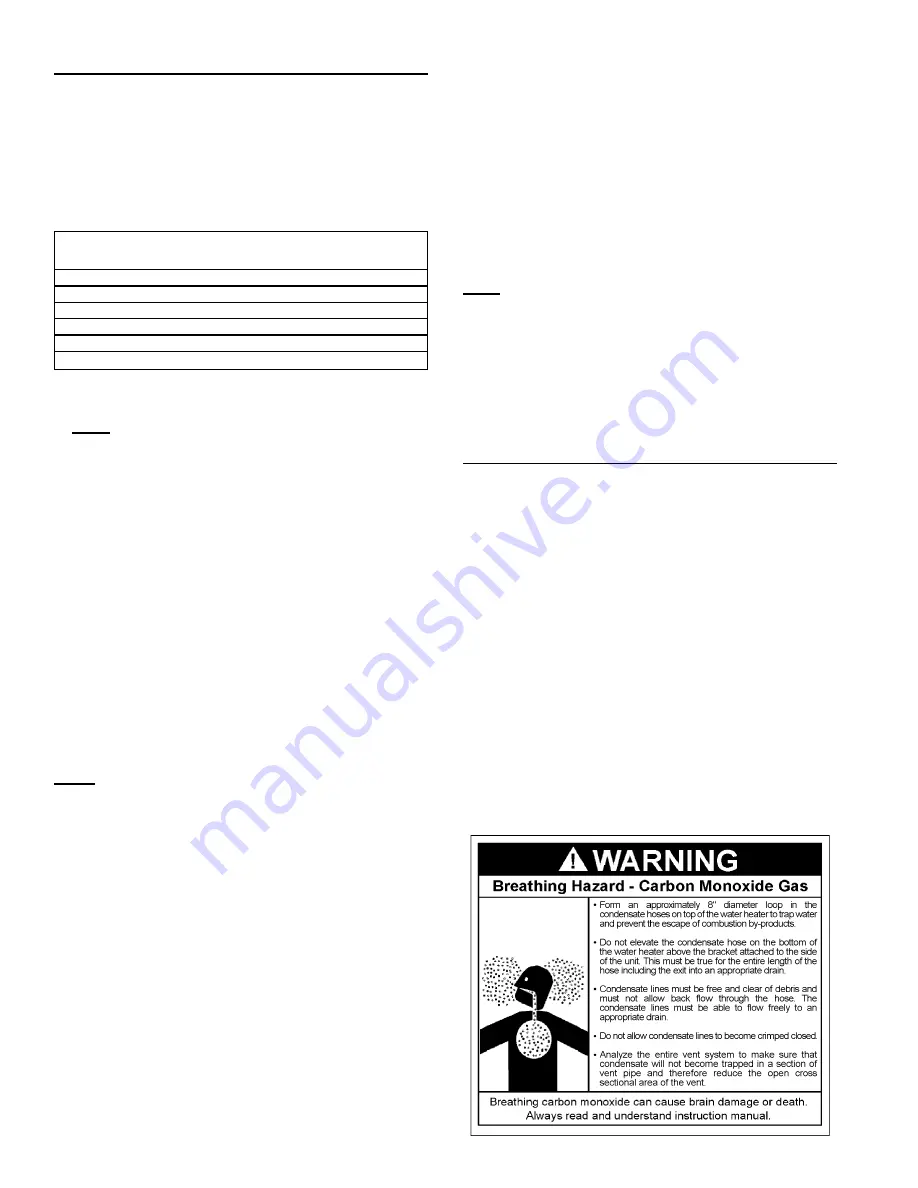
18
PLANNING THE VENT SYSTEM
Plan the route of the vent system from the discharge of the blower to
the planned location of the vent terminal.
1. Layout total vent system to use a minimum of vent pipe and elbows.
2. This water heater is capable of venting flue gases equivalent to 25'
(7.6 m) of 2" pipe, 65' (19.8 m) of 3" pipe, or 128' (39.0 m) of 4" pipe
as listed in Table 1.
TABLE 1
Number of
2" Maximum
3" Maximum
4" Maximum
90° Elbows
Pipe - ft. (m)
Pipe - ft. (m)
Pipe - ft. (m)
1
20 (6.1)
60 (18.3)
120 (36.6)
2
15 (4.6)
55 (16.8)
112 (34.1)
3
10 (3.0)
50 (15.2)
104 (31.7)
4
--
45 (13.7)
96 (29.3)
5
--
40 (12.2)
88 (26.8)
6
--
35 (10.7)
80 (24.3)
The minimum vent lengths for each of the pipe sizes is one 90° on top of
the unit plus 2' (61 cm) of straight pipe and the appropriate termination.
NOTE: The equivalent feet (m) of pipe listed above are exclusive of
the termination. That is, the termination, with an installed screen, is
assumed to be in the system and the remainder of the system must
not exceed the lengths discussed above.
3. The blower discharge adapter is made to accept only straight
sections of 2" pipe. To start, a minimum of 2 inches (5.1 cm) of 2"
pipe must be attached to the blower discharge, see Figure 17.
