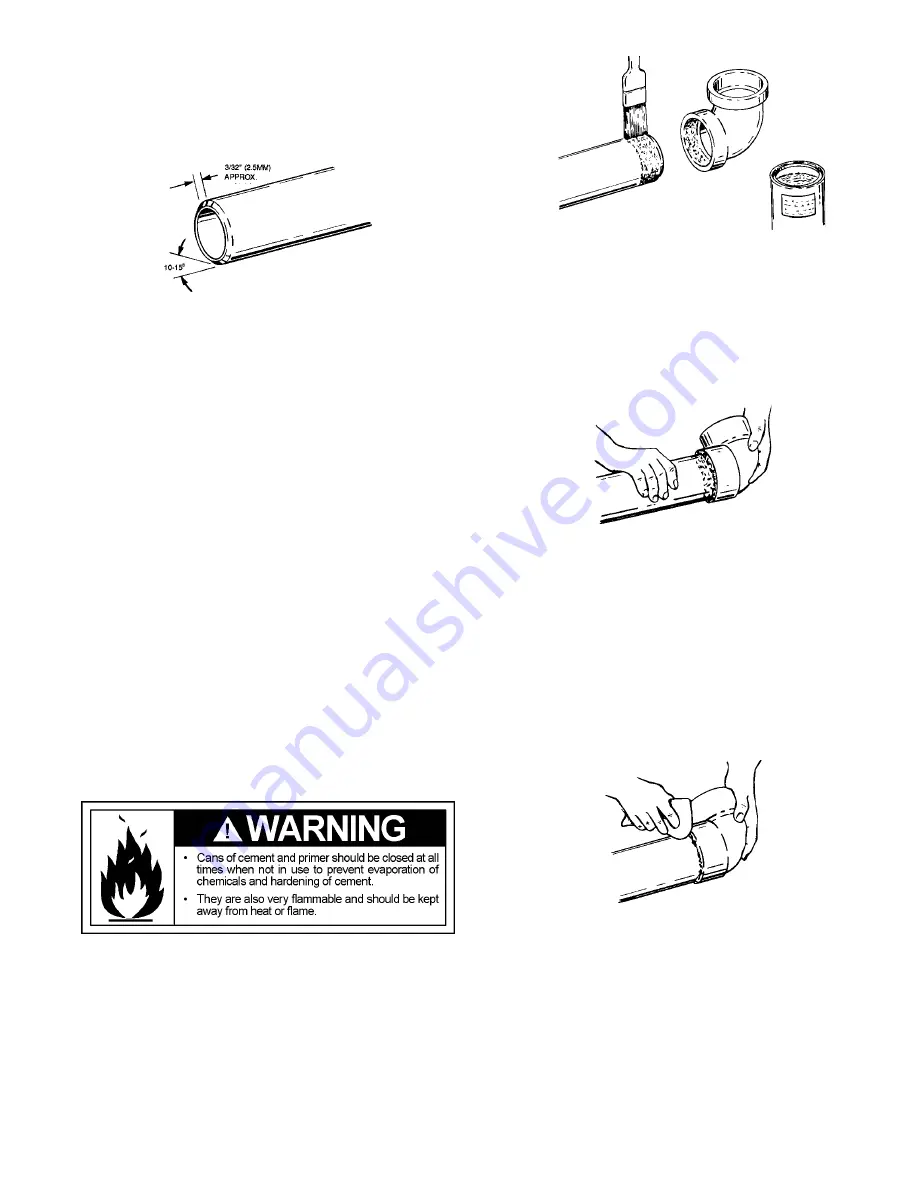
25
B. Deburring
Use a knife, plastic pipe deburring tool, or file to remove burrs from the
end of small diameter pipe. Be sure to remove all burrs from around the
inside as well as the outside of the pipe. A slight chamfer (bevel) of about
10°-15° should be added to the end to permit easier insertion of the pipe
into the end of the fitting. Failure to chamfer the edge of the pipe may
remove cement from the fitting socket, causing the joint to leak.
STEP B
C. Test dry fit of the joint
Tapered fitting sockets are designed so that an interfaced fit should
occur when the pipe is inserted about 1/3 to 2/3 of the way into the
socket. Occasionally, when pipe fitting dimensions are at the tolerance
extremes, it will be possible to fully insert dry pipe to the bottom of the
fitting socket. When this happens, a sufficient quantity of cement
must be applied to the joint to fill the gap between the pipe and fitting.
The gap must be filled to obtain a strong, leak-free joint.
D. Inspection, cleaning, priming
Visually inspect the inside of the pipe and fitting sockets and remove
all dirt, grease or moisture with a clean dry rag. If wiping fails to
clean the surfaces, a chemical cleaner must be used. Check for
possible damage such as splits or cracks and replace if necessary.
Depth-of-entry
Marking the depth of entry is a way to check if the pipe has reached
the bottom of the fitting socket in Step F. Measure the fitting depth
and mark this distance on the pipe O.D. You may want to add
several inches to the distance and make a second mark as the
primer and cement will most likely destroy your first one.
Apply primer to the surface of the pipe and fitting socket with a natural
bristle brush. This process softens and prepares the PVC or CPVC for
the solvent cementing step. Move quickly and without hesitation to
the cementing procedure while the surfaces are still wet with primer.
E. Application of solvent cement
• Apply the solvent cement evenly and quickly around the outside of
the pipe at a width a little greater than the depth of the fitting socket.
• Apply a light coat of cement evenly around the inside of the
fitting socket. Avoid puddling.
• Apply a second coat of cement to the pipe end.
STEP E
F. Joint assembly
Working quickly, insert the pipe into the fitting socket bottom and
give the pipe or fitting a 1/4 turn to evenly distribute the cement.
Do not continue to rotate the pipe after it has hit the bottom of the
fitting socket. A good joint will have sufficient cement to make a
bead all the way around the outside of the fitting hub. The fitting
will have a tendency to slide back while the cement is still wet so
hold the joint together for about 15 seconds.
STEP F
G. Cleanup and joint movement
Remove all excess cement from around the pipe and fitting with
a dry cotton rag. This must be done while the cement is still soft.
The joint should not be disturbed immediately after the cementing
procedure, and sufficient time should be allowed for proper curing
of the joint. Exact drying time is difficult to predict because it
depends on variables such as temperature, humidity and cement
integrity. For more specific information, you should contact your
solvent cement manufacturer.
STEP G