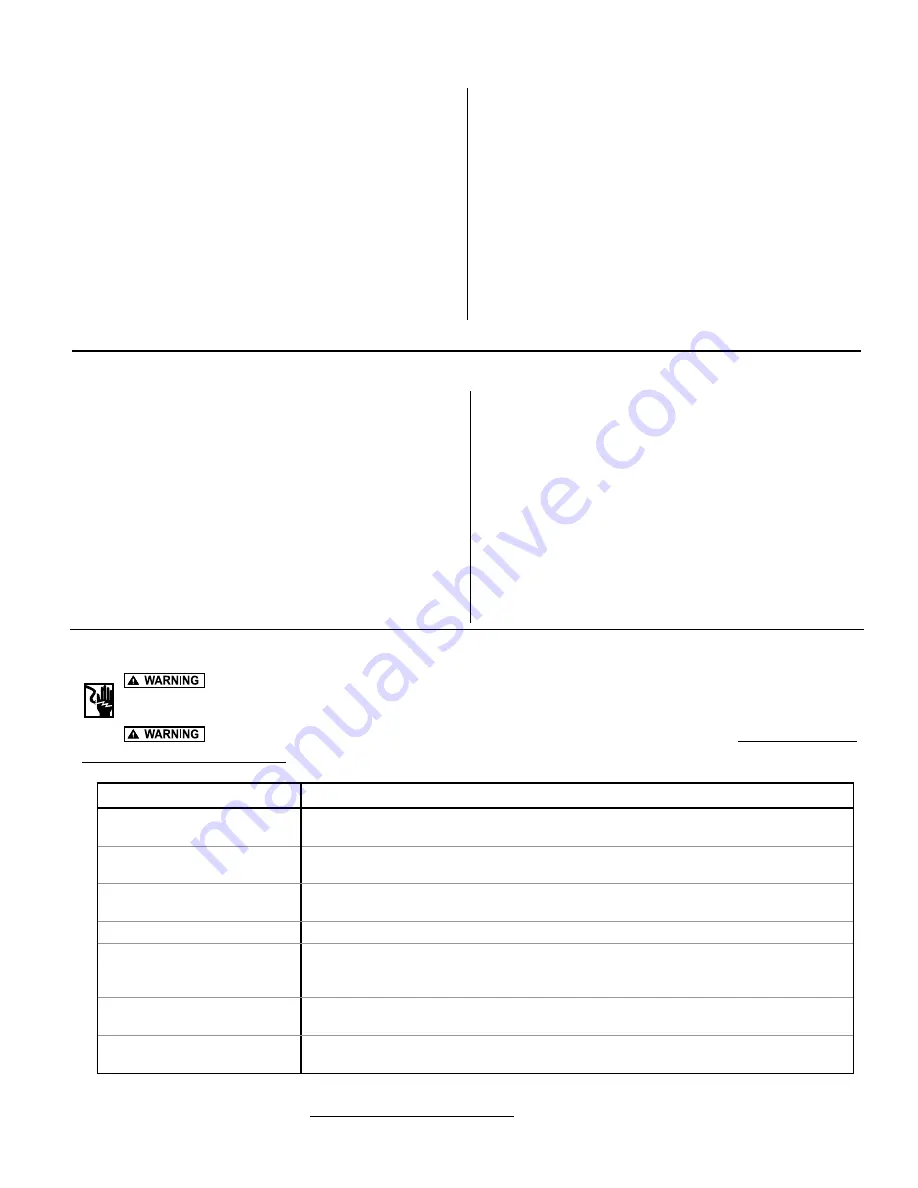
3
1. Electrical wiring and protection must be in accordance with National
Electrical Code and any other applicable state and local electrical
requirements.
2. All installations require a basin cover to prevent debris from falling into
the basin and to prevent accidental injury.
3. Securely tape or clamp power cord to discharge pipe, clear of the float
mechanism(s).
4. Use full-size discharge pipe.
5. Basin must be in accordance with applicable codes and specifications.
6. Pump must be level and float mechanism(s) clear of sides of basin
before starting pump. Float switch may be repositioned as needed.
