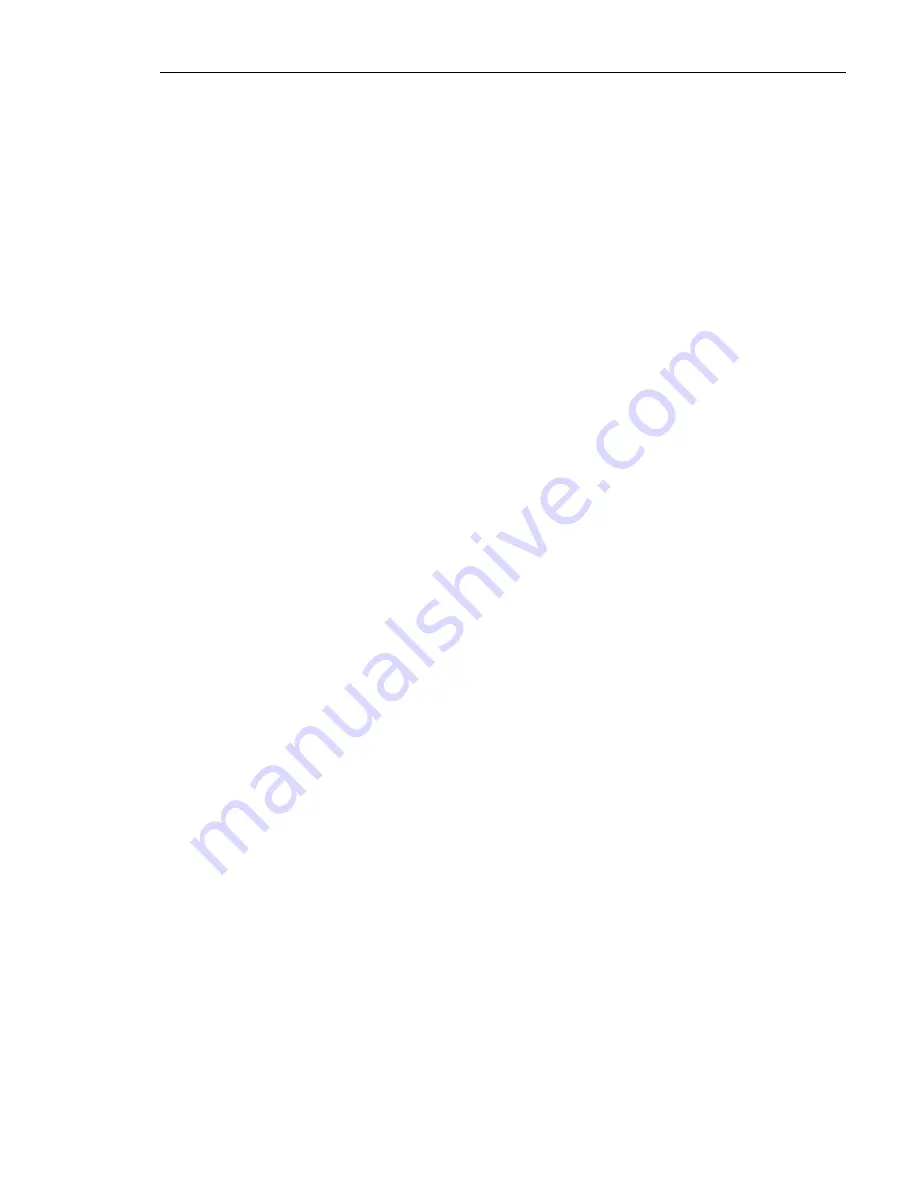
FUNCTIONAL DESCRIPTION
IV-12
Battery Capacity Output (optional)
Output control line P0.4 (U104.24) is used to develop an analog output that is
proportional to the capacity of a battery that has been tested. The microprocessor's
port line P0.4 is configured as a pulse width modulated output which is filtered by the
R131 and C128 R/C network. The resulting DC voltage is buffered by amplifier
U105B and bussed to connector J101.2. R113 is a current limiting resistor inserted
for protection against accidental shorts. C121 is an RF bypass capacitor.
4. LED PCB
The LED PCB assembly provides the user interface to each of the four charging
compartments within the Base PowerCharger
4x4
system. A ribbon cable running from
J2 of the main PCB to P4 on the LED PCB carries the signals that drive the status
LED's and test switches for each charging compartment.
Located on this assembly are four test switches; SW1 - SW4 (one for each charging
compartment), a power on indicator (LED171 or 172) and four sets of status indicators
(LED1 - LED4 for charging compartment 1, LED5 - LED8 for charging compartment 2,
LED9 - LED12 for charging compartment 3 and LED13 - LED16 for charging
compartment 4). All of the drive and interface electronics for these devices are
located on the main PCB and are described in the Display Drive Circuitry section and
the Test Switch Interface Circuitry.
Power Up Operation
At power on, the POWER indicator will turn on. The controller for each channel will
perform a series of power-on diagnostics (including a test of the four LED's) and then
advance to the appropriate mode based on whether a fault is detected, a battery is
present, and the status of the test switch. See
Diagnostics
Section for a detailed
description of the power-on diagnostics.
If a fault is detected, the controller will revert to the FAULT Mode. Any power brown-out
(< 90VAC) or interruption will cause a charging sequence to be restarted when proper
power is re-established.
If a test is in progress during a power brown-out or interruption the controller will revert to
normal operation when proper power is re-established. Press the
TEST
button to start
the testing cycle again.
Turn on Delay
The system will delay no more that 10 seconds after power on to allow the battery/power
electronics to stabilize and go through a self test. The
CHARGER ON
indicator will be
turned on after the delay, if a battery is present.
Содержание Base Powercharger 4x4
Страница 1: ...9650 0072 01 Rev E ZOLL Base Powercharger 4x4 Service Manual...
Страница 8: ...GENERAL INFORMATION I 7 SEE FILE PG7_C PM5 FOR THIS PAGE AND ALL OF THE SYMBOLS...
Страница 11: ...GENERAL INFORMATION I 10...
Страница 13: ...CHECKOUT PROCEDURES 9650 0072 II 2 Rev D...
Страница 39: ...SCHEMATIC DRAWINGS V 2...
Страница 49: ...COMPONENT LAYOUT DRAWINGS VI 2...
Страница 53: ...DISASSEMBLY PROCEDURES VII 2...
Страница 55: ...DISASSEMBLY PROCEDURES VII 4...
Страница 57: ...DISASSEMBLY PROCEDURES VII 6...
Страница 58: ...DISASSEMBLY PROCEDURES VII 7...
Страница 60: ...DISASSEMBLY PROCEDURES VII 9...
Страница 62: ...DISASSEMBLY PROCEDURES VII 11...
Страница 63: ...DISASSEMBLY PROCEDURES VII 12...
Страница 65: ...DISASSEMBLY PROCEDURES VII 14...
Страница 67: ...DISASSEMBLY PROCEDURES VII 16...
Страница 71: ...REPLACEMENT PARTS VIII 4...
Страница 73: ...A 2 Base PowerCharger4x4 Operator s Guide...
Страница 75: ...B2 Base PowerCharger4x4 Operator s Guide...