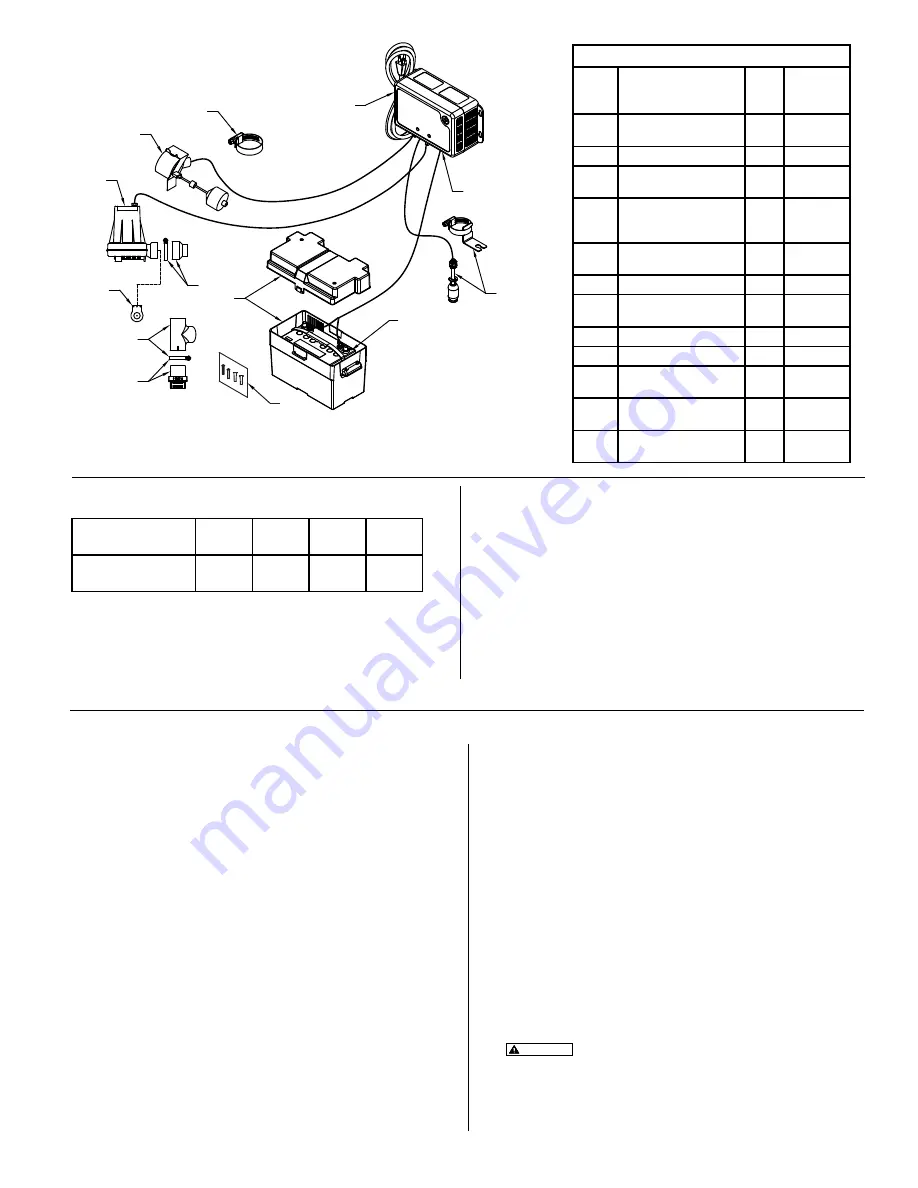
3
The DC controller is equipped with a charger for maintaining the battery in a
ready state and recharging the battery after use when AC power is restored.
Time for recharge depends upon the amount of power consumed by the pumping
cycle during the AC power interruption. The pump may go back to the ready run
position in a very short period of time. A completely drained battery may require
up to 24 hours for full recharge. If battery does not charge properly, the LED
battery will flash red.
