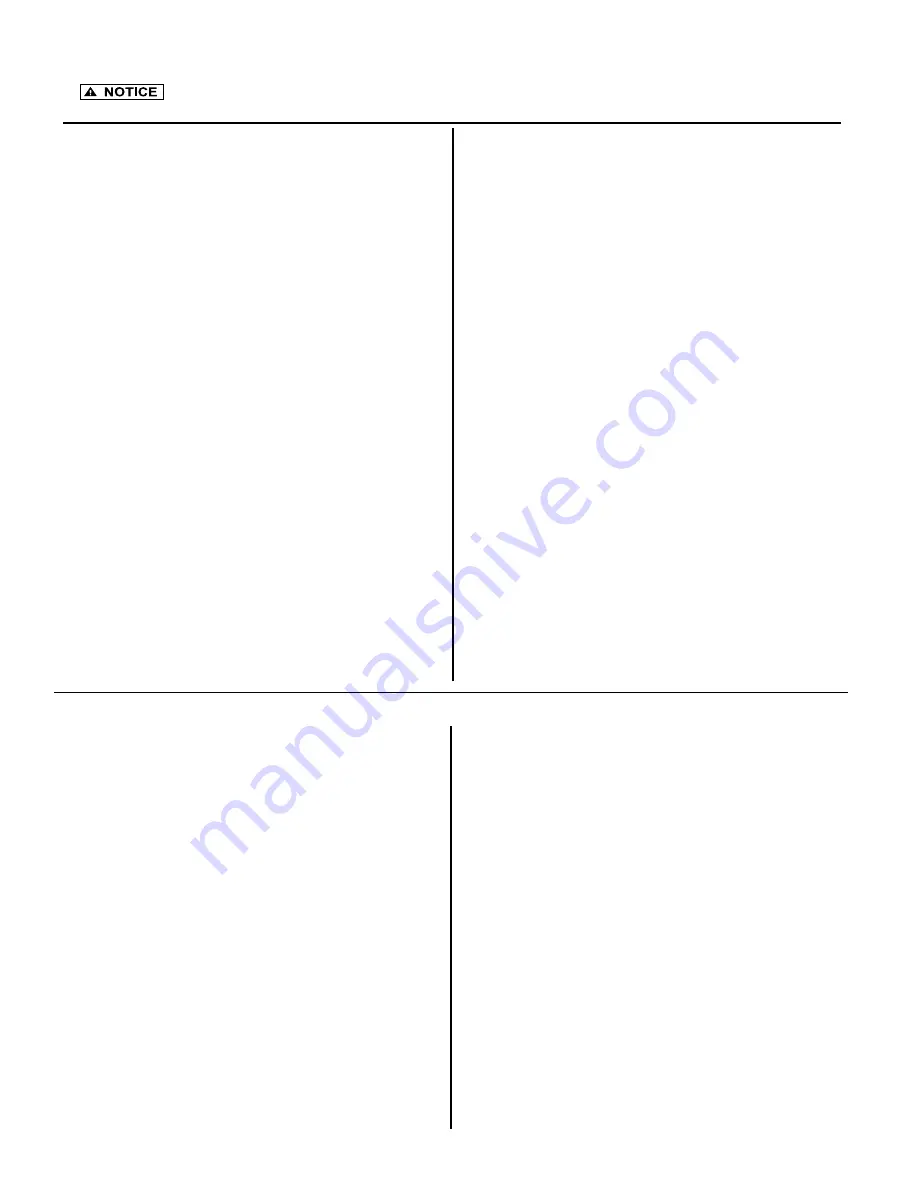
6
© Copyright 2020 Zoeller
®
Co. All rights reserved.
1. Review the drawing in Fig. 4 on page 5 and the actual system to
become familiar with the components in the packaged grinder pump
system. Review where the unit will be installed. Determine where
the power feed, inlet pipe, and discharge pipe will be located.
2. Remove the unit from packing. Prepackaged outdoor systems are
preassembled at the Zoeller Company and require a minimum of
field assembly work. Float switches are set and tethered for proper
operation from the Factory. The alarm switch should be located 2”
above the pump “on” level.
3. Float switches are tied in place for shipping purposes on all model
prepackaged systems. Cut the cable tie around each float switch
bulb or the unit will not operate properly. Verify that where the float
switches are set will work for your application.
Verifying that the
float switches are set properly and will not hang up inside the basin is
the responsibility of the installing contractor.