7. Basin must be clean and free of debris after installation.
8. Gate valve or ball valve to be supplied by installer and installed
according to any and all codes.
9. Gas tight seals required to contain gases and odors.
10. Vent gases and odors to the atmosphere through vent pipe.
11. Install Zoeller Pump Stand (Model 10-2421) under pump to
provide a settling basin.
RECOMMENDED INSTALLATION FOR ALL APPLICATIONS
EASY DO'S & DON'TS FOR INSTALLING A SUMP PUMP
1. DO read thoroughly all installation material provided with the system.
2. DO inspect system for any visible damage caused by shipping. Contact
dealer if system appears to be damaged.
3. DO clean all debris from the sump. Be sure that the pump will have
a hard,
flat surface beneath it. DO NOT install on sand, gravel or dirt.
4. DO be sure that the sump is large enough to allow proper clearance
for the level control switch(es) to operate properly.
5. DO always disconnect pump from power source before handling.
DO always connect to a separately protected and properly grounded
circuit.
DO NOT ever cut, splice, or damage power cord (only splice in a
watertight junction box).
DO NOT carry or lift pump by its power cord.
DO NOT use an extension cord with a sump pump.
6. DO install a union in the discharge line.
DO NOT use a discharge pipe smaller than the pump discharge.
7. DO NOT use a sump pump as a trench or excavation pump, or for
pumping sewage, gasoline, or other hazardous liquids.
8. DO test system immediately after installation to be sure that the
system is working properly.
9. DO cover sump with an adequate sump cover.
10. DO review all applicable local and national codes and verify that the
installation conforms to each of them.
11. DO consult manufacturer for clarifications or questions.
12. DO inspect and test system for proper operations at least every three
months.
© Copyright 2019 Zoeller
®
Co. All rights reserved.
ELECTRICAL PRECAUTIONS-
Before servicing a pump, always shut off the main power breaker and then unplug the pump
- making sure you are wearing insulated protective sole shoes and not standing in water. Under flooded conditions, contact your local
electric company or a qualified licensed electrician for disconnecting electrical service prior to pump removal.
Submersible pumps contain oils which becomes pressurized and hot under operating condition
.
Allow 2-1/2 hours after
disconnecting before attempting service.
If the above checklist does not uncover the problem, consult the factory - do not attempt to service or otherwise disassemble pump. Service must be performed
by Zoeller Authorized Service Centers. Go to www.zoellerpumps.com/service stations to find the Authorized Service Centers in your area.
SERVICE CHECKLIST
CONDITION
COMMON CAUSES
A. Pump will not start or run.
Check fuse, low voltage, overload open, open or incorrect wiring, open switch, impeller or seal bound mechanically.
Motor or wiring shorted. Float assembly held down. Switch, damaged or out of adjustment.
B. Motor overheats and trips
overload or blows fuse.
Incorrect voltage, negative head (discharge open lower than normal) impeller or seal bound mechanically, motor
shorted.
C. Pump starts and stops too
often.
Float switch tether length too short, check valve stuck open, or none installed in long distance line, overload open,
bidding, sump pit too small.
D. Pump will not shut off.
Debris under float assembly, float bound by basin sides or other, switch damaged or out of adjustment.
E. Pump operates but delivers
little or no water.
Check inlet, strainer housing, discharge pipe, and vent holes for obstructions. Discharge head exceeds pump
capacity. Low or incorrect voltage. Incoming water containing air or causing air to enter pumping chamber.
Incorrect motor rotation. (DC pump only)
F. Drop in head and/or capacity
after a period of use.
Increased pipe friction, clogged line or check valve. Abrasive material and adverse chemicals could possibly
deteriorate impeller and pump housing. Check line. Remove base and inspect.
G.
If tank or fittings leak.
Carefully tighten pipe joints (use pipe dope) and screws. Check gasket location, tighten lid evenly. Do not over
tighten fittings or screws.