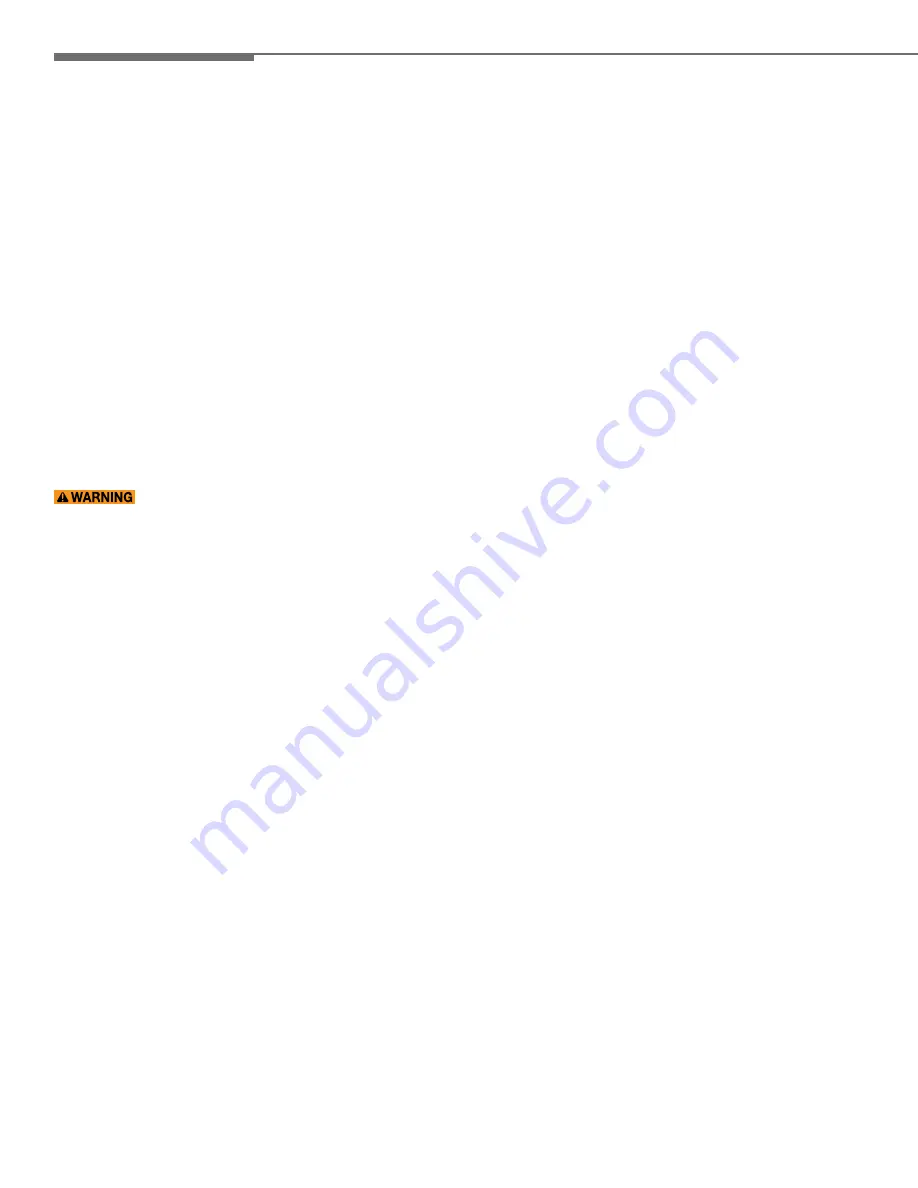
Normal operation and periodic maintenance
OPERATION AND MAINTENANCE
26
Coil
Coils may be cleaned by removing the motor/blower
assembly, providing access to the air entry side of the coil.
Brush the entire finned surface with a soft bristled brush,
brushing parallel to the fins, taking care not to damage the
fins. Brushing should be followed by cleaning with a vacuum
cleaner. Compressed air can also be used by blowing air
through the coil fins from the leaving air side, again followed
by vacuuming. If fins are damaged during the cleaning
process, a 12 fins per inch fin comb can be used to straighten
the fins. For a deeper cleaning, spray the finned surface with
a mild alkali cleaning solution and rinse thoroughly. Failure
to maintain a clean coil surface will result in reduced airflow,
reduced performance and increased power consumption.
Clean the coil at every inspection. Units provided with the
proper type of air filters, replaced regularly, will require less
frequent coil cleaning.
Electrical wiring & controls
Electrical operation of each unit is determined by the
components and wiring of the unit. This may vary from unit
to unit. Refer to the wiring diagram located in a zip-lock
plastic bag in the electrical end pocket of each unit for the
actual type and number of controls provided on each unit.
The integrity of all electrical connections should be verified
at least twice during the first year of operation. Afterwards,
all controls should be inspected regularly for proper
operation. Some components may experience erratic
operation or failure due to age. Thermostats may become
clogged with dust/lint, and should be periodically inspected
and cleaned to provide reliable operation.
When replacing any electrical components such as fuses,
contactors, relays or transformers, use only the exact type,
size and voltage component as furnished from the factory.
Any deviation from this could result in personnel injury
or damage to the unit and will void the manufacturer’s
warranty. All repair work should be done in such a way as to
maintain the equipment in compliance with governing local
and national codes, ordinances and safety testing agency
listings.
General
Each unit on a project will have its own unique operating
environment and conditions which dictate a maintenance
schedule for that unit that may be different from other
equipment on the project. A formal regular maintenance
schedule and an individual unit log should be established
and maintained. Following this schedule will help maximize
the performance and service life of each unit on the project.
The safety considerations listed in the front of this manual
should be followed during any service and maintenance
operations.
For more detailed service information consult your Sales
Representative or the factory.
Disconnect power supply from the unit before servicing.
Motor/blower assembly
The type of fan operation is determined by the control
components and their method of wiring. This may vary from
unit to unit. Refer to the wiring diagram located in a zip-lock
plastic bag in the electrical end pocket of each unit for that
unit’s individual operating characteristics.
All motors have permanently lubricated bearings so no
further field lubrication is ever required.
If the motor/blower assembly ever requires more extensive
service such as motor or blower wheel/housing replacement,
the entire assembly can be removed from the unit.
Dirt and dust should not be allowed to accumulate on the
blower wheel or housing. Failure to keep this clean may
result in an unbalanced wheel condition which can lead to
a damaged blower wheel or motor. The wheel and housing
may be cleaned periodically using a brush and vacuum
cleaner, taking care not to dislodge the factory applied
balancing weights on the blower wheel blades. Clean
the blower at every inspection. Any blower or motor that
is not properly maintained will not be covered under the
manufacturer’s warranty.
Содержание RW Series
Страница 31: ...29 SMART IDEAS Always the best climate for...