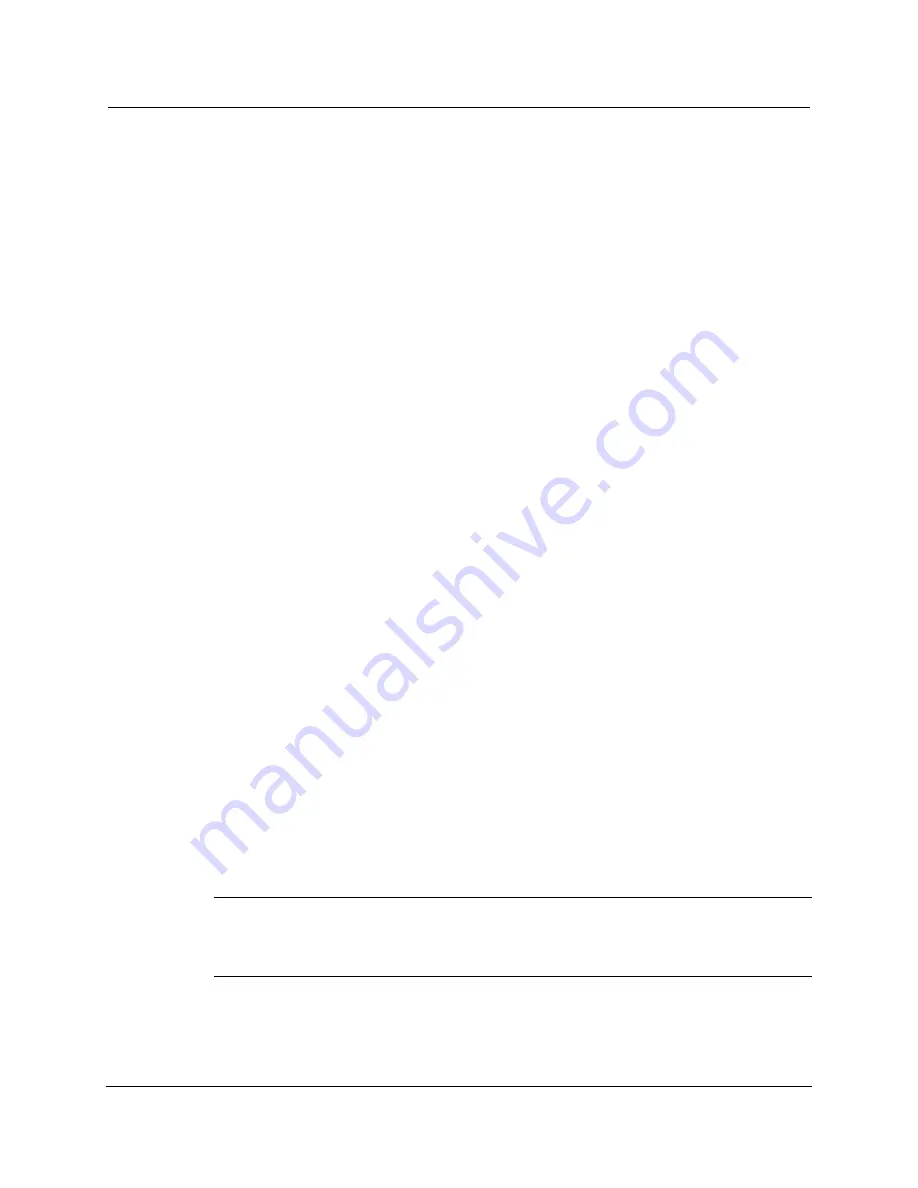
3M™ MicroTouch™ Controller EX Dual Mode Reference Guide
29
3M Touch Systems, Inc. Proprietary Information – TSD-40848A
CHAPTER 4
3M™ MicroTouch™ EX Serial
Communications
This chapter discusses the fundamentals of communicating with the 3M™ MicroTouch™
EX serial controller. The firmware commands, which are usually issued by a driver or
utility program on the host system, control the operation of the touch controller however
developers can enter these commands directly. This chapter:
•
Describes the controller default settings.
•
Lists the recommended firmware commands for current development.
•
Describes how to use each of these commands.
•
References additional commands developers may need to use.
The description of each command includes the command syntax, the default value, how
the command works, and the expected response from the controller.
Overview of Firmware Commands
Developers may use these commands when writing touch applications, developing
custom drivers or touch configurations, or testing their touch systems. Developers can
issue commands to initialize the controller, select operating modes, and execute
diagnostic functions.
Most sensor users do
not
have to use firmware commands to use their touch systems. For
example, users can use MT 7 software to calibrate the sensor or to determine the
controller type and firmware version.
Note:
This document assumes you are familiar with standards and modes of
communication with serial devices, as well as firmware commands and how to use them.
Executing some commands may alter the performance of your sensor and render it
inoperable. You should be aware of the results before executing any firmware commands.
To optimize the performance of the 3M™ MicroTouch™ EX touch controller and
simplify the development of custom drivers, 3M Touch Systems recommends you use the
commands listed in this chapter for current development. Using these commands ensures
compatibility with all 3M™ MicroTouch™ controllers.