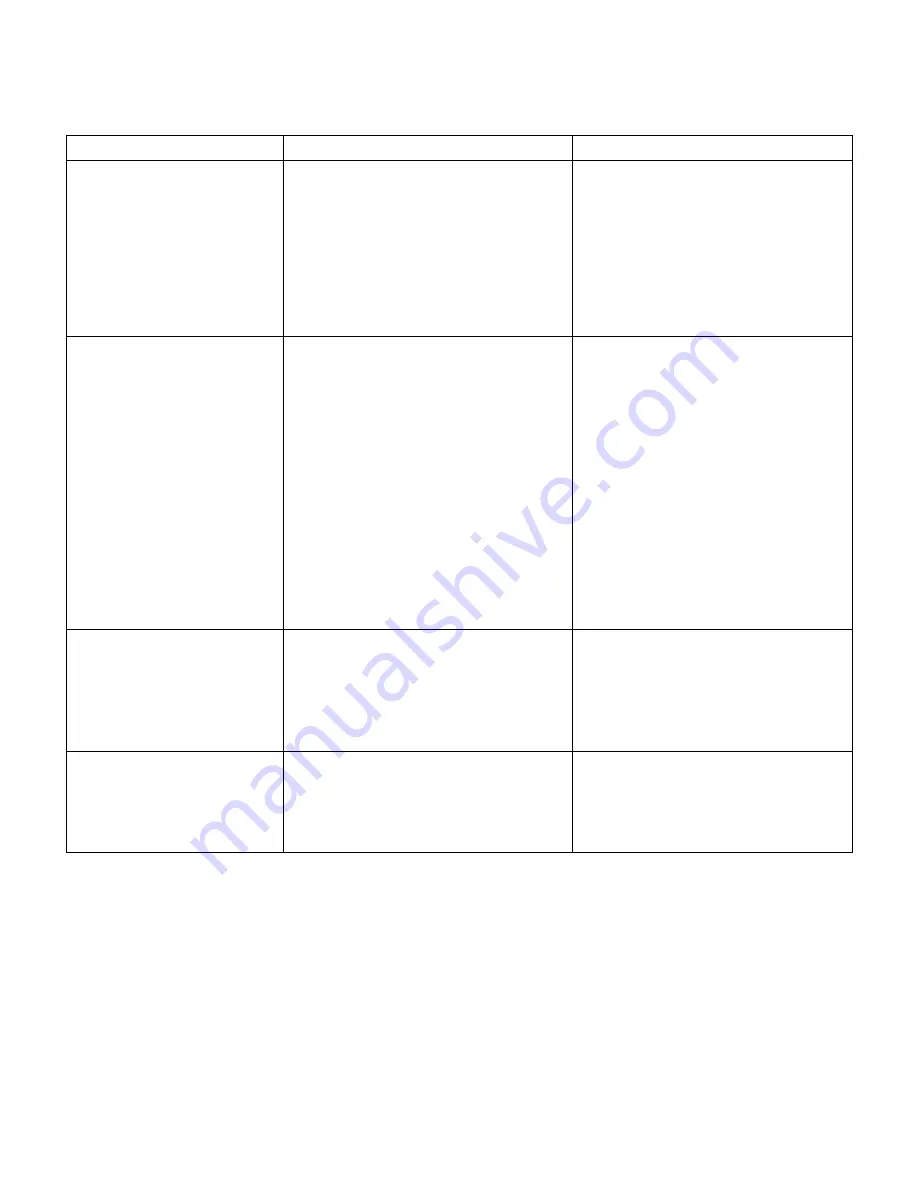
33
TROUBLE SHOOTING CHART
SYMPTOM
CAUSES
CHECK & CORRECTIVE MEASURE
1. High load on evaporator. Load in ex-
cess of design conditions.
2. Unbalanced system. Oversized air han-
dling unit matched with under sized
condensing unit.
3. Compressor discharge valve leaking.
4. Expansion valve widely open.
5. Improper bulb location or installation.
Loss of oil pressure.
Relay defective or burned out.
1. Loss of oil from compressor due to:
(a) Oil trapping in system.
(b) Compressor short cycling.
(c) Insufficient oil in system.
(d) Operation at excessively low suction
pressure.
2. Excessive liquid refrigerant returning to
compressor.
3. Malfunctioning oil pump.
4. Restriction in oil pump inlet screen.
1. Incorrect relay.
2. Incorrect mounting angle.
3. Line voltage too high or too low.
4. Excessive short cycling.
5. Relay being influenced by loose mounting.
1. Check the design.
2. Follow manufacturer's guide line and
correct it.
3. Repair/replace compressor.
4. Check and adjust the superheat ac-
cordingly.
5. Check the expansion valve bulb is
properly tighten at correct location.
High suction pressure.
1. (a) Correct the system piping.
(b) Trace out the wiring/defective con-
trols/components, etc. and correct it.
(c) Add oil.
(d) Check the superheat of expansion
valve and other possible causes
like clogged filter, low CFM, iced
evaporator etc. & correct it.
2. Check the system for correct super-
heat & other possible causes like
clogged filter, low CFM, iced evapo-
rator, etc. and correct it.
3. Repair or replace it.
4. Clean/replace it (oil change recommended).
1. Check and replace.
2. Remount relay in correct position.
3. Determine reason and correct.
4. Determine reason and correct.
5. Remount rigidly.
Unit noisy.
1. Loose parts or mountings.
2. Tubing rattle.
3. Bent fan blade causing vibration.
4. Fan motor bearings worn.
1. Find and tighten.
2. Tighten the pipe support.
3. Replace blade.
4. Replace motor.