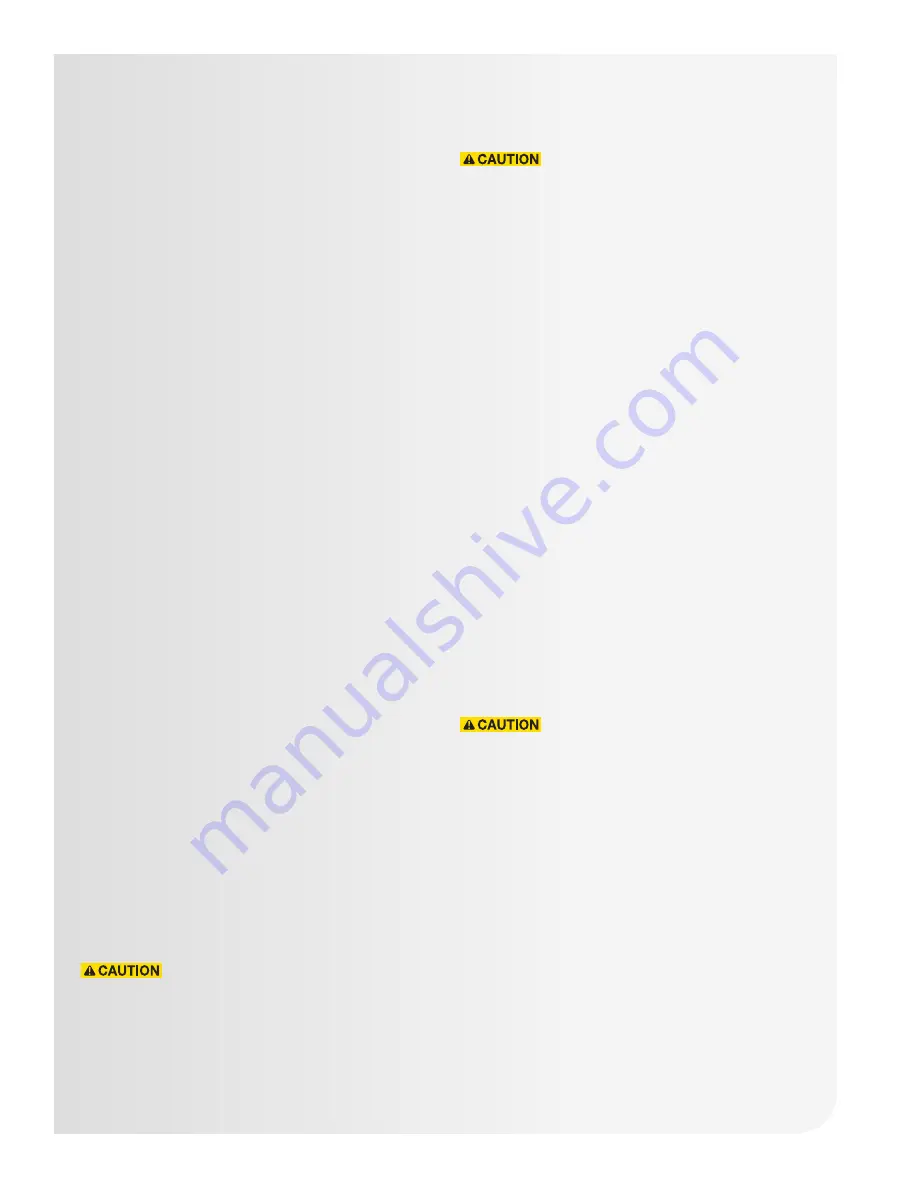
14
Installation positioning,
fastening and testing
Each riser is supplied with a 3-inch swaged portion
on the top and sufficient extension at the bottom for
an inserted length of approximately 2 inches. This
unit-to-unit joint is not intended for full bottoming in
the joint. When installing the Vertical Hi-Stack unit
to the unit below, the risers should never be pulled
down to engage in the swage connection. This is
already accounted for in the riser lengths and allows
for variations in floor-to-floor dimensions and correct
riser positioning.
Some jobs require that the unit risers be supplemented
with “between-the-floor” extensions. These pieces
should be assembled into position at this time.
“Between-the-floor” extensions may be field or factory
supplied. If the latter, insulation is also provided.
Once the units are positioned with the risers centered
in the pipe chase, each unit should be positioned
perfectly vertical (plumb) in two planes and anchored
to the building structure. All assemblies must be
adequately secured during lifting and rigging until
equipment is permanently fastened and set in its
final location. All temporary and permanent supports
must be capable of safely supporting the equipment’s
weight along with any additional live or dead loads
that may occur. All supports must be designed to
meet applicable local codes. All fastening devices
must be designed to mechanically lock the equipment
in place without the possibility of loosening or
breaking away due to system operation or vibration.
It is imperative that the unit be properly leveled
to assure condensate drainage and proper coil
operation. Once all units on a riser are anchored,
unit-to-unit riser joints may be made as follows: Each
branch run out in the coil section must be centered in
the expansion slot in the side or back panel prior to
joining risers. Ensure that clamps on drain pan P-trap
are secured and have not loosened during shipment
or installation.
Make sure the branch run out is pitched slightly
downward inside the unit so condensate, if formed,
will run back into the condensate pan and not out
toward the riser. Any water damage caused by not
following this procedure is not covered under the
warranty.
Make sure that the drain pan cover is in place prior to
start-up. Failure to have this properly installed may
prevent condensate drainage resulting in property
damage. Any water damage caused by not following
this procedure is not covered under the warranty.
Each riser joint must be in vertical alignment, with a
minimum of 1" penetration (although 2" is preferable
and allowed for) into each swaged joint. This condition
will be met if floor-to-floor dimension is as specified
and if each branch run out is properly centered. Riser
joints must be made with phos-copper, silfos, or
other high temperature alloys. Soft solders (50-50,
60-40, 85-15) or other low temperature lead alloys are
not suitable for this application. Use flame and heat
protection barriers where needed during soldering
or brazing process to protect adjacent flammable
materials. Care should be taken to assure that no
valve package components are subjected to high
temperature, which may damage seals or gaskets.
If the valve package connection at the coil is made
with a union, the coil side of the union must be
prevented from twisting during tightening to prevent
damage to the coil tubing. Over-tightening must be
avoided to prevent distorting the union seal surface
and destorying the union, ultimately causing a leak.
Secure the union nut hand-tight and then tighten no
more than an additional 1/4 turn.
Wide variations in floor-to-floor dimensions may
necessitate cutting off or extending individual risers.
Such modifications are the full responsibility of the
installing contractor.
The risers must not be rigidly fastened within each
unit, but must be free to move within the pipe chase
with normal vertical expansion and contraction
movements.
The installing contractor must anchor the built-in
risers at some point to the building structure. The
unit design will accommodate up to a 1" expansion
and contraction (2" total movement). The installing
contractor must provide and install additional
expansion compensation devices in each riser. Venting