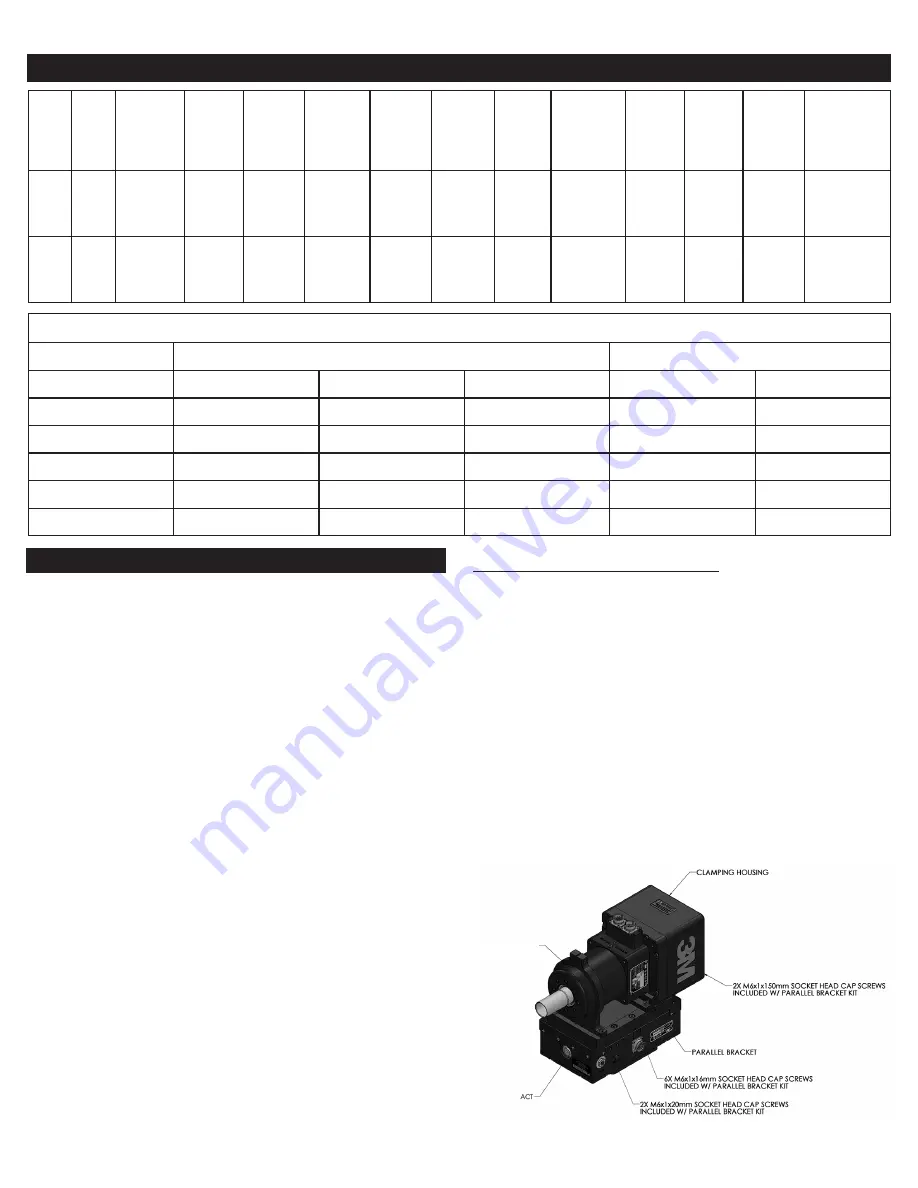
3
General Overview
The 3M Model 06531 13300 RPM, 3 HP and 3M Model 06532 6000 RPM, 5 HP Servo Rotary
Tool share many common components. The 13300 and 6000 RPM motors are capable of
continuously producing 3 and 5 horsepower respectively. The motors use a BT30 Toolholder
which allows changing out tools and media. Each of these motors provide a convenient and
effective means to spin and/or change any number of different media types to support a fully
automated workcell.
These automatic tool-changing models actuate pneumatically to secure the BT30 style
Toolholder. They are comprised of four primary components: a high-torque Servo Motor, a
pneumatic actuator, high force Belleville springs, and a component to clamp a Toolholder.
These models use a drawbar to pull the Collet/Gripper in. High force Belleville springs located
at the back of the Servo Motor tension the drawbar. Actuating the large pneumatic actuator,
located in the Clamping Housing, opens the Collet/Gripper. During pressurization the cylinder
contacts the Belleville springs and compresses them to drive the Collet/Gripper out, releasing
the Toolholder. There is no mechanism to forcibly eject the Toolholder from the Collet, so
gravity or a capturing mechanism must be used. Both models use a 30 taper to grip a
standard BT30 Toolholder. This design locks the Toolholder in the 30 tapered shaft and resists
large pull out forces. The shaft does not have locking keys, so motor indexing for tool change
is not required.
