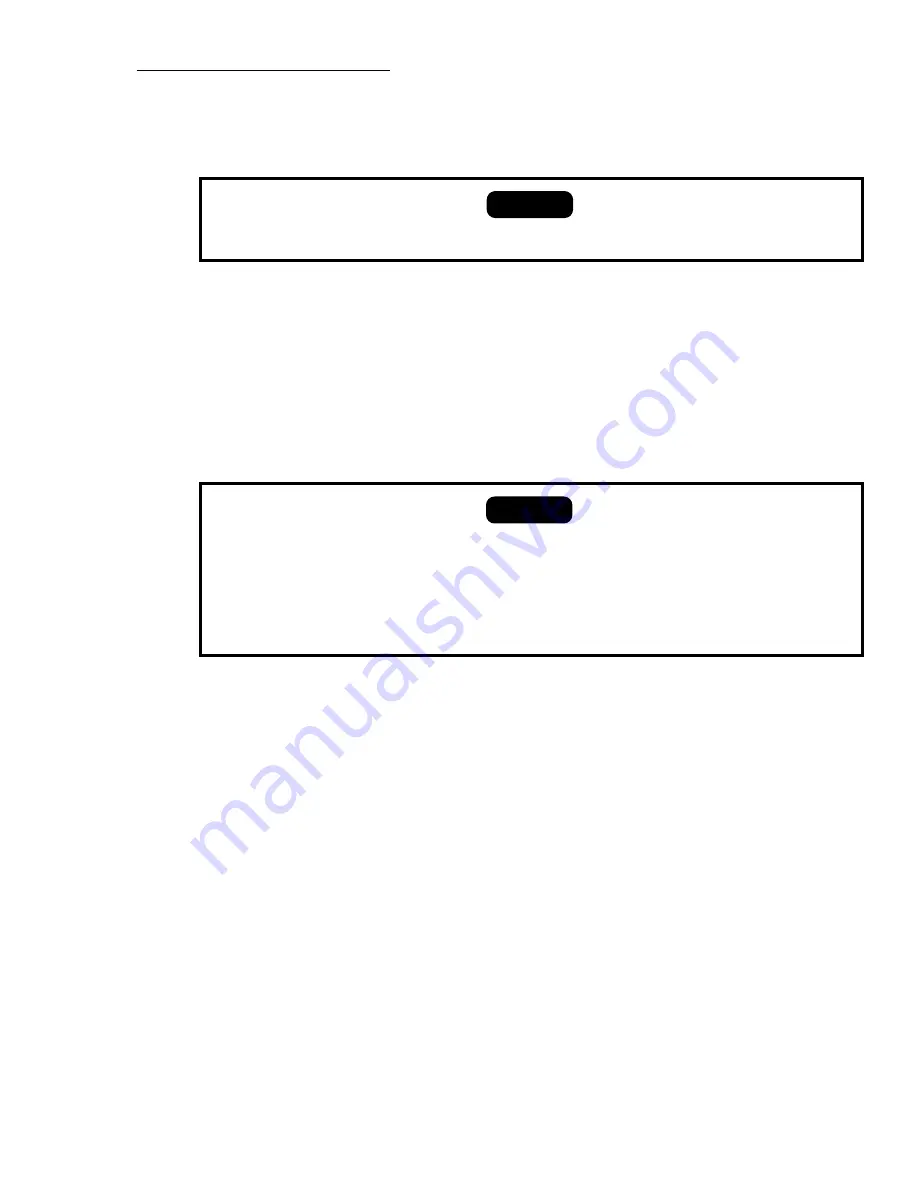
9
7.
INSTALLATION and START-UP
7.1
APPLICATION and CHECK ANALYSIS
To achieve the best dryer performance, you should carefully check that the design
and installation requirements outlined below are satisfied.
Operating pressure of ZEKS dryers can range from 75 -150 PSIG. Air available for
your usage will vary with operating pressure. The maximum design pressure of the
ZEKS Heatless Dryer is 150 PSIG. For units required for higher operating
pressures, consult your ZEKS representative.
The dryer must never be installed where air and/or ambient temperature exceeds
120°F or drops below +50°F. Locate dryer to avoid extremes of heat and cold from
ambient or other conditions. Avoid locating dryer outside or where it is exposed to
the elements.
7.2
LOCATING and MOUNTING
Lift the dryer only by the lifting points indicated on the General Arrangement
drawings furnished with dryer. Bolt the dryer to a suitable foundation using the bolt
holes provided in the base frame. Anchor bolts should project a minimum of two (2)
inches above the foundation. Refer to General Arrangement drawing for details.
7.3
PIPING
Pipe the compressed air lines to the inlet and outlet connections using piping and
fittings suitable for the maximum pressure rating of the system. Locate the prefilters
as close as possible to the dryer. Ensure the positioning allows for ease of
servicing. Refer to the General Arrangement drawing.
Note that the wet air inlet is at the dryer’s lower manifold, while the dry air outlet is
at the dryer’s upper manifold. In situations where air supply is required 24 hours a
day (where it is undesirable to have interrupted the airflow), a three valve by-pass
system is recommended to bypass the dryer. Use the fewest elbows necessary to
keep pressure drop at a minimum.
Once all piping has been connected, all joints including those on the dryer, should
be soap-bubble tested at line pressure to ensure no joints have been damaged in
transit and site placement.
The standard dryer is not rated for any gas other than air.
ZEKS recommends that the mufflers be removed prior to initial start up to allow
any desiccant dust generated during shipment to discharge. After running dryer
for 30 minutes, deenergize / depressurize dryer and reinstall mufflers. Note that
dryer operation will be
extremely loud
during this period. Proper hearing protec-
tion must be worn by all workers in the vicinity of the dryer during this procedure.
NOTICE
NOTICE