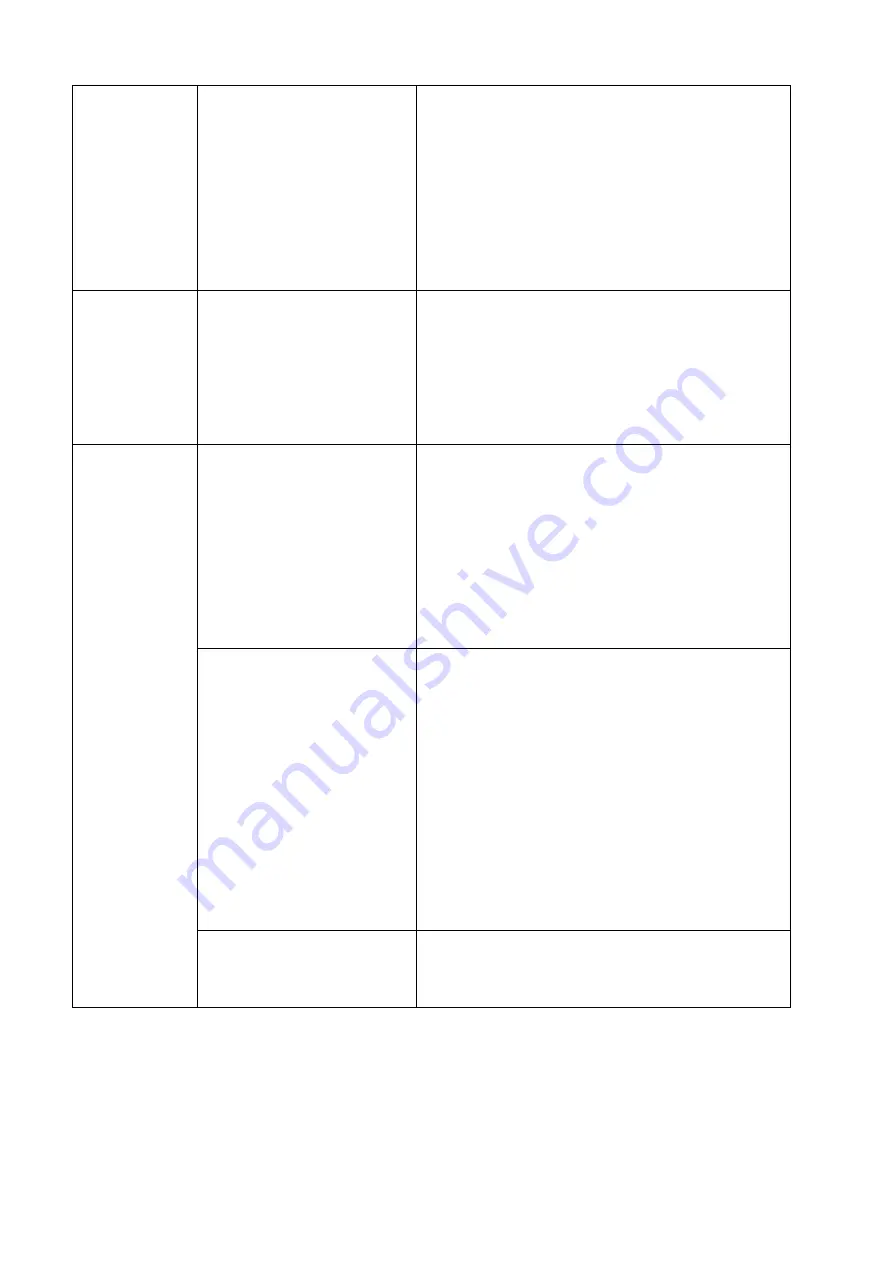
25
valve;
4. The fit clearance between the
worm gear and the worm is too
large;
5. A sound is heard when the
pipeline safety valve is opened.
4. It is unnecessary to replace parts if no damage occurs;
5. Check and clean the safety valve, and adjust its opening
pressure.
The flow
regulation
mechanism does
not work
1. The threads of adjusting screw
and adjusting nut are galled;
2. The driving mechanism is
internally jammed.
1. Remove the parts for repair or replacement;
2. Disassemble and check, and observe the movement of
connecting rod, eccentric gear, crosshead, and crosshead
sleeve in the bracket.
Diaphragm
ruptures
1. Cracks exists at the edge
1. The diaphragm has reached the fatigue limit and naturally
ruptures, and needs to be replaced
2. If the radius of arc angle of the pressure-tight seal of the
cylinder head (pump head) diaphragm is not large enough or
the seal not smooth enough, it is necessary to increase the arc
angle radius and then polish the seal with sand papers.
2. The diaphragm ruptures at the
outlet hole of the corresponding
pump head
It is mainly caused by excessive oil make-up.
1. Check the fit clearance between the limit valve spool and
the limit valve sleeve, and control it within 0.03~0.07mm.
2. Check whether the two O-rings of the limit valve sleeve
are intact, and replace them in case of rupture.
3. If the diaphragm still ruptures after inspection and repair,
appropriately adjust and increase the spring force of the
make-up valve rod.
3. Other ruptures
The diaphragm is possibly scratched by sharp materials (such
as welding slag and iron scrap) in the liquid