PERFORMANCE
The DC pump performance at 12.7 Vdc
BATTERY SELECTION
Discharge
Feet of Head
5
(1.5 m)
10
(3 m)
15
(4.6 m)
28
(85 m)
Flow
GPM (LPM)12.7 volts
43
(163)
35
(132)
27
(102)
Shut-off
Head
SK3183
The DC emergency pump system requires a good quality, 12 volt battery
to obtain maximum pumping time during a power outage. A deep-cycle,
12 volt, 105 amp-hour marine battery or larger is recommended and will
provide approximately 5 hours of continuous pumping time in a sump pump
installation with 8' (2.4 m) of head pressure. In most installations, the pump
runs intermittently and the battery life is extended accordingly. Batteries with
top terminals are recommended for ease of installation. "Wet" cell batteries
contain acid, and proper precaution must be taken when handling. Battery
box will accommodate a maximum battery size of 13-1/2" (34.3 cm) Length x 7"
(17.8 cm) Width x 9-1/2" (49.5 cm) Height. AGM batteries also recommended.
Do not use gel batteries or automotive batteries.
© Copyright 2019 Zoeller
®
Co. All rights reserved.
2
3
1
4
5
12
10
11
9
6
7
8
12 VOLT BATTERY
SUPPLIED BY USER
Model 508 Spin
™
Item
Description
Qty
508-C
02/19
thru Current
1
Pump 12 V DC / Backup
(service part)
1
155652
2
Flapper asm, (service part)
1
152970
3
Fitting, asm & clamp "508"
(service part)
1
152969
4
Fitting, PVC 1-1/2" (DN40)
tee/SCH 40 (pressure
fitting)
1
153766
5
Valve, check / 1.5" (DN40)
Inline / vertical
1
153772
6
Operational float
1
155654
7
Clamp, #28 Worm-SS (float
switch)
2
004287
8
Spin
™
controller
1
155978
9
Fuse, 30 amp automotive
1
016918
10
Optional high water float,
NC
1
10-4830
11
Battery box asm (box and
cover)
1
10-0764
12
Hardware pak, charger /
switch mode
2
152864
NOTE: Check float operations to ensure the hose clamp screws will not
interfere with the float operation of the primary pump.
8. Assemble the operation float assembly per Figure 3. Install float switches
as seen in Figure 1.
9. Install the operational float switch bracket above the "on" level of the
primary pump using the clamp provided. Make certain the clamp is tight
on the pipe to avoid slippage. Ensure that the "off" level of the float is 1"
(2.5 cm) minimum above the outlet of the DC backup pump. Position the
pumps in the sump and move float up and down, ensuring free movement
without interference from any obstructions inside the sump or lid. The
float switch can be moved on the discharge pipe, or the rubber stops can
be adjusted as necessary. Cut extra float rod length below lower float
stop to prevent debris from interfering with float operation.
10. Install the Spin
™
Controller (see Figure 3) by using the anchors provided.
For best cooling, install wall mount configuration. The controller should
be located at least 3' (1 m) above the sump.
11. Connect the leads from the controller to the battery terminals. Positive
(+) lead to positive terminal and black neg. (-) lead to negative battery
terminal.
CAUTION
Correct battery hook-up is essential for operation of
the system. Use wing nuts supplied with battery and eyelet connectors
on battery wire leads. The positive terminal is the larger stud, 3/8" (10
mm) diameter. The smaller stud, 5/16" (8 mm) diameter is the negative
terminal. Apply grease to the terminals to help prevent corrosion.
1. The preferred method of installation for backup pumps is shown in Figure 1.
The installation kit includes the necessary fittings and parts needed to install
as in Figure 1. A check valve is incorporated in the discharge of the backup
pump.
NOTE: Do not install in small spaces where the controller will not be
properly cooled.
2. Remove all parts from the shipping carton, and make sure all parts are
included. Refer to the parts list on page 3.
3. Select a location for the battery and the controller. The controller must be
within 8' (2.4 m) of a 115 V wall outlet and within 6' (1.8 m) of pump and basin.
Is recommented that the controller is plugged into a separate circuit from the
primary pump.
4. If the primary pump is installed, disconnect power.
NOTE: Discharge piping must be 1-1/2" SCH 40 PVC
5. Remove the discharge pipe from the pump and place it aside.
6. Solvent weld the DC Pump discharge reducer fitting to the tee as shown in
Figure 1. Ensure the O-ring is properly located on the pump discharge. Slide
the DC pump into the fitting, and tighten the hose clamp.
NOTE: The pump must be pushed all the way into the fitting to prevent the
fitting from leaking.
7. Determine the position of the DC pump and measure for discharge piping.
Use that measurement to cut the discharge pipe. Solvent weld that piece
to the tee. Measure, cut and solvent weld any remaining discharge piping
above the tee.
INSTALLATION