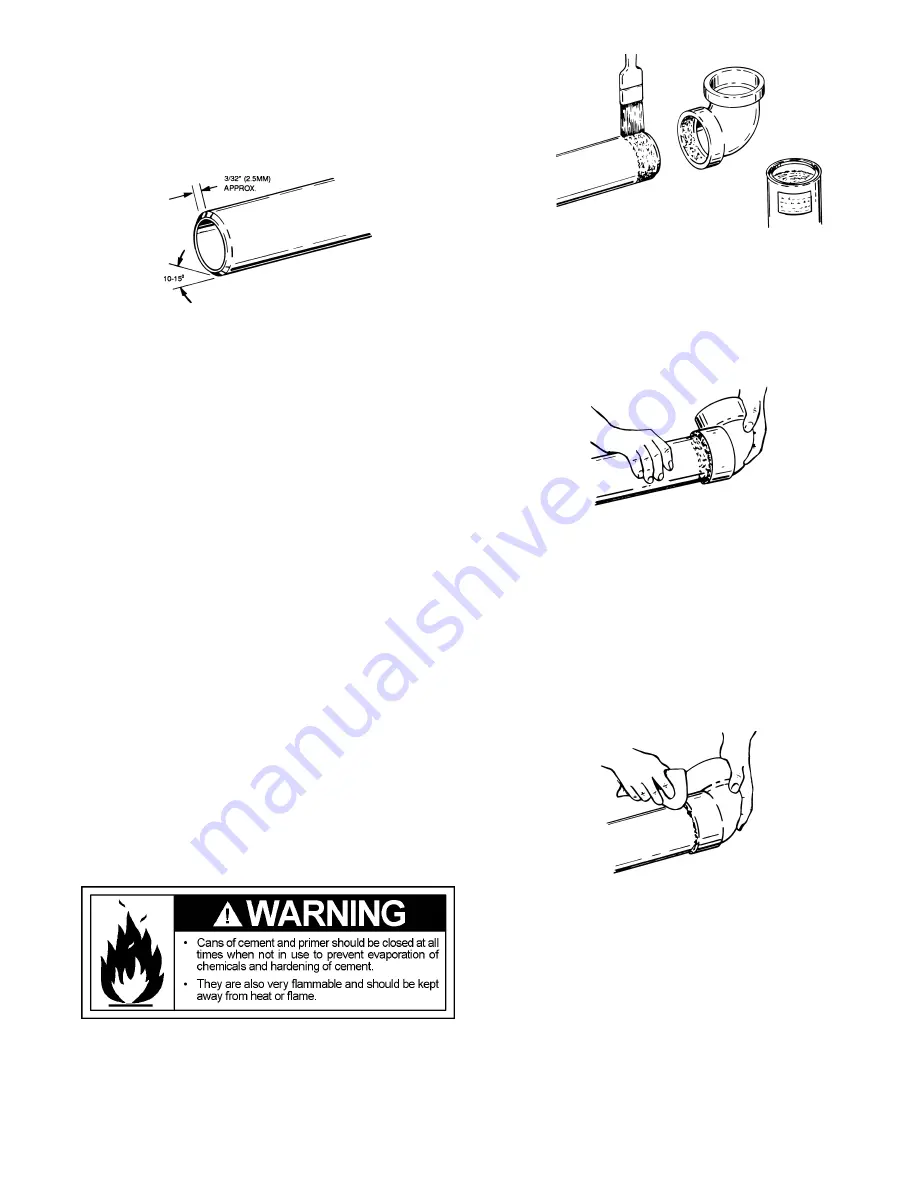
20
B. Deburring
Use a knife, plastic pipe deburring tool, or
fi
le to remove burrs
from the end of small diameter pipe. Be sure to remove all burrs
from around the inside as well as the outside of the pipe. A slight
chamfer (bevel) of about 10°-15° should be added to the end to
permit easier insertion of the pipe into the end of the
fi
tting. Failure
to chamfer the edge of the pipe may remove cement from the
fi
tting
socket, causing the joint to leak.
STEP B
C. Test dry
fi
t of the joint
Tapered
fi
tting sockets are designed so that an interfaced
fi
t should
occur when the pipe is inserted about 1/3 to 2/3 of the way into
the socket. Occasionally, when pipe
fi
tting dimensions are at the
tolerance extremes, it will be possible to fully insert dry pipe to the
bottom of the
fi
tting socket. When this happens, a suf
fi
cient quantity
of cement must be applied to the joint to
fi
ll the gap between the
pipe and
fi
tting. The gap must be
fi
lled to obtain a strong, leak-free
joint.
D. Inspection, cleaning, priming
Visually inspect the inside of the pipe and
fi
tting sockets and
remove all dirt, grease or moisture with a clean dry rag. If wiping
fails to clean the surfaces, a chemical cleaner must be used.
Check for possible damage such as splits or cracks and replace
if necessary.
Depth-of-entry
Marking the depth of entry is a way to check if the pipe has reached
the bottom of the
fi
tting socket in Step F. Measure the
fi
tting depth
and mark this distance on the pipe O.D. You may want to add
several inches to the distance and make a second mark as the
primer and cement will most likely destroy your
fi
rst one.
Apply primer to the surface of the pipe and
fi
tting socket with a
natural bristle brush. This process softens and prepares the PVC
or CPVC for the solvent cementing step. Move quickly and without
hesitation to the cementing procedure while the surfaces are still
wet with primer.
E. Application of solvent cement
• Apply the solvent cement evenly and quickly around the outside
of the pipe at a width a little greater than the depth of the
fi
tting
socket.
• Apply a light coat of cement evenly around the inside of the
fi
tting socket. Avoid puddling.
• Apply a second coat of cement to the pipe end.
STEP E
F. Joint assembly
Working quickly, insert the pipe into the
fi
tting socket bottom and
give the pipe or
fi
tting a 1/4 turn to evenly distribute the cement.
Do not continue to rotate the pipe after it has hit the bottom of the
fi
tting socket. A good joint will have suf
fi
cient cement to make a
bead all the way around the outside of the
fi
tting hub. The
fi
tting
will have a tendency to slide back while the cement is still wet so
hold the joint together for about 15 seconds.
STEP F
G. Cleanup and joint movement
Remove all excess cement from around the pipe and
fi
tting with a
dry cotton rag. This must be done while the cement is still soft.
The joint should not be disturbed immediately after the cementing
procedure, and suf
fi
cient time should be allowed for proper curing of
the joint. Exact drying time is dif
fi
cult to predict because it depends
on variables such as temperature, humidity and cement integrity.
For more speci
fi
c information, you should contact your solvent
cement manufacturer.
STEP G