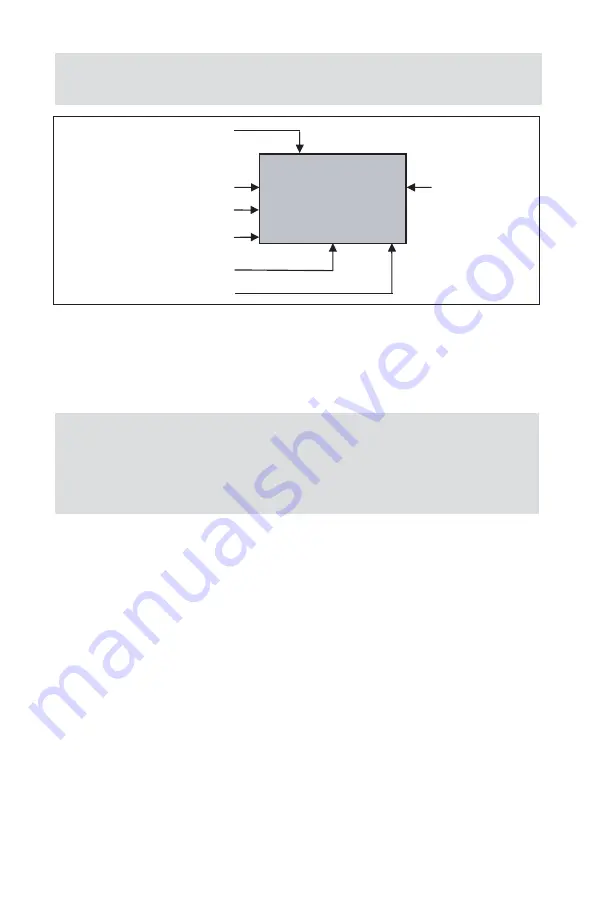
17
NOTE: Before executing, the program should be entered in the
program table (see Paragraph 5.3.16)
,
NOTE: While Program Set Point mode is running, the current Set
Point value also can be changed from local LCD/keypad and digital
RS-232/RS-485 communication interface. In this case, new Set Point
value will be kept only until the next successive program step is
executed.
,
51.01 litr/min
S 51.0 0.0s
CS: 1 0.0 0
M:D L:Off S: Off
Current SP value
Current program step
Program Mode: E/D
Program Loop Mode: On/Off
Program Run Status: On/Off
Current step time
elapsed
Current flow rate value
As shown in the above drawing the Program Run parameter can be toggled “On”
or “Off” by pressing the
RIGHT
and
LEFT
keypad buttons, while PI screen #4 is
active. If Program Run status parameter is set to “Off”, the program execution will
pause and current SP value will freeze until Program Run status parameter is set
to “On”.
5.2 Menu
Structure
The diagram on the Figure 5.7 gives a general overview of the standard top-level
display menu structure when running firmware version A001. The
ESC
pushbutton
is used to toggle between the Process Mode (PI screens) and the Setup menus.
UP
and
DN
buttons must be used to move through the menu items. When the last
item in the menu is reached, the menu “wraps around” and scrolls back to the
beginning of the menu items list. Similarly, when the first menu item is highlight-
ed and the
UP
button is pressed, the menu “wraps around” and scrolls down to
the end of the menu item’s list.
All process configuration parameter’s settings are password-protected. In order to
access or change them, Program Protection should be disabled. Each time the
device is powered up, the Program Protection is enabled automatically. By default,
the device is shipped from the factory with the Program Protection (PP) password
set to Zero (PP Disabled). If PP password is set to Zero (Disabled), entering a PP
password is not required. A subsequent screen will appear and the Program
Protection menu item will be selected:
Summary of Contents for TIO
Page 14: ...10 Figure 4 3 RS 485 Multidrop Half Duplex Two Wire System...
Page 55: ...51 Figure 6 2 Connecting TIO to the GFM using 0 5 Vdc output from DB9 connector...
Page 56: ...52 Figure 6 3 Connecting TIO to the GFM using 5 10 Vdc output from RJ11 connector...
Page 57: ...53 Figure 6 4 Connecting TIO to the GFM using 4 20 mA output from DB9 connector...
Page 61: ...58 Figure 6 6 Connecting TIO to the GFC Using 0 5Vdc Input Output from DB15 Connector...
Page 62: ...59 Figure 6 7 Connecting TIO to the GFC Using 4 20mA Input Output from DB15 Connector...
Page 68: ...65 Figure 6 9 Connecting TIO to the Generic Flow Meter...
Page 69: ...66 Figure 6 10 Connecting TIO to the Generic Flow Controller...
Page 95: ...92 APPENDIX D Mechanical Drawings...
Page 96: ...93 APPENDIX E Circuit Layout Diagrams Circuit Layout Top...