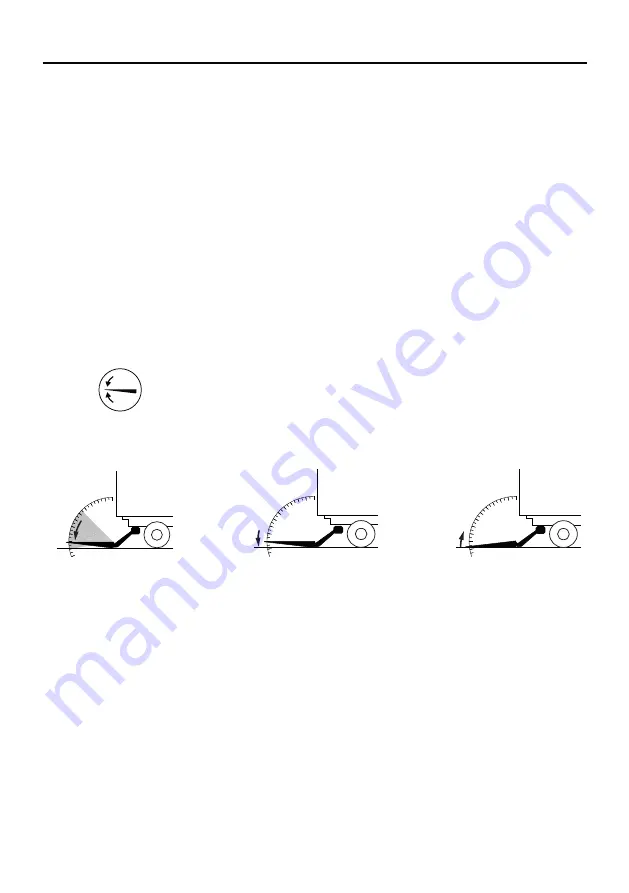
26
Design and Function
3.11 Electric autotilt
The optional electric autotilt feature simplifies tail lift operation.
Autotilt-down is enabled automatically when the Down function is used and when the plat-
form rests on the ground, provided that the platform angle is less than 45°. This function
automatically tilts the tip of the platform down towards the ground.
In autotilt down, the tilt function is driven solely by gravity. For fastest operation, the plat-
form should first be tilted manually to the horizontal position before enabling autotilt.
Autotilt-up is enabled when using the Up function with the platform in the ground position.
When this function is enabled, the platform is automatically tilted up to the set angle (hori
-
zontal position) before moving upwards.
Zone where autotilt
is available
Lowering to ground
Raising from ground
45º
±10º
A
Autotilt symbol