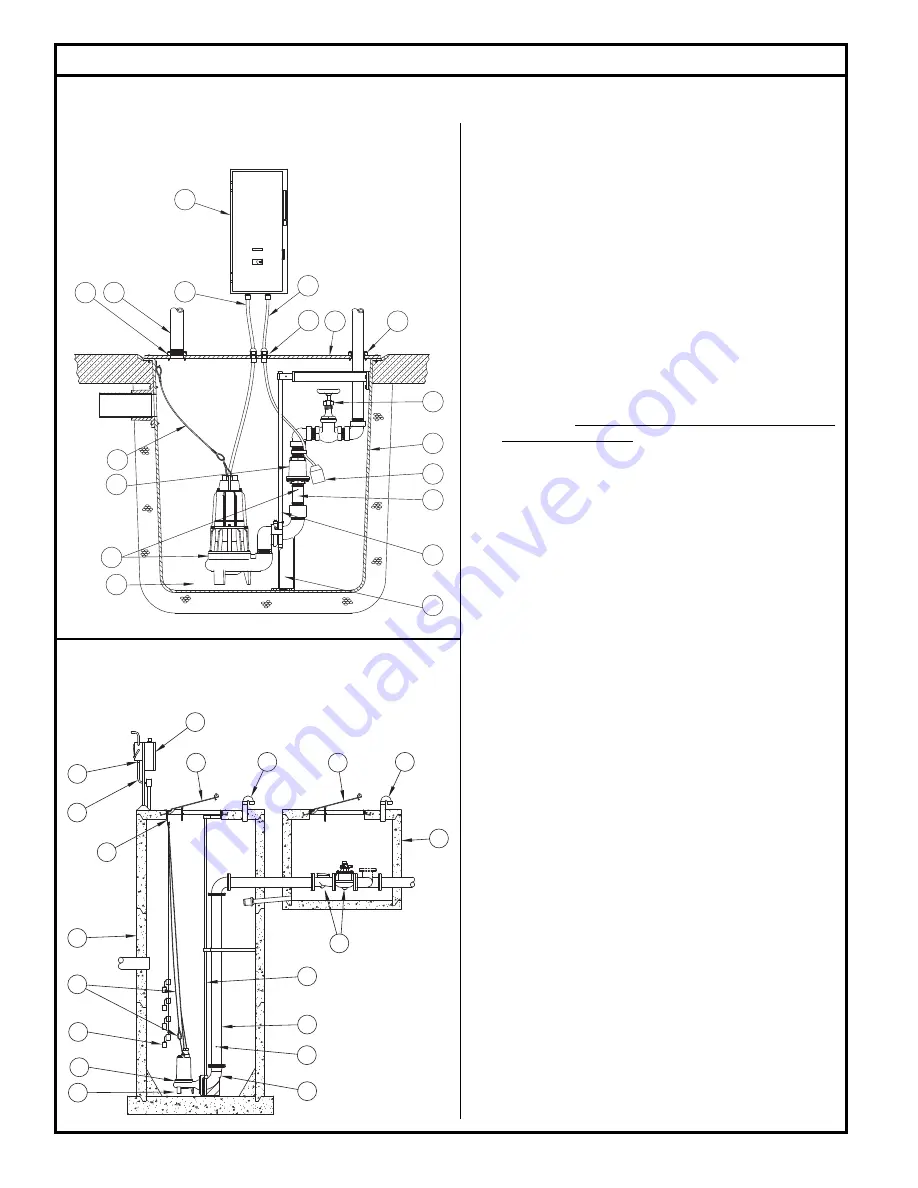
4
© Copyright 2010 Zoeller Co. All rights reserved.
All installations must comply with all applicable electrical and plumbing codes, including, but not limited to, National Electrical Code,
local, regional, and/or state plumbing codes, etc.
TYPICAL OUTDOOR CONCRETE BASIN WITH VALVE
BOX AND HINGED ACCESS COVERS
TYPICAL INDOOR FIBERGLASS BASIN
Typical Sewage/Waste Pumping System Installation
(1) Electrical wiring and protection must be in accordance with the
National Electrical Code, and any other applicable state and
local electrical requirements.
(2) Install proper full fl ow check and shut-off valve.
(3) Install proper controls. (Outdoor panels require NEMA 3R or
4X enclosure)
(4)
All
installations
require a basin cover to prevent debris from
falling into the basin and to prevent accidental injury.
(5) Gas tight seals are required in all indoor sewage installations
to contain gases and odors.
(6)
When check valve is installed, drill a 3/16” diameter hole in
the discharge pipe below the check valve even with the top
of the pump. NOTE: The hole must be below the basin cover
and cleaned periodically. Water stream will be visible from this
hole during pump run periods. Also a vent hole is drilled in the
pump housing. Be sure that this hole is cleared during any
servicing.
(7) Vent gases and odors to the atmosphere through vent pipe per
Local and State codes.
(8) Secure power cord to avoid entanglement with variable level
fl oat switch mechanism.
(9)
Do not reduce pump discharge pipe below 3” IPS size.
(10) Basin must be in accordance with all applicable codes
and
specifi cations. Basin must be sized to allow a minimum 3
minute lapse time between starts.
(11) Pump must be level and the tethered variable level fl oat switch
must be free and not hang up on pump or pit peculiarities.
(12) If a rail system is used, discharge elbow must be fi rmly anchored
to the bottom of basin. In fi berglass basin, the bottom will need
to be reinforced if the discharge elbow is used.
(13) If a rail system is used, the guide rails are ¾” schedule 40 pipe
for threaded vertical discharge units and 2” schedule 40 pipe
for fl anged horizontal discharge units. Brass, stainless steel or
galvanized steel is recommended.
(14) Install ring and cable for lifting pump from pit.
(15) Basin must be clean and free of debris after installation.
(16) Cords must be properly sealed to prevent moisture and gases
from entering the control panel.
3
8
7
5
16
1
14
6
13
12
11
10
2
2
9
5
4
15
ZEPA0466
ZEPA0071
7
4
4
7
3
16
1
10
6
12
9
6
13
2
10
14
15
8
11