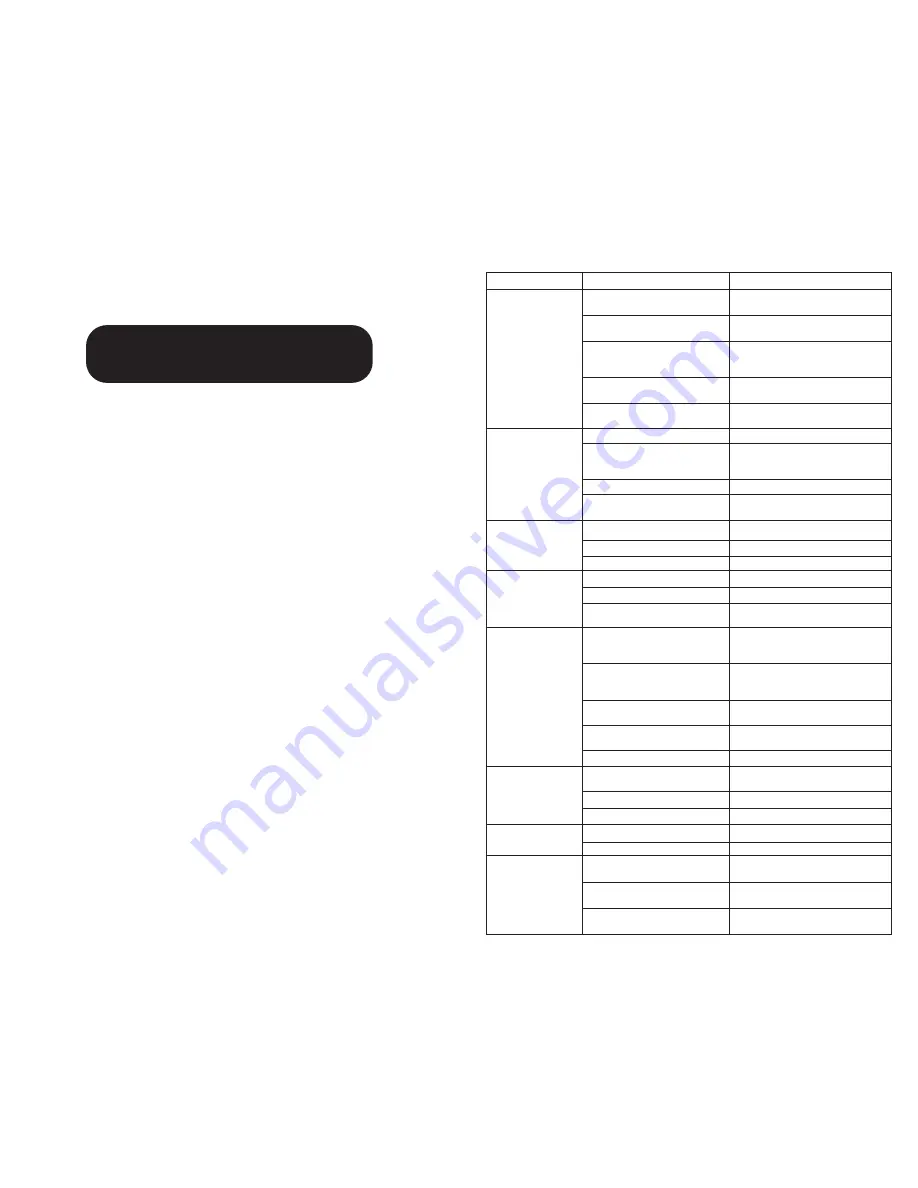
1-888-880-8368
Have your product proof of purchase with date ready for warranty issues.
Or write to:
Zephyr Corporation
Service and Warranty Department
395 Mendell Street
San Francisco, CA 94124
TO OBTAIN SERVICE UNDER WARRANTY
or any Service Related Questions, please call:
After installation, the unit
doesn’t work?
Light works, but motor is
not turning.
The unit is vibrating.
The motor is working,
but the lights are not.
The hood is not venting
out properly.
Heat lamp is not working.
Metal filter is vibrating.
Temperature Sensor is
not working.
1. The power source is not turned ON.
2. The power line and the cable locking
connector is not connecting properly.
3. The switch board and control board
wirings are disconnected.
4. On the switch board, Black/White wire or
White wire is disconnected.
5. The switch board or control board is
defective.
1. The motor is defective, possible seized.
2. The thermally protected system detects
if the motor is too hot to operate and
shuts the motor down.
3. Damaged condenser.
4. The Blue wire on the control board is
disconnected.
1. The motor is not secure in place.
2. Damaged blower wheel.
3. The hood is not secured in place.
1. Defective halogen bulb.
2. The light bulb is loose.
3. The RED wire on control board is
loosen.
1. The hood might be hanging to high from
the cook top.
2. The wind from the opened windows or
opened doors in the surrounding area
are affecting the ventilation of the hood.
3. Blocking in the duct opening or duct
work.
4. The direction of duct opening is
against the wind.
5. Using the wrong size of ducting.
1. Power on the heat lamp is not
turning on.
2. Heat lamp bulb is defective.
3. Heat lamp bulb is loose.
1. Metal filter is loose.
2. Spring clip is broken.
1. The right upper corner of LCD display
indicates “HI”.
2. The right upper corner of LCD display
indicates “LO”.
3. The right upper corner of LCD display
indicates “Err” after changing the Sensor.
1. Make sure the circuit breaker and the
unit’s power is ON.
2. Check the power connection with the
unit is connected properly.
3. Make sure the wirings between the switch
board and control board are connected
properly.
4. Make sure the Black/White wire or White
wire connects properly.
5. Change the switch board or control board.
1. Change the motor.
2. The motor will function properly after the
thermally protected system cool down.
3. Change the condenser.
4. Make sure the Blue wire on control board
is connected properly.
1. Tighten the motor in place.
2. Change the blower wheel.
3. Check the installation of the hood.
1. Change the halogen bulb.
2. Tighten the light bulb.
3. Make sure the RED wire on control board is
connected properly.
1. Adjust the distance between the cook top
and the bottom of the hood within 24” and
32” range.
2. Close all the windows and doors to eliminate
the outside wind flow.
3. Remove all the blocking from the duct work
or duct opening.
4. Adjust the duct opening direction.
5. Change the ducting to at least 8” or higher.
1. Make sure the heat lamp power is ON.
2. Change the heat lamp bulb.
3. Tighten the heat lamp bulb.
1. Change the metal filter.
2. Change the spring clip.
1. Change the sensor.
2. Change the sensor.
3. Change the switch board.
Issue
Cause
What to do
Troubleshooting Procedures for AK7500, AK700