Cleaning/Changing the Sensor
8.2.1
Cleaning
1) Drain the flowcell, by manually opening the solenoid valve -
Select YES to 'Open Valve' on the main operating page of
the transmitter. See Section 6.2.1.
2) Unscrew the clamping screw and carefully remove the
sensor assembly from the flowcell. Check that O-ring does
not fall out.
8
MAINTENANCE
3) Inspect the sensor. If the membrane is clean, refit the sensor
as in 5) below.
If deposits are visible on the membrane, remove by gently
wiping the membrane with a moist paper tissue; for oily or
greasy deposits, the tissue may be moistened with a mild
detergent or, if necessary with iso-propyl alcohol (propan-2-
ol). After cleaning, dry the interior of the flowcell with a paper
tissue or soft cloth, ensure that the O-ring is correctly
positioned.
4) Insert the sensor assembly into the flowcell.
5) Use the clamp screw to secure the assembly. Screw in firmly
using finger pressure only.
Caution.
Do not overtighten the clamping screw.
6) Close the solenoid valve – Select NO to 'Open Valve' on the
main operating page of the transmitter. See Section 6.2.1.
7) Carry out a calibration – see Section 6.2.2. If a low sensor
efficiency is displayed, see Section 9.2.
8.2.2
Changing the Sensor
1) Drain the flowcell, by manually opening the solenoid valve –
Select YES to 'Open Valve' on the main operating page of
the transmitter. See Section 6.2.1.
2) Unscrew the clamping screw and remove the sensor
assembly from the flowcell.
3) Disconnect the sensor capsule and discard both the sensor
and sealing washer.
4) Take out the O-ring from the flowcell; dry the interior of the
flowcell with a tissue or soft cloth and insert the new O-ring
supplied with the replacement capsule. Ensure that the O-
ring is correctly located on the shoulder near the end of the
cavity.
5) Remove the new sensor from its container, taking care not to
damage the membrane. Unscrew the protective cap from
the rear of the sensor.
6) Fit the new sealing washer (supplied) as shown in Fig 4.1 and
locate and secure the connector body on the sensor.
7) Insert the complete assembly into the flowcell.
8) Use the clamping screw to secure the assembly. Screw in
firmly using finger pressure only.
Caution.
Do not overtighten the clamping screw.
9) Close the solenoid valve – Select NO to 'Open Valve' on the
main operating page of the transmitter. See section 6.2.1.
10) Carry out a calibration – see Section 6.2.2. If a low sensor
efficiency is displayed, see Section 9.2.