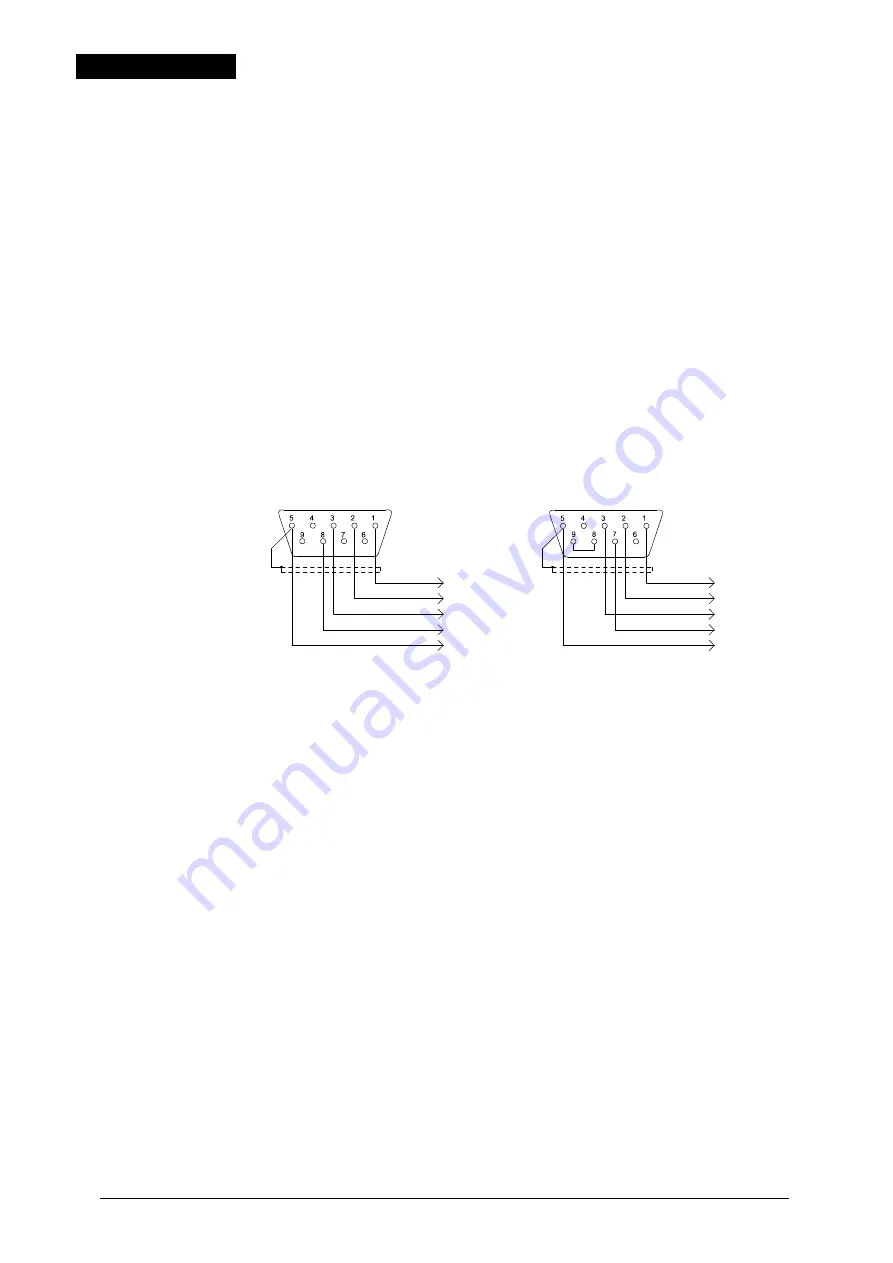
End Switch
zub machine control AG
Manual MK1/100
·
Hardware Installation
Seite 5
MK1/100
You can now carry out a test of the end switch. After activation of the end switch, an error
must occur and the red Error LED must be lit.
In order to enquire about the error, open the error enquiry window as described above. The
error message "End switch reached" must appear. Delete the error message with
ESC
and
J
(for Yes).
Switch off the power supply, before you connect the encoder to the
MK1/100
.
For error-free operation it is necessary for the encoder to be connected with the
MK1/100
via
a shielded cable. In making the connection it is important to keep the cables as short as
possible and to route them as far away from power cables as possible. Encoders with TTL or
open collector outputs can be used, which have a supply voltage of 5 V.
The precise allocation of the encoder jack and the significance of the signals (temporal trends
and interrelationships) can also be found in the hardware reference section.
The encoder is mounted on the motor shaft. In order to test the encoder, it is necessary that
the motor shaft is able to move freely.
The motor must not be connected during this test.
In order to test the encoder in a simple way at first, carry out an APOS test program. Select
the APOS menu item
File
→
Load.
With the keys
Pos1
and
End,
select the document "DREHGTST.M“. You can also enter the
name of the document directly. The entry must be completed with the
Enter
key.
After the APOS program has been loaded, it must be started as follows:
Leave the Editor window with the
ESC
key. Then select the menu
Execute
→
Start program
with the
cursor
keys and the
Enter
key. When the
Enter
key is pressed, the program is
processed.
In the output window, you will now see a new position value displayed every half a second.
After a full revolution of the motor shaft by hand, the position value should amount to four
times the encoder count per turn. For instance, if the encoder count per turn is 500, you
should receive a position value of
±
2000. After a further revolution in the opposite direction,
the position value should be zero.
End Switch
Incremental Encoder
! ! !
! ! !
Encoder with
negative
index impulse
Encoder
Encoder with
positive
index impulse
Encoder
+ 5 V
track A
track B
/Index
GND
screen
+ 5 V
track A
track B
/Index
GND
screen
Z&B Werkbild: mk1drehb
to the encoder
to the encoder
bridge