These automatic tool-changing motors are fail-safe, in that no air pressure is required to hold
the Toolholder. Therefore, the Toolholder will remain held in the Collet/Gripper even when
the air pressure is unexpectedly lost. Likewise, applying air pressure to a single input port
via a simple manual or electrically operated valve opens the Collet/Gripper and releases the
Toolholder. The design always isolates the motor bearings from the drawbar tension. This
greatly improves reliability by allowing the motor shaft to spin freely and never be subject to
any clamping forces. Both motors use sealed bearings to ensure a long life. The bearings have
additional contamination protection from a contact shaft seal. This special seal eliminates the
need for constant purge air.
During operation these motors generate considerable heat due to their high torque and
compact size. Excessive operating temperatures will significantly reduce the life of the motors.
Water Cooling is required to keep the unit within the internal temperature operating range.
The motor should never be allowed to exceed a temperature of 176˚F (80˚C). Continuously
operating the unit above 176˚F (80˚C) will cause the rotor to de-magnetize and the bearings to
fail. High temperatures will also cause the O-rings that seal the cooling water channels to fail,
possibly filling the motor with water. Flow through water cooling is provided on the motor to
allow high duty cycles without overheating.
Product Configuration / Specifications
Operating / Maintenance Instructions
Model
Power
HP
(kW)
Continuous
Stall
Torque
lb.-ft. (N·m)
Full Load
(A)
Maximum
Speed
RPM
Speed
Regulation
%
Shaft
Maximum
Axial
Load lb.
(N)
Shaft
Maximum
Radial
Load lb.
(N)
Weigh
lb. (kg)
Operating
Temperature
Optimal,
Maximum
F (C)
Thermal
Cutoff F
(C)
Max.
Coolant
Pressure:
PSI (Bar)
Insulation
Amplifier Type
06531
3
(2.2)
2.57 (3.5)
15.0
13300
5
Reversible
150 (666)
300
(1332)
28
(12.7)
122, 176
(60, 80)
212
(100)
60 (4.1)
Class F
(155°C)
Kollmorgen
®
Servo Amplifier
13300, 3M PN
06547
06532
5
(3.7)
5.6 (7.6)
19.5
6000
5
Reversible
150 (666)
300
(1332)
28
(12.7)
122, 176
(60, 80)
212
(100)
60 (4.1)
Class F
(155°C)
Kollmorgen
®
Servo Amplifier
0605, 3M PN
06545
Fastener Tightening Torque Specs
Torque
Minimum Depth
Fastener Size
in.-lbs.
ft.-lbs.
N-m
in.
mm
M4 x .7
50
4.2
5.6
0.17
4.3
M5 x .8
85
7.1
9.6
0.21
5.3
M6 x 1
140
11.7
15.8
0.25
6.3
M8 x 1.25
348
29.0
39.3
0.33
8.4
M10 x 1.5
600
50.0
67.8
0.41
10.5
Installation & Operation
Mounting the 3M rotary tool to a 3M ACT compliant tool
The tools are designed to attach directly to the Carriage of 3M ACT (Active Compliant Tool),
using the Parallel Mounting Kit Model 06533.
The Parallel-Axis configuration is shown in Figure 1, where the tool attaches to the ACT
Carriage with the Parallel Mounting Kit. The Parallel Mounting Kit is positioned on the Carriage
and attached using the four (4) supplied M6x1x20mm Socket Head Cap Screws. The tool is
then attached to the Parallel Mounting Kit as shown, with two (2) M6x1x20mm Socket Head
Cap Screws into the front of the Motor Housing. Two (2) M6x1x145mm Socket Head Cap
Screws pass through the Clamping Housing/Mounting Plate. The fasteners must be tightened
to the torque specified in the Technical Specifications Section.
To attach the tool to an ACT in a Perpendicular-Axis configuration, position the Clamping
Housing/Mounting Plate over the Carriage as shown in Figure 2. Then secure the unit using
four (4) M6x1x145mm Socket Head Cap Screws. Tighten the fasteners to the torque specified
the Technical Specifications Section. 5mm Dowel pins can be inserted and glued into the
Carriage to align the motor. The Clamping Housings and Mounting Plate have predrilled
clearance dowel holes for this configuration.
NOTICE: Make sure that the M6x1 fasteners do not exceed a depth of 0.40” (10 mm) into
the ACT Carriage Helicoils or damage will occur.
NOTICE: Do not press Dowel Pins into the ACT Carriage, this will damage the linear rails.
3M 06531
3M 06532
Figure 1. Spindle Motor Parallel-Axis Configuration