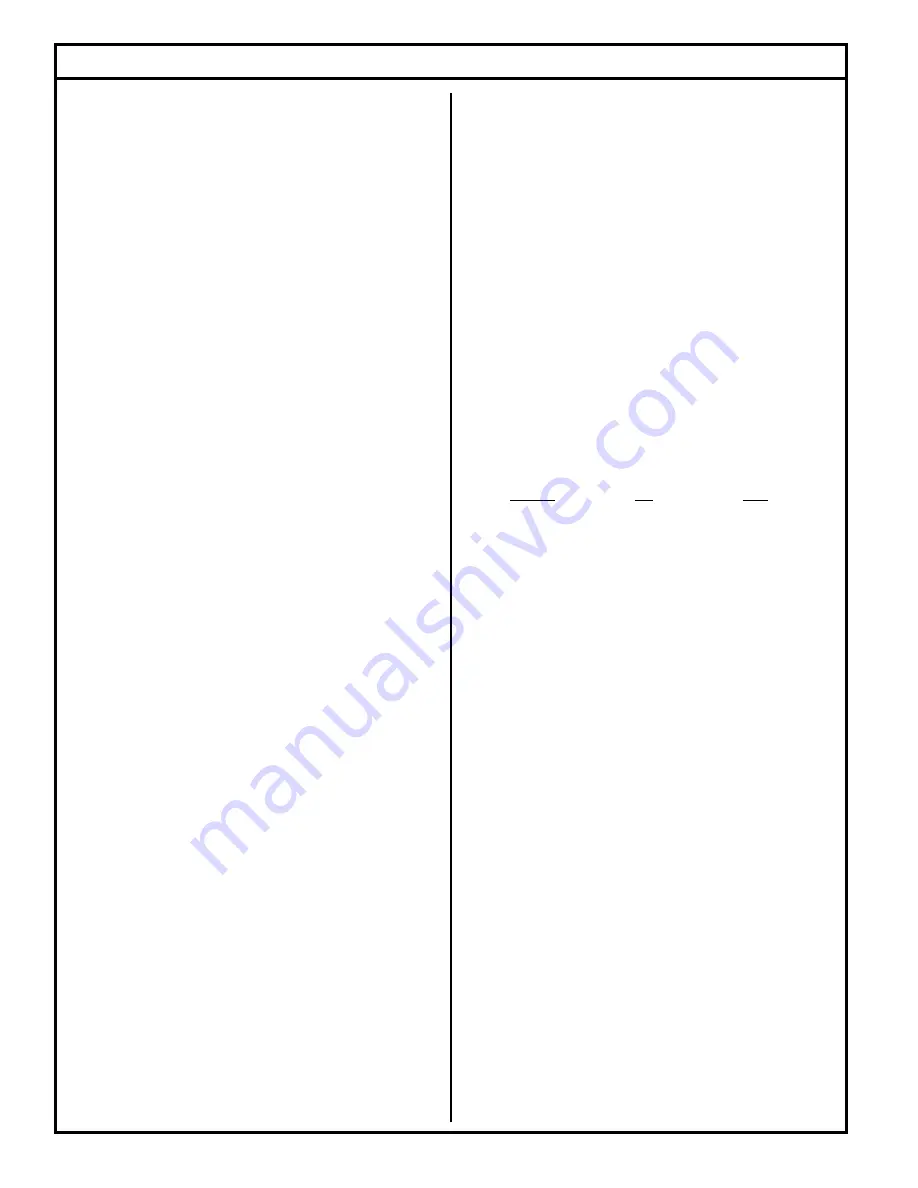
10
© Copyright 2010 Zoeller Co. All rights reserved.
Operation
GENERAL
Zoeller pumps are lubricated and tested at the factory prior to shipment
and require minimum pre-start-up maintenance.
Maximum operating temperature of pump liquid must not exceed 104°F
(40°C).
These units are not designed to handle liquids other than effl uent: 160
and 180 or sanitary sewage: 280, 290 and 400. If pump is used to de-
water areas with contaminated liquids with heavy or abrasive ma te ri als,
the warranty will be void ed.
NAMEPLATE DATA
The nameplate, located on the side of the pump, indicates spe cifi c
in for ma tion about the construction of the pump. The model num ber
and date code information should be recorded on the front page in the
“Owner’s Information” section of this manual.
SHORT TERM STORAGE
When not in use, the pump should be stored and the following is
ad vised:
• Store pump inside whenever possible or cover with some type of protective
cov er ing.
• Tape or seal in plastic bag the terminal ends of wire leads.
• Spray coat unpainted surfaces with rust inhibiting oil.
• The impeller should be rotated every six months in order to keep the
seals lubricated and not develop a permanent set.
If panel is to be stored, the following is advised:
• Store the panel inside whenever possible and leave in the ship ping
box.
• All openings shall be sealed.
• Store in an upright position.
• Do not stack anything on top of panel.
START-UP PROCEDURE
Before placing the equipment into operation the following should be
checked:
• Clean pit.
• Electrical boxes dry and securely installed.
• Floats positioned properly.
• Discharge valves open.
• 3/16” vent hole drilled in pipe between check valve and pump.
Once the above has been verifi ed proceed with the following checks:
• Pump power cables and control fl oats properly installed and voltage
verifi ed.
• Conduit connections to panel are properly sealed.
• After installing the pump into the containment area, with ad e quate
sub mer gence, open the discharge valve fully. Start the unit using
manual controls. If fl ow is appreciably less than rated performance,
pump may be air locked. To expel trapped air, jog the unit several
times, using the manual controls.
• Have a qualifi ed electrician take voltage and current mea sure ments
with the pump running. Record these readings in the space provided
in the “Own er’s In for ma tion” section on page 1 of this manual for
future reference.
ADJUSTMENT PROCEDURE
Pumps: No adjustments are required.
Floats: Nonautomatic - Refer to the system drawing or to the panel
wiring sche mat ic for the desired lo ca tion of each fl oat switch
setting.
Automatic - Float is factory set to provide approximate on/off
levels as follows:
SERIES
ON
OFF
X160/X180 19½"
9¾"
X280
19¾"
10"
X290
19½"
9¾"
A tighter pumping range can be set by moving the fl oat stop
closer to the fl oat thereby lowering the "on" point.
Valves: Discharge valves should be placed in the fully open po si tion.
Sys tems should not be operated for extended periods of time
with the dis charge valves partially closed due to damaging
the valve.
SHUTDOWN PROCEDURES
If a system is shutdown for more than six months, the following is
rec om mend ed:
Pumps: If pit is to remain dry, then the pump can remain in the pit.
With the pump in the pit, it should be operated for fi ve minutes
once every three months. If the pit is to remain wet, the pump
should be removed and stored as noted above.
Panels: The panel should have all openings sealed to prevent mois ture
and dust from entering the enclosure. Prior to re start ing sys tem,
the panel should be inspected for presence of mois ture and any
loose con nec tions.
Valves: Consult the valve/actuator supplier for information con cern ing
these systems components.