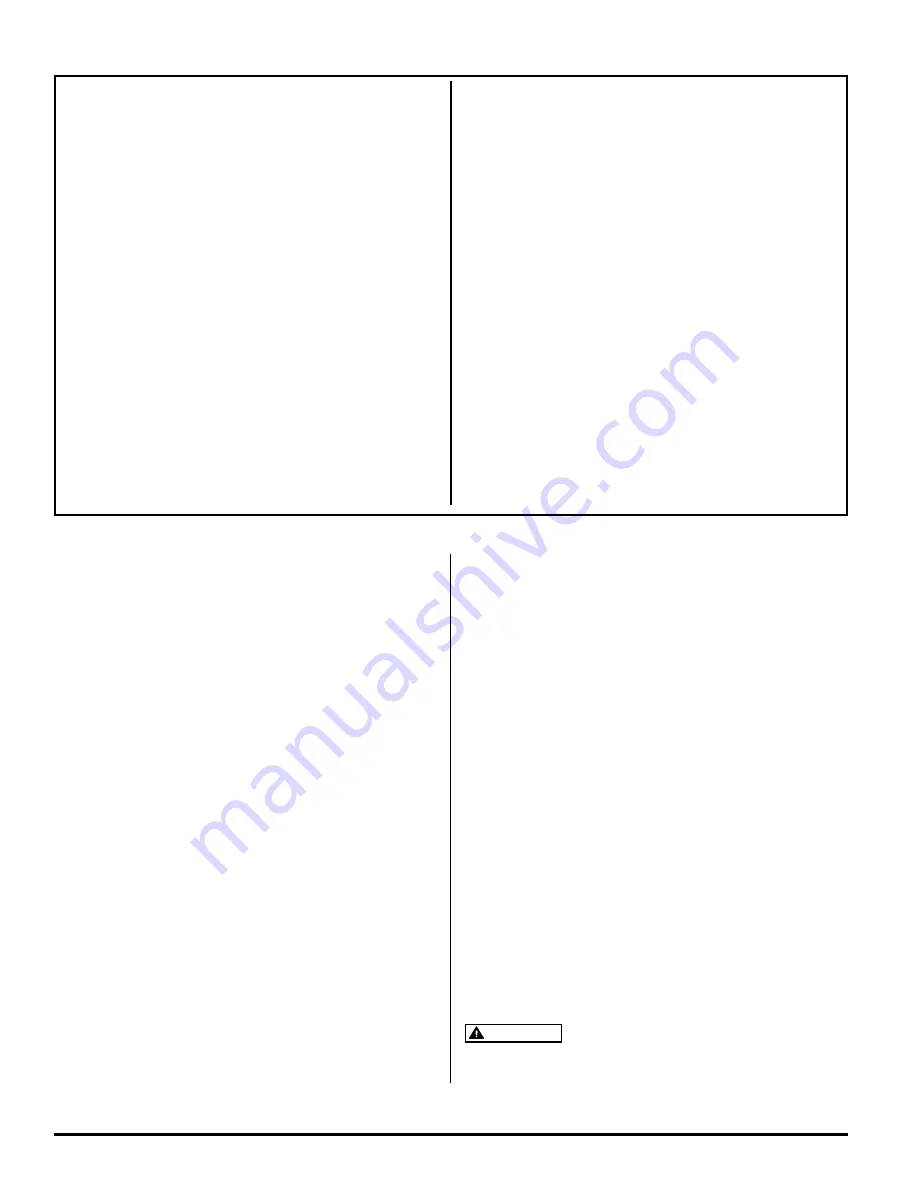
© Copyright 2014 Zoeller
®
Co. All rights reserved.
2
LOCATION
1. Pump can be located at the well or can be offset some distance
away from the well. For best performance it should be located as
close to the well as possible.
2. Location can be in the basement, a watertight pit below ground, or
in a pump house above ground.
3. Ventilation and drainage must be provided to prevent damage from
moisture to the motor and pressure switch.
4. The pump and all piping must be protected from freezing.
5. Pump and pipe line must be drained when not in use if there is any
danger of freezing.
WELL CONDITIONS
1. Wells should be pumped clean of all sand and foreign matter
before installing the pump or damage may result to the operating
parts.
2. The well must be able of supplying enough water to satisfy the
capacity of the pump and water needs. The water level must not
draw down below the maximum rated suction lift of the pump or
loss of capacity and prime will result.
