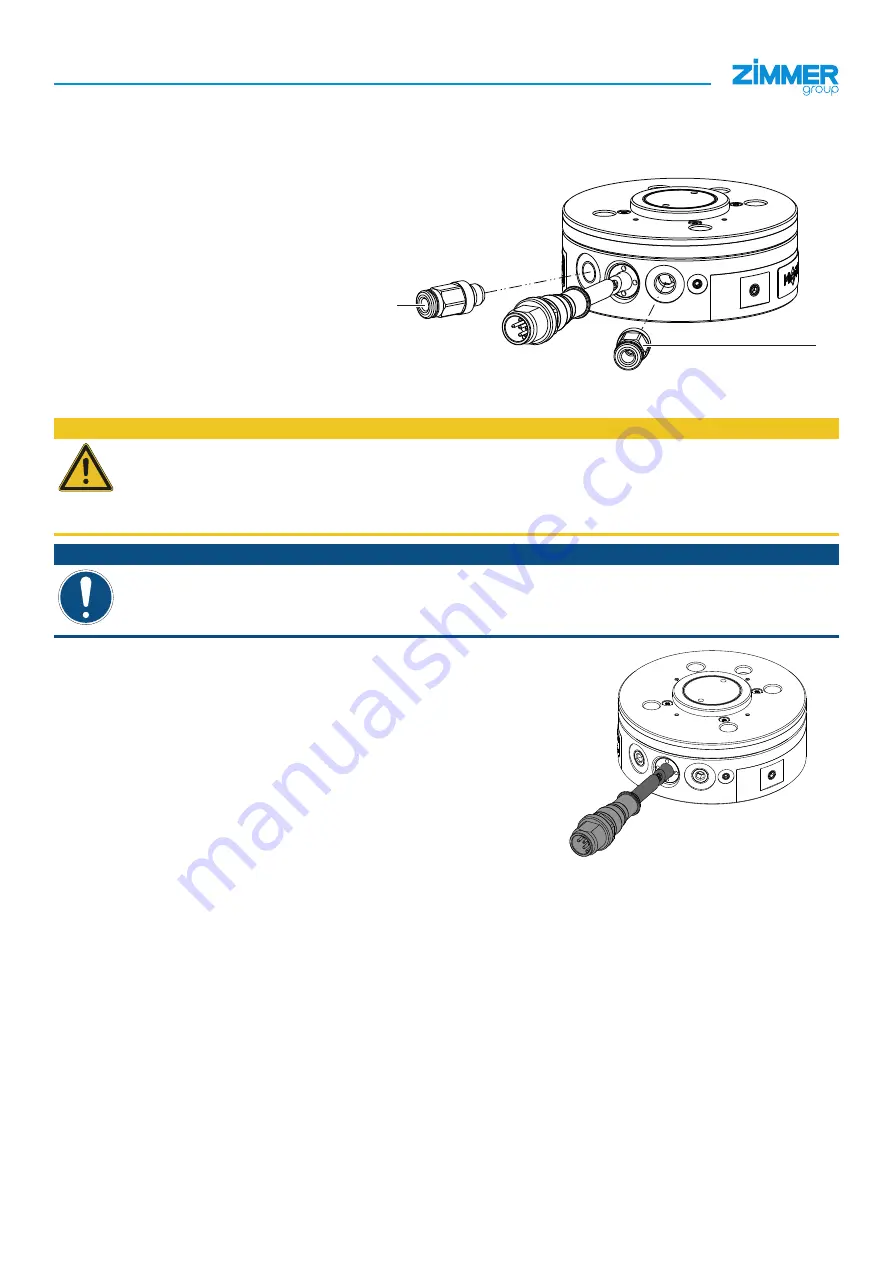
19
10.2 Installing the energy supply
10.2.1 Installing the pneumatic system
►
Unscrew the grub screws.
bt
bu
►
Insert the screw fittings into the provided
connections.
bt
Close gripper
bu
Open gripper
10.2.2 Installing the wiring
CAUTION
Risk of injury from getting caught in the connecting cable
While the robot is moving, hair or limbs can be caught in the connecting cable.
►
Route the connecting cable as close as possible to the robot arm.
►
Avoid the danger zone.
NOTICE
The cables that are used by Zimmer GmbH feature a minimum bending radius of 10 x the outer diameter.
This bending radius must not be undershot!
►
Freely suspended cables must be secured to prevent excessive motion loads or pinching.
►
Connect the product with the robot or route the connecting cable
along the robot to the IO-Link master.
INSTALLATION AND OPERATION INSTRUCTIONS:
LWR50F
DDOC01074 / f
EN / 2023-06-05
Zimmer GmbH • Im Salmenkopf 5 •
77866 Rheinau, Germany •
+49 7844 9138 0 • www.zimmer-group.com
Содержание MATCH LWR50F
Страница 2: ......