If using 2" inch vent pipe:
A minimum of 2 inches (5.1 cm) must be attached to the blower
before the first elbow. After the first elbow add the additional
venting required for the installation. The total system cannot
exceed the lengths discussed above, where each elbow is
equal to 5 feet (1.5 m) of straight pipe.
If using 3" or 4" inch vent pipe:
Two inches (5.1 cm) of pipe must be attached to the blower discharge
before adding a reducer to acquire the desired pipe diameter. An
appropriately sized 45 degree elbow (supplied locally-a schedule 40
DWV) vent terminal must be obtained with an equivalent screen (supplied
in vent kit). The total system cannot exceed the equivalent pipe lengths
discussed above where each elbow is equal to 5 feet (1.5 m) of straight
pipe (3" vent pipe) or 8 feet (2.4 m) of straight pipe (4" vent pipe).
U.S. Installations
NOTE: This unit can be vented with PVC pipe materials (Cellular Core
ASTM-F891; DWV ASTM-D2665 or CSA B181.2; Schedule 40, 80, 120
ASTM-D1785 or CSA B137.3; or SDR Series ASTM-D2241 or CSA B137.3),
CPVC pipe materials (CPVC41 ASTM-D2846 or CSA B137.6; Schedule
40, 80 ASTM-F441 or CSA B137.6; or SDR Series ASTM-F442), ABS pipe
materials (Schedule 40 DWV ASTM-D2661 or CSA B181.1 or Schedule
40 DWV Cellular Core ASTM-F628). The fittings, other than the TERMINATION
should be equivalent to PVC-DWV fittings meeting ASTM D-2665 (Use
CPVC fittings, ASTM F-438 for CPVC pipe and ABS fittings, ASTM D-2661/
3311 for ABS pipe). If CPVC or ABS pipe and fittings are used, then the
proper cement must be used for all joints, including joining the pipe to the
Termination (PVC Material). If local codes do not allow the use of the PVC
termination when a material other than PVC is used for venting, then an
equivalent fitting of that material may be substituted if the screen in the PVC
terminal is removed and inserted into the new fitting.
PVC Materials should use ASTM D-2564 Grade Cement; CPVC Materials
should use ASTM F-493 Grade Cement and ABS Materials should use
ASTM D-2235 Grade Cement.
Canadian Installation of this water heater must comply with CAN/CSA
B149.1 - Natural Gas and Propane Installation Code which requires
the vent system components be certified to ULC S636.
This water heater has been design certified to be vented with PVC
pipe certified and marked as complying with ULC S636. This water
heater is supplied with a 2 inch 22.5 degree termination elbow that is
a special fitting that must be used with this appliance. Any outlet
piping, fittings and glue used to vent this appliance that is not supplied
by the manufacturer must comply with the ULC S636 requirements.
If the water heater is being installed as a replacement for an existing power
vented heater in pre-existing venting, a thorough inspection of the existing
venting system must be performed prior to any installation work. Verify that
the correct material as detailed above has been used, and that the minimum
or maximum vent lengths and terminal location as detailed in this manual
have been met. Carefully inspect the entire venting system for any signs of
cracks or fractures, particularly at the joints between elbows and other
fittings and the straight runs of vent pipe. Check the system for signs of
sagging or other stresses in the joints as a result of misalignment of any
components in the system. If any of these conditions are found, they must
be corrected in accordance with the venting instructions in this manual
before completing the installation and putting the water heater into service.
NOTE: A. For water heaters in locations with high ambient temperatures
(above 100°F) it is recommended that CPVC or ABS pipe and fittings be used.
B. A 22.5 degree elbow (2" vent pipe) or a 45 degree elbow (3" and 4" vent
pipe) with an installed screen VENT TERMINAL must be used in all cases.
4. There will be some installations where condensate will be formed in
the horizontal runs of the vent system. This condensate will run into
the condensate boot attached to the blower and out the fitting. The
water heater is shipped with condensate hose that attaches to the
fitting on the condensate boot. No other Tee or fitting is required. See
Figures 17, 20 and 21.
CONDENSATE
This water heater is a condensing unit and requires a drain to be located
in close proximity to allow the condensate to drain safely. The condensate
drains from the unit at the exhaust tee located at the bottom of the unit
(see figure 16) and from two places on the blower assembly (see figure
17). Condensate from this water heater is mildly acidic. Please note that
some local codes require that condensate is treated by using a pH
neutralizing filter prior to disposal.
NOTE: It is important that the condensate hose on the bottom of the unit is
not installed elevated above the clamp that is secured to the side of the
jacket, see figure 16. This must be true for the entire length of the hose
from the clamp to the exit into an appropriate drain. If these instructions are
not followed or if the condensate hose is blocked, water will spill from the
condensate trap. As with every water heater installation, a drain pan
should be used to prevent water damage to the surrounding area. If
necessary, a condensate pump with an incorporated reservoir may be
used to pump the water to an appropriate drain. To avoid condensate
spillage, select a pump with an overflow switch.
Caution must be used to ensure that the drain is free and clear of
debris and will not allow backflow through the condensate hose. Consideration
must be given to avoid freezing of the condensate lines which could result in
excessive build up of condensate inside the water heater. Waterproof heat
tape may be required to prevent freezing of the condensate lines. Please
ensure that the outlet of the condensate drain does not create a slippery
condition which could lead to personal injury.