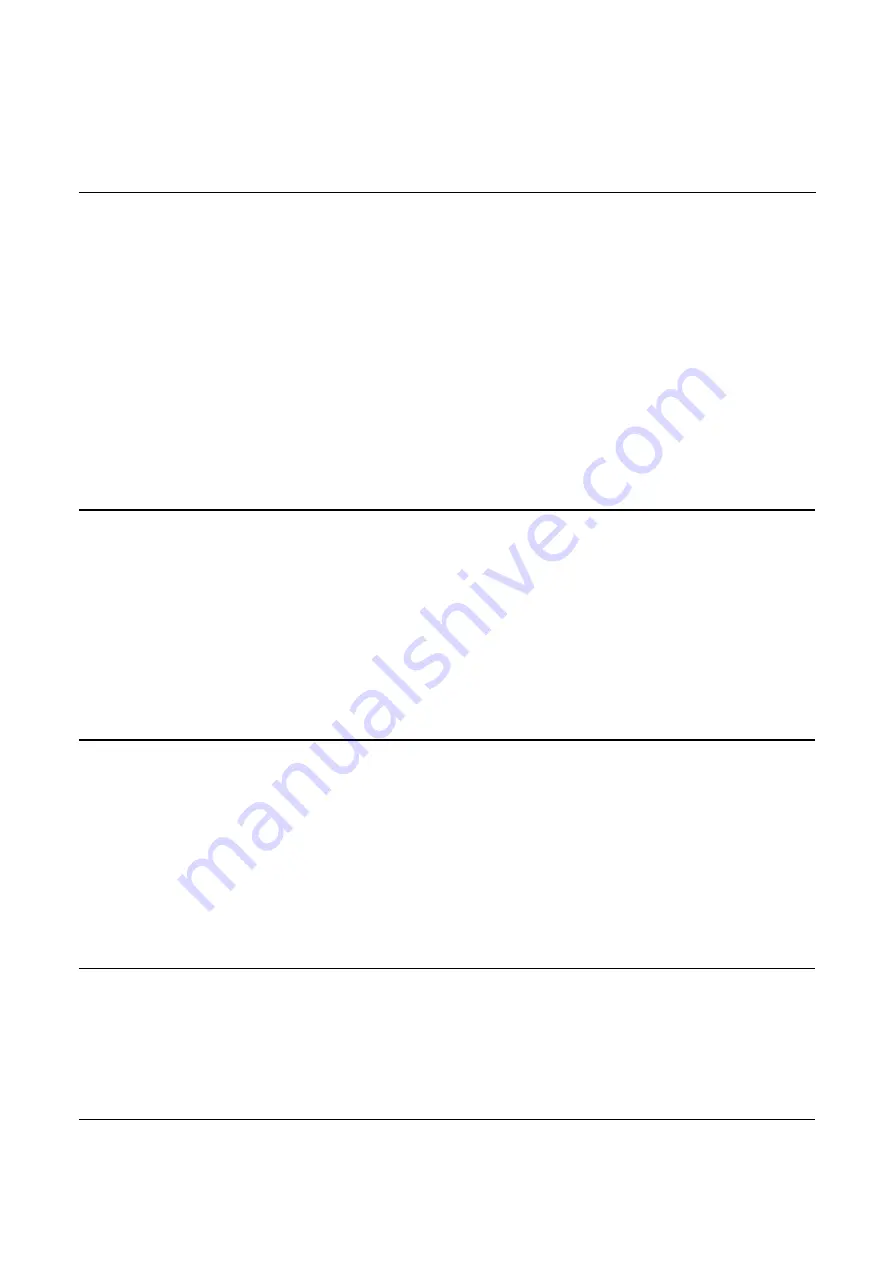
34
Troubleshooting Guide
Troubleshooting
(Continued)
Problem
Upper drive assembly does not
move up or moves up slowly
Upper taping head does not move
down at the end of the taping
cycle
Upper drive assembly comes
down too fast or too hard
Centering guides move slower
than normal
Cause
Lower air pressure
Defective head raising valve
Worn head raising valve actuator
Clogged or damaged exhaust
mufflers on the upper ends of the
head raising cylinders
Defective head power valve
Upper drive assembly force
adjust regulator set too light
Defective top drive assembly
force adjust regulator
Defective one-way valve
Defective head power valve
Upper drive assembly force
adjust regulator set too heavy
Defective upper drive assembly
force adjust regulator
Cushion screw misadjusted
Cushion screw missing
Centering guide force adjust
regulator set too low
Centering guide cylinder speed
controls not in correct adjustment
Defective centering guide power
valve
Correction
Disconnect the air supply. Make
sure main pressure regulator reads
zero. Reconnect air supply and
adjust regulator to read 70 PSIG
[5 bar].
Clean or replace head raising
valve
Replace valve
Clean or replace exhaust mufflers
Clean or replace the head power
valve
Adjust the upper drive assembly
force adjust regulator to increase
the force against the top of the
box. Turn air regulator
counterclockwise.
Replace regulator
Clean or replace valve
Clean or replace valve
Adjust upper drive assembly force
adjust regulator to decrease force
against top of box. Turn regulator
clockwise.
Replace regulator
Adjust cushion screw at base of
cylinder
Replace screw
Adjust regulator
Adjust speed controls mounted on
centering guide cylinder
Clean or replace valve
Summary of Contents for Matic 700r
Page 33: ...28 THIS PAGE IS BLANK ...
Page 45: ...40 THIS PAGE IS BLANK ...
Page 46: ...41 700r Random Case Sealer Frame Assemblies ...
Page 47: ...42 700r Random Case Sealer Figure 2807 ...
Page 49: ...44 700r Random Case Sealer Figure 3437 ...
Page 51: ...46 700r Random Case Sealer Figure 3439 ...
Page 53: ...48 700r Random Case Sealer Figure 5670 ...
Page 55: ...50 Figure 5916 1 of 2 700r Random Case Sealer ...
Page 57: ...52 Figure 5916 2 of 2 700r Random Case Sealer ...
Page 59: ...54 700r Random Case Sealer Figure 5917 ...
Page 61: ...56 Figure 5918 1 of 2 700r Random Case Sealer ...
Page 63: ...58 700r Random Case Sealer Figure 5918 2 of 2 ...
Page 65: ...60 700r Random Case Sealer Figure 5919 ...
Page 67: ...62 700r Random Case Sealer Figure 5920 ...
Page 69: ...64 700r Random Case Sealer Figure 5921 ...
Page 71: ...66 Safety and Information Labels 700r Random Case Sealer ...