SUCTION LIMITATIONS
1. Shallow well installation is satisfactory where the suction lift is less
than 25 feet. Suction lift is the vertical lift plus losses due to friction
2. Suction lift varies depending upon elevation (altitude) and water
temperature.
PIPING
1. Plastic or galvanized steel pipe may be used in the installation.
Plastic pipe must have a minimum pressure rating 160 P.S.I. Gal-
vanized steel pipe must be in good condition free of rust and scale.
Threads should be sharp and cleanly cut.
2. Both the suction and discharge pipe should be no smaller than the
corresponding tappings of the pump (See Figure 1). If long runs
are encountered larger pipe should be used. Smaller pipe will
reduce the capacity of the pump.
3. All joints and connections should have pipe sealing compound
(male threads only) applied and drawn up tightly.
The entire system must be air and water tight for efficient operation.
PUMP INSTALLATION
1. Refer to Figures 3, 4, 5, and 6 for typical installations. If galva-
nized pipe is used, both the suction and discharge pipe should be
supported at a point near the pump to avoid strains being placed
on the pump.
2. The suction pipe should slope upwards from the water source
to the pump. Locate the pump as close to the water as possible
keeping the suction pipe as short as conditions permit.
3 Avoid dips or pockets in offset piping or air will accumulate at high
points which will make priming difficult.
4. A foot valve located in the water or a check valve located as close
to the water as possible will reduce priming time of the pump and
help maintain prime. A strainer must be used on the suction line to
filter out dirt and debris.
5. Install a gate valve and union in the discharge line. For removal
of the pump for service, close the gate valve and disconnect the
union.
CAUTION
Do not use a globe valve or other restricting type of
valve at the discharge. This will seriously restrict the capacity of the pump.
LIMITED WARRANTY
Zoeller Pump Company warrants, to the purchaser and subsequent
owner during the warranty period, every new Zoeller Pump Company
product to be free from defects in material and workmanship under
normal use and service, when properly installed, used and maintained,
for 1) Standard Warranty - a period of one year from date of installation
or 18 months from date of manufacturer, whichever comes first OR 2)
Optional Three (3) Year Warranty - a period of three (3) years from date
of installation or 42 months from date of manufacturer whichever comes
first. Parts that fail, (within standard or three (3) year optional warranty)
that inspections determine to be defective in material or workmanship,
will be repaired, replaced or remanufactured at Zoeller Pump Company’s
option, provided however, that by so doing we will not be obligated to
replace an entire assembly, the entire mechanism or the complete unit.
No allowance will be made for shipping charges, damages, labor or other
charges that may occur due to product failure, repair or replacement.
This warranty does not apply to any material that has been disassembled
without prior approval of Zoeller Pump Company, subjected to misuse,
misapplication, neglect, alteration, accident or act of nature; that has
not been installed, operated or maintained in accordance with Zoeller
Pump Company installation instructions; that has been exposed to but
not limited to the following: sand, gravel, cement, mud, tar, hydrocarbons
or hydrocarbon derivatives (oil, gasoline, solvents, etc), wash towels or
feminine sanitary products, etc. or other abrasive or corrosive substances.
This warranty is in lieu of all other warranties expressed or implied; and
we do not authorize any representative or other person to assume for
us any other liability in connection with our products.
Contact Zoeller Pump Company, 3649 Cane Run Road, Louisville,
Kentucky 40211-1961, Attention: Customer Support Department to obtain
any needed repair or replacement of part(s) or additional information
pertaining to our warranty.
ZOELLER PUMP COMPANY EXPRESSLY DISCLAIMS LIABILITY
FOR SPECIAL, CONSEQUENTIAL OR INCIDENTAL DAMAGES OR
BREACH OF EXPRESSED OR IMPLIED WARRANTY; AND ANY
IMPLIED WARRANTY OF FITNESS FOR A PARTICULAR PURPOSE
AND OF MERCHANTABILITY SHALL BE LIMITED TO THE DURATION
OF THE EXPRESSED WARRANTY.
Some states do not allow limitations on the duration of an implied warranty,
so the above limitation may not apply to you. Some states do not allow
the exclusion or limitation of incidental or consequential damages, so
the above limitation or exclusion may not apply to you.
This warranty gives you specific legal rights and you may also have
other rights which vary from state to state.