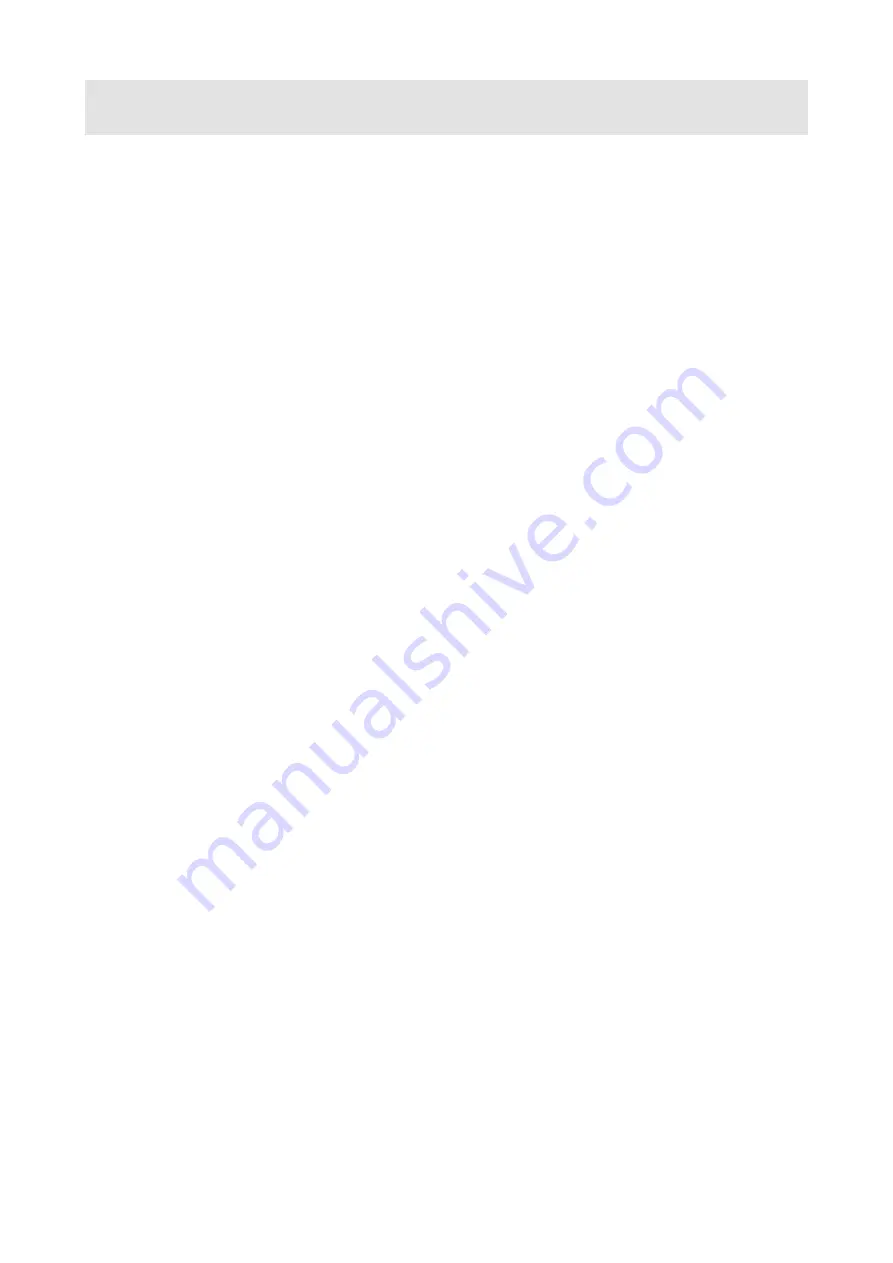
11
12. PREVENTIVE INSPECTIONS AND ACTUATOR REPAIRS
FOR NUCLEAR POWER STATIONS
Actuators life for nuclear power station - line MOA OC is determined to 40 years according to technical conditions.
Based realized qualifying examinations and longtime experiences from operation is recommended by the actuator
manufacturer to realize during product life following range and periods of preventive inspections and repairs:
1. Preventive inspections and revisions of actuator – once in 3 years
is realized at actuator operator and includes these actviities:
– visual inspection of actuator, if it is not broken, corroded, inspection of seal condition, fastening condition, check
tighness of the cable grommets, tightening screw connections. In case of defects finding, remove these defects or
determine the procedure of its removal.
– after unscrewing the motor cover and terminal box and control box cover in actuator will be realized visual inspection
of connection and conductors marking, check of internal wiring parts in actuator, tightning terminal box connections,
check of protection conductors connections and check of conductors from protective interconnection system.
– check transition resistance of protective conductor connections – R_trans < 0,1 Ohm.
– check the unit on control box – transmission unit, control springs, circumeference of cam drive and lever mechanism
is necessary to lubricate by the fat Ciatim 221. Add oil PP80 or equivalent oil to the gear-case.
– make functional test of extreme positions by remote or local electrical control, while doing so to check adjustment
and function of position, torque and signalling switches and adjustment of position indicator and position transmitter.
Remove identified failures in adjustment and in function or determine the procedure for its remove.
2. Small repairs – in case of loss of functionality or damage
– at the actuator operator is possible to do small repairs - as for examle replacement of injured or worn parts like seal,
microswithces, motor, bearings, gear wheels etc. Only professionally trained staff with valid certificate for this activity
can do this activity.
3. Total actuators rebuild
(general repair)
– total actuators rebuild
(general repair)
is done in case of big actuator failure or in old actuators and substantially worn
actuators. Its purpose is put actuator into condition approaching the new actautor with guaranteed technical
parameters.
– repair of this extension is recommanded to do at operationally important positions and emergency system positions,
which are long-term exposed of increased thermal effects of radiant heat or corrosive effects for the purpose to keep
permanent device reliability for throughout of determined lifetime
(e.g. hermetical zones spaces inaccessible during
operation, partially or fully closed spaces of steam pipe, outdoor spaces etc.)
– this activity can be done only by actuator manufacturer, in exceptional cases by manufacturer determined and
trained service organization.
– for making rebuild activities are estabilished technological procedures at the manufacturer, but its way and range
always depends on assessement of actuator state and requirements of customer.
General repirs includes in most cases these activities:
– replacement of sealing elements
(guferos and o-rings)
– replacement of lubricants
– replacement of torque springs
– replacement of control units, eventually of whole control board
– replacement of connecting material
–
at big rebuilds, concerning to large quantities and actuator types, is suitable the rebuild procedure mutually agree
and arrange the way of verification
(e.g. inspection and testing plan by rebuilt actuators).