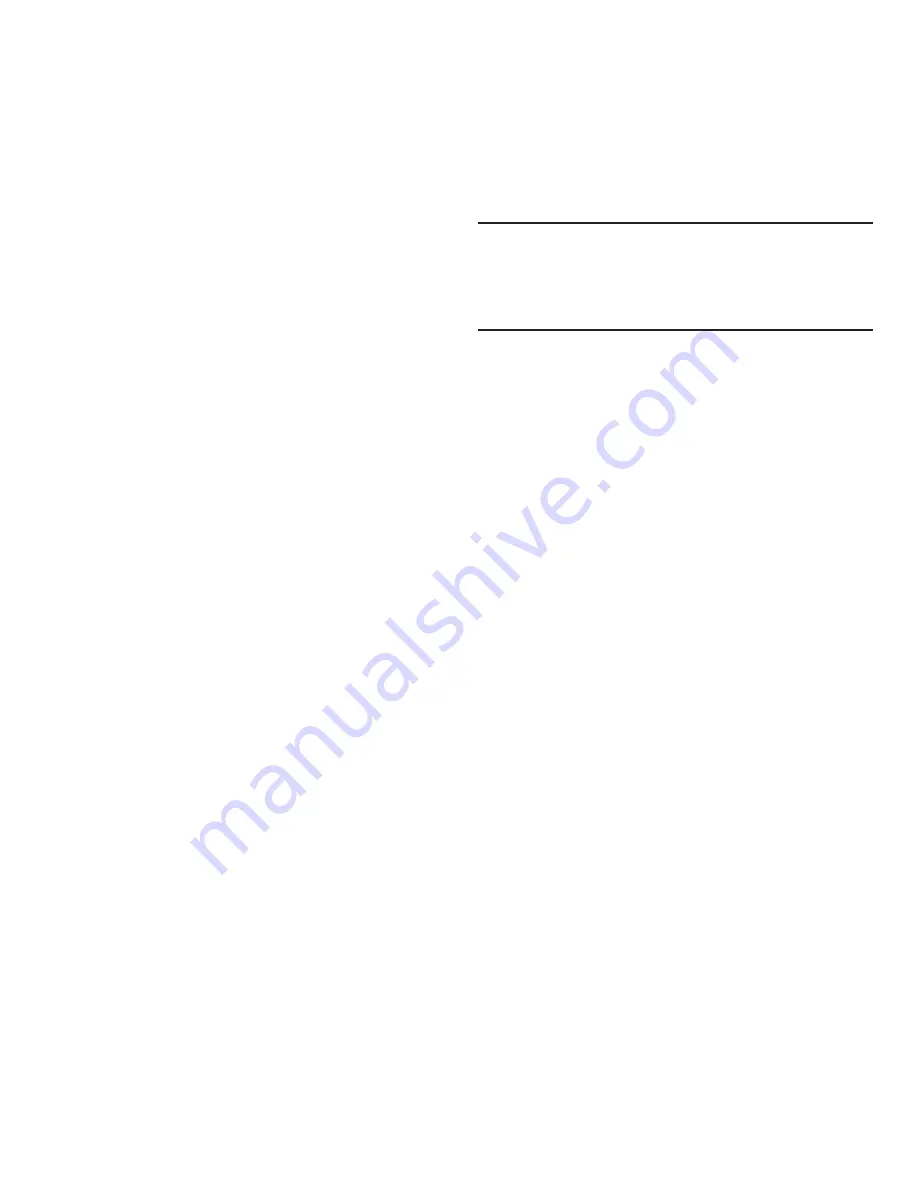
YZ Systems Milton Roy • 201 Ivyland Road • Ivyland, Pennsylvania • USA • 18974 • P: 281.362.6500 • www.yzsystems.com
DP-2010 ver.05-2018
Page 16
s
eCTion
9: s
ysTem
m
ainTenanCe
Preventative Maintenance
Schedule
A preventative maintenance program
serves to anticipate maintenance issues
prior to waiting until the system requires
service. Like changing the oil & filters in
an automobile, by choosing to service the
various parts and operation in the Sampling
System at regular intervals, the technician
can perform the maintenance service when
desired, rather than when required, such as
in the middle of night.
The key is to perform maintenance before it
is required. The preventative maintenance
schedule implemented should consider the
application of the sampler. Many of these
considerations include: the weather envi-
ronment; the condition of, the actuation gas,
the product condition and quality, and the
pump stroke frequency. All of these issues
must be considered when establishing a
preventative maintenance schedule.
Recommended Maintenance Schedule
Monthly Inspection
1. Verify system pressure
2. Check for leaks
3. Test the battery.
4. Test the system for leaks each time a
fitting or connection has been made.
Semi-Annual Inspection
1. Clean and lubricate the sample pump
2. Check the filter element, and replacing
as necessary.
Annual Inspection
1. Rebuild pump
2. Test the Sampler System performance
and service, as needed
3. Replace Z-65 Battery Assembly.
Recommended Spare Parts List
Part # Description
Recommended
Quantity
D3-0002 DP-2000 pump seal
replacement kit
1
D3-0003 Filter Regulator repair kit 1
A4-0001 Solenoid
1
E3-2001 Z-65 Battery Assembly
1
Содержание DynaPak DP-2010
Страница 1: ...DynaPak Gas Sampler S Y S T E M S U P P O R T M A N U A L DP 2010 V e r s i o n s D F J K L S T D ...
Страница 2: ...DP 2010 Instruction Operating Manual Version 05 2018 ...
Страница 38: ...201 Ivyland Road Ivyland PA 18974 P 800 653 9435 P 281 362 6500 E sales yzhq com www yzsystems com ...