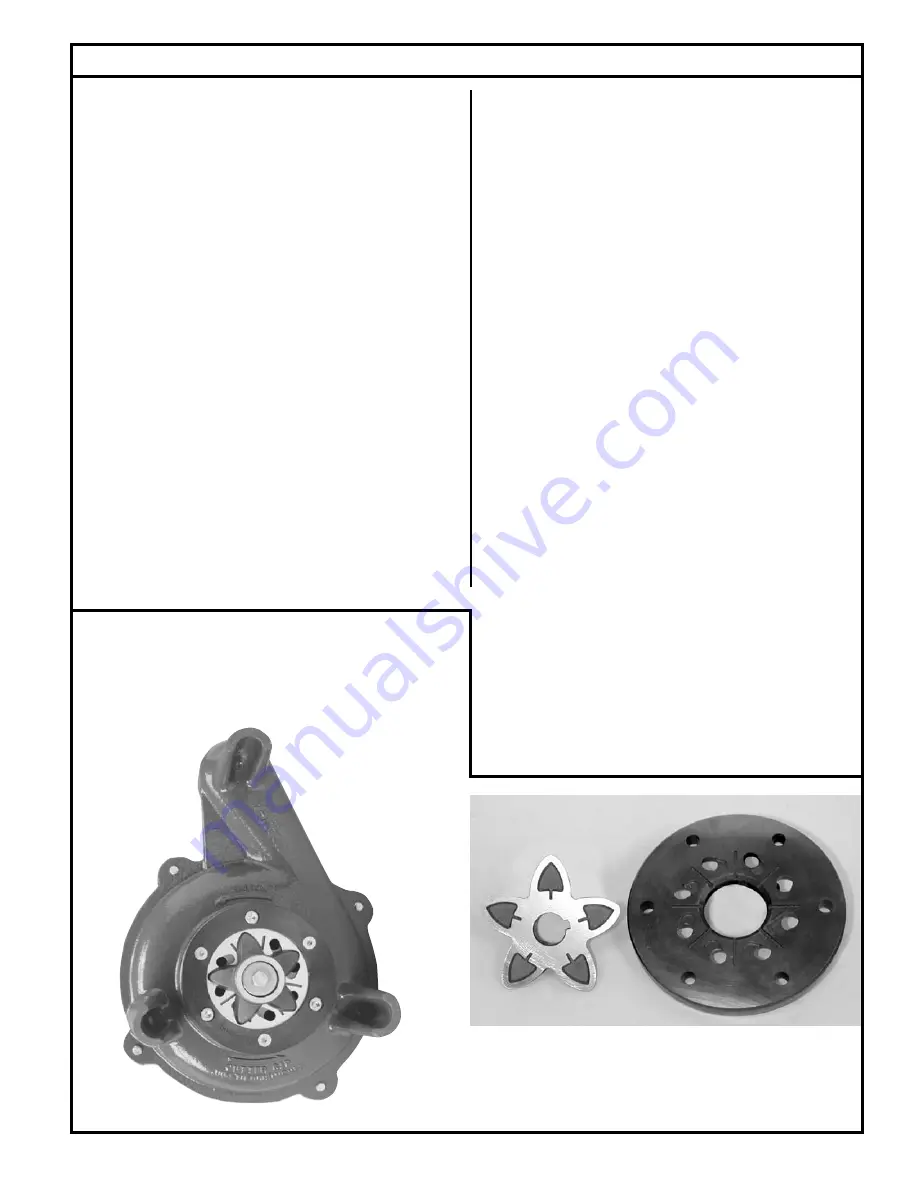
11
© Copyright 2008 Zoeller Co. All rights reserved.
Cutter Maintenance
To remove star cutter: Remove guard ring then heat the
cen ter bolt to 350°F to loos en Loctite® thread seal ant.
Grind the Star Cutter and Disc seen here to a 32 micro
fi
nish.
Sur fac es must be
fl
at to within 0.001” T.I.R. Gap must be be tween
0.004” and 0.008” on these parts.
1.
All power circuits must be dis con nect ed and locked
out before any attempts are made at servicing.
The star
cutter and disc can be removed and sharp ened by grinding
the cut ting faces. Both star cutter and disc must be re moved
from the pump. Removal of these parts can be ac com plished
in the
fi
eld by removing pump from the sump and po si tion ing
hor i zon tal ly to access the intake of the pump. If seals or other
repairs are required, the pump must be totally removed and
serviced in a shop by a quali
fi
ed pump technician or au tho rized
service center.
2. Remove the three countersunk screws on the plastic guard
ring and remove the ring.
3. Thoroughly clean the star cutter and disc assembly. Tilt pump
back to the vertical po si tion to make certain the end play has
been removed. Check and record the clearance be tween the
star cutter and disc with a feeler gage. The correct running
clear ance is between 0.004" and 0.008".
4. With pump in horizontal position, heat the hex head bolt in
the center of the star cutter with a propane torch. The bolt
must be heated to 350°F to soften the thread lock sealer on
the bolt for ease of removal. Remove the bolt by turning in a
coun ter clock wise rotation. It will be necessary to use a wood
block to prevent the star cutter from turning while re mov ing
the bolt. Pull star cutter from the shaft and remove the spacer
shims located behind the star cutter.
5. Remove the three cap screws holding the disc and remove
disc from the pump.
6. The disc and star cutter can be replaced with new service
parts or resurfaced by grinding. Re sur fac ing is ac com plished
by surface grinding both disc and star cutter to a 32 micro
fi
nish. Do not attempt grinding in the
fi
eld. Send parts to a
quali
fi
ed machine shop or return to the factory for repair. The
disc, star cutter and shims are a matched set. Keep parts
together. Measure disc before and after re sur fac ing with
micrometer and record measurements.
7. After resurfacing, the disc and star cutter must be
fl
at within
0.001". If the disc has been surface ground, it will be neces-
sary to remove shims to com pen sate for the ma te ri al removed
from the disc. As a starting point, remove shims of the same
thickness as the amount machined from the cutter disc (step
6 above). Final running clearance must be between 0.004”
and 0.008”. Be sure pump is in vertical position and all end
play has been removed before mea sur ing.
8. Clean bottom of pump where disc is located and replace
disc and retainer screws. Torque to 63-67 in-lbs. Replace
star cutter with the correct shims. Install washer and torque
hex head bolt to 71-75 in.-lbs. Apply Loctite 262 thread-lock
sealant or equal to bolt threads prior to insertion. Check
running clearance with pump in vertical po si tion to re move
end play. Clear ance must be between 0.004" and 0.008" to
obtain ef
fi
cient grinding when pump is put back in service.
9. Replace plastic guard ring and its three screws.
10. Check the oil in the motor housing before reinstalling. Con tact
the factory if the oil has a milky appearance or burnt smell.
The level should be even with the
fi
ll plug when pump is in
the upright position. Add oil if re quired. Use insulating oil
sup plied by the factory.
FIGURE 6.