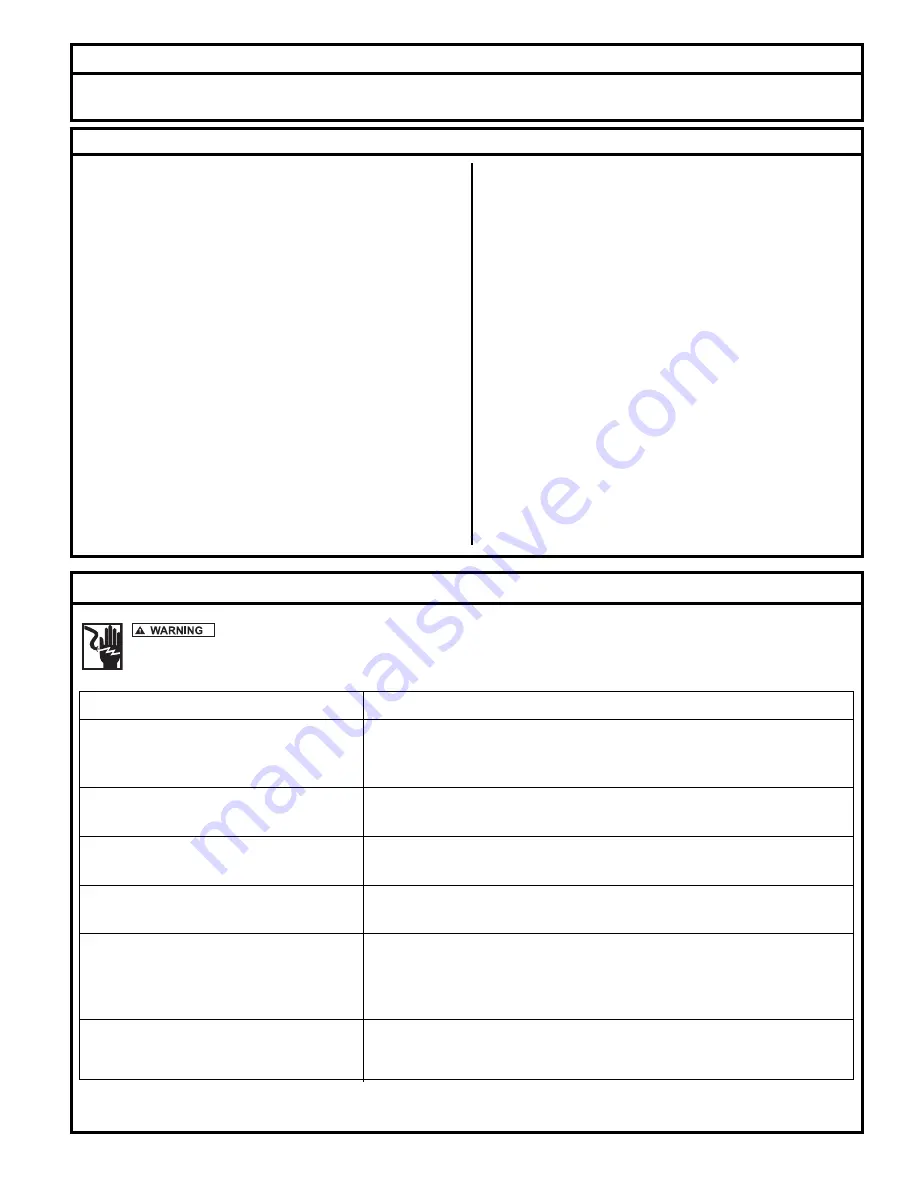
7
© Copyright 2007 Zoeller Co. All rights reserved.
Splicing Underground Wires
Splicing of wires to be buried must be done according to the National Electrical Code. Wire connectors or splicing means installed on conductors
for direct burial shall be listed for such use.
Start-up and Maintenance
Before placing the equipment into operation the following must be
checked:
•
Septic tank and/or pump chamber should be pumped and cleaned
prior to in stal la tion in existing system.
•
Septic tank and/or pump chamber must be watertight.
•
Installation needs to be according to instructions.
•
Installation should include an easy access riser and tamper resistant
lid.
•
Filter assembly needs to be in place and secure.
•
Float tree needs to be in place, secure and adjusted for proper
cycling.
• Make
sure
fl
oat switches are free to move within the basin.
•
Be sure electrical connections are watertight and conform
to the Uniform Building Code and the National Electrical
Code (NEC).
•
Fill the septic tank and/or pump chamber with water and check the
system for operation.
After installing the pump into the containment area with ad e quate
sub mer gence, open the discharge valve fully. Start the unit using manual
controls. If
fl
ow is appreciably less than rated per for mance, pump may
be air locked. To expel trapped air, jog the unit several times, using
the manual con trols.
Have a quali
fi
ed electrician take voltage and current mea sure ments
on the black wire of single phase. Record these read ings in the
space provided in the “Owner’s Information” section on the front this
manual for future ref er ence.
Be sure to complete all items such as installing the lid on the riser,
securely closing the control panel, and checking the sys tem op er a tion
have been com plet ed before placing the system into ser vice.
Routine maintenance should include:
• Service
fi
lter in STEP system and/or septic tank.
• Clean pump screen.
• Make sure the check valve is functioning properly.
• Check wire connections.
• Make sure the weep hole is clear.
• Make sure the
fl
oat switches are free to move within the basin.
• Make sure there are no leaks in the plumbing.
• Make sure there is no excessive noise while the pump is
running.
ELECTRICAL PRECAUTIONS-
Before servicing a pump, always shut off the main power breaker and then unplug
the pump - making sure you are not standing in water and wearing insulated protective sole shoes. Under
fl
ooded conditions, contact
your local electric company or a quali
fi
ed licensed electrician for disconnecting electrical service prior to pump removal.
If the above checklist does not uncover the problem, consult the factory - Do not attempt to service or otherwise disassemble pump.
Service must be by Zoeller Authorized Service Stations.
Troubleshooting and Service Checklist
COMMON CAUSES
Check fuse, low voltage, over load open, open or incorrect wiring, open switch, impeller or
seal bound mechanically, defective capacitor or relay when used, motor or wiring shorted.
Float assembly held down. Switch defective, dam aged, or out of adjustment.
Incorrect voltage, negative head (discharge open lower than normal), impeller or seal
bound mechanically, or relay, motor shorted.
Check valve stuck or none installed in long distance line, over load open, level switch(es)
defective, sump pit too small, leak in the system.
Debris under
fl
oat assembly bound by pit sides or other, switch de fec tive, damaged
or out of adjustment, leak in the system.
Check strainer housing, dis charge pipe, or if check valve is used vent hole must be
clear. Discharge head exceeds pump ca pac ity. Low or incorrect voltage. Incorrect
motor ro ta tion. Capacitor de fec tive. In com ing water con tain ing air or causing air to
enter pump ing chamber.
Increased pipe friction, clogged line or check valve. Abrasive material and ad verse
chem i cals could possibly deteriorate impeller and pump housing. Check line. Remove
unit and inspect.
CONDITION
A. Pump will not start or run.
B. Motor overheats and trips over load or
blows fuse.
C. Pump starts and stops too often.
D. Pump will not shut off.
E. Pump operates but delivers little or no
water.
F. Drop in head and/or capacity after a
period of use.