4. Dig a hole for the basin. The hole should be at least 24” larger in
diameter than the basin diameter to provide 12” of backfill all around
and deep enough to provide either 12” of compacted backfill or 6”
when a concrete pad is required. Ensure the removable cover extends
above the finished grade line and the grade slopes away from the unit.
Backfill and subbase should be 1/8” –3/4” pea gravel or 1/8” –1/2”
crushed stone. (Reference basin installation instructions included
with unit)
5.
Note: Care must be taken when excavating in order to avoid underground
utilities and disturbance of existing structure foundations. The hole should
be located at least ten feet from adjacent structures. Additional distance
may be required to sufficiently locate the basin outside of the loading area
of the adjacent structures.
6. The location of the inlet fitting is determined by the depth of the inlet
pipe. The inlet fitting must be used with 4” pipe. It is best to install the
inlet on the side of the basin opposite the float switches. To install, use
a 5” hole saw to drill into the side of the basin at the correct elevation.
Center the hub inner diameter with the hole in the basin. Attach the
hub to the side of the basin using the sealant and hardware provided.
7. The bottom of the excavation can now be back filled and compacted.
Set basin in hole and connect the 4” inlet pipe to the inlet hub.
8. The discharge piping is connected to the 1-1/4” threaded fitting
located in the basin sidewall.
9. Connect pull rod to Pump assembly. Connect lift cable to top of pump.
Lower the pump into basin ensuring the discharge pipe bracket slides
into the disconnect fitting.
10. Pouring a concrete anchor around system can now be completed.
Basin should be filled with water when pouring concrete to minimize
movement of the system. Back fill around basin with specified
media. Care should be used to avoid damaging components
or leaving voids when back filling. Refer to Basin installation
reference guide on more specific requirements.
11.
Note: The progressing cavity grinder basin is a sewage holding tank.
Vent connection should be installed in accordance with all national,
state and local plumbing codes.
12. Dig a trench for the electrical conduit. Trench should be located
at least 18” deep and follow all applicable NEC codes. Connect
electrical wiring to Junction box according to wiring instructions
included in this manual and wiring diagram in box. Use the potting
kit provided with the junction box. Use the included sealant when
closing junction box.
13. If used, a control panel is installed within sight of the system.
Connect float switches and pump cords according to the “Pump
Wiring Instructions” found in this manual and located inside the
panel enclosure.
14. Remove any debris from the basin. Using clean water, check the
system for proper operation.
15. Seal and secure the lid using the proper bolts and sealant when
using a lid without a formed gasket.
16. Add water to the basin and test the system for leaks and proper
pump operation.
17. Record system start up data for future reference.
OUTDOOR PREPACKAGED SYSTEM INSTALLATION INSTRUCTIONS
This set of instructions is for factory prepackaged outdoor progressing cavity grinder systems only. If this is a field assembled outdoor
system you can use these instructions as a guideline.
GENERAL
Zoeller pumps are lubricated and tested at the factory prior to shipment
and require minimum pre-start-up maintenance.
Maximum operating temperature of pump liquid for grinder pumps must
not exceed 130 °F (54 °C).
These units are not designed to handle liquids other than sanitary sewage.
If pump is used to dewater areas with contaminated liquids with heavy
or abrasive materials, the warranty will be voided.
NAMEPLATE DATA
The nameplate, located on the top of the pump, indicates specific
information about the construction of the pump. The model number
and date code information should be recorded on the front page in the
“Owner’s Information” section of this manual.
SHORT TERM STORAGE
When not in use, the pump should be stored and the following is advised:
• Drain pump housing by laying pump horizontal with discharge down.
Then stand pump on legs.
• Store pump inside whenever possible or cover with some type of protective
covering.
• Tape or seal in plastic bag the terminal ends of wire leads.
• Spray coat unpainted surfaces with rust inhibiting oil.
If panel is to be stored, the following is advised:
• Store the panel inside whenever possible and leave in the shipping
box.
• All openings shall be sealed.
• Store in an upright position.
• Do not stack anything on top of panel.
START-UP PROCEDURE
Before placing the equipment into operation the following should be
checked:
• Clean pit.
• Electrical boxes dry and securely installed.
• Floats positioned properly.
• Discharge valves open.
• Adequate water level in basin for pump submersion.
Once the above has been verified proceed with the following checks:
• Pump power cables and control floats properly installed and voltage
verified.
• Conduit connections to panel are properly sealed.
OPERATION