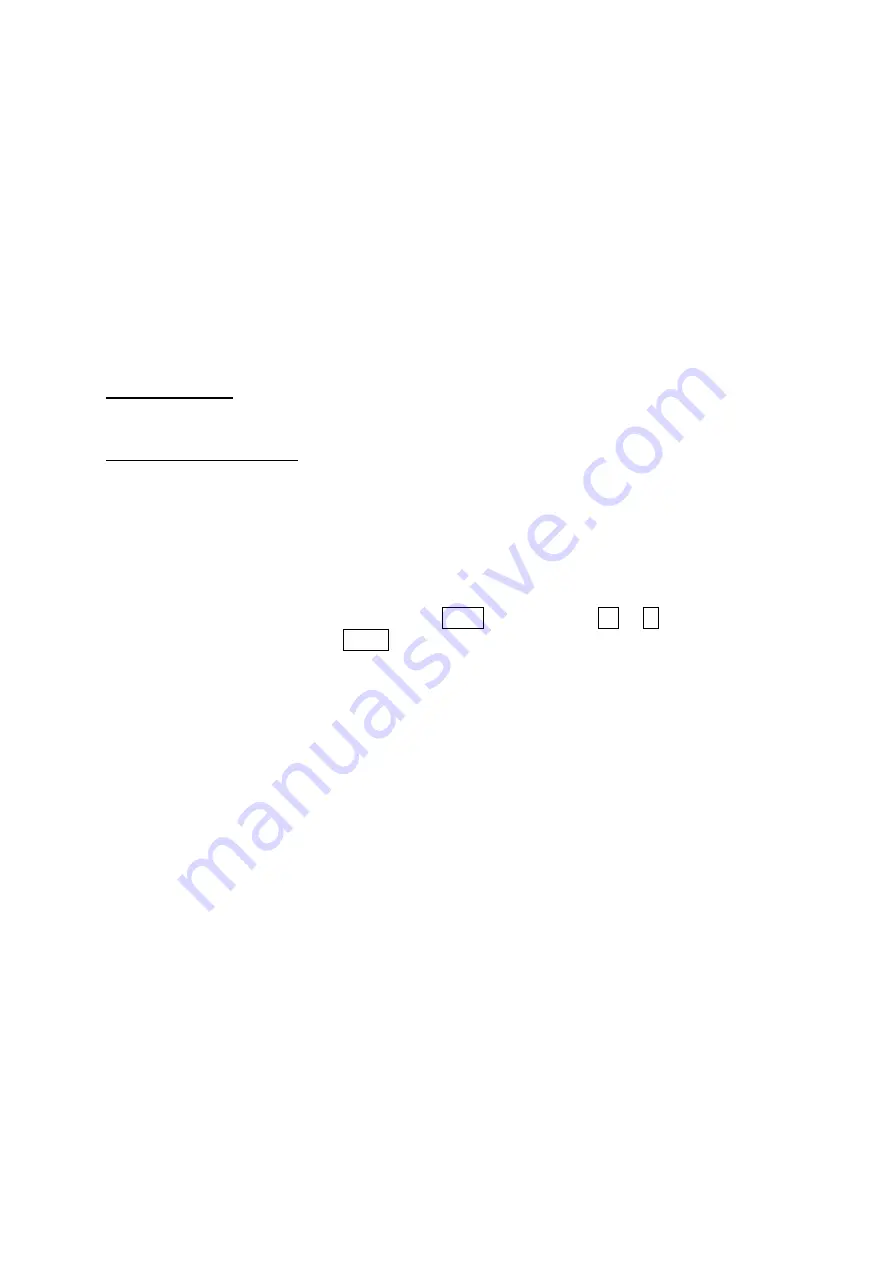
- 2 -
- 3D interpolated ignition map, if TPS selected
- signal delay compensation
- instant monitoring of rev's and angle, via LCD(hand held programmer)
- programmable power valve actuation
- store and load function for 5 PV curves
- external switch for changing PV curve while riding
- programmable PV deviation
- programmable max close and max open positions
- self PV test on power-up
- PV error detecting (position sensor failure, servo motor failure)
- fast processing for high accuracy - delays from 1us
- timing calculation for every 1 RPM change (1000, 1002, .. , 9805, 9806, ...)
Very important!
Resistor spark plugs must be used, because they produce less electromagnetic disturbances.
Danger of electric shock!
Avoid connecting PDCI to 12V power supply, before connecting it to ignition coil. High voltage
is generated and touching free wires can cause electric shock, or damage the unit.
1.
HOW TO ENTER MENU
PDCI
must be connected to power supply. Connect
programmer
to
PDCI
and wait few seconds
for activation of
programmer
and then press enter. With pressing + or - you can move
through menu and with pressing enter you can choose.
You can exit menu with choosing
Exit.
2.
MENU ORGANISATION
Set Ign.
- set ignition parameters submenu
Set PV
- set PV parameters submenu
Exit
2.1.
SET IGNITION PARAMETERS SUBMENU
Load Ign. Map
- load (select) ignition map (from #1 to #2)
Save Ign. Map
- save new ignition map (from #1 to #2)
Set Ignition Map
- ignition map parameters submenu
Advance
- advance/retard whole ignition map on both ignition coil outputs
Advance 1
- advance/retard ignition coil output 1
Advance 2
- advance/retard ignition coil output 2
Gear Shift Light
- shift light
Quick Shift
- quick shift settings
Rev Limit
- rev limit
Static Angle
- static angle (stator position)
Compensation
- signal delay compensation (from pickup to spark plug)
Power Jet 1
- power jet 1