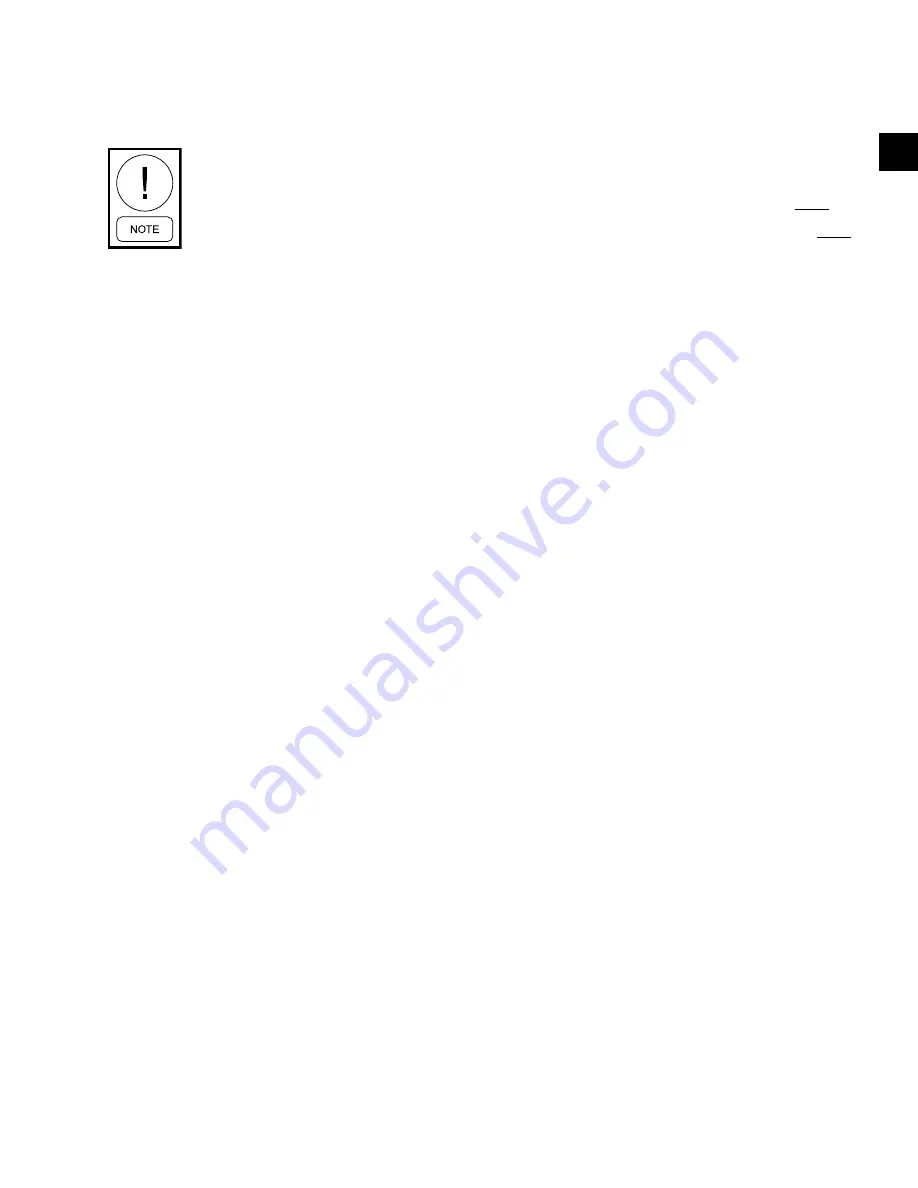
JOHNSON CONTROLS
11
SECTION 2 - SYSTEM OPERATING PROCEDURES
FORM 160.76-O1
ISSUE DATE: 6/15/2015
2
For display messages and information pertaining to the
operation refer to
Optiview™ Control Center – Opera-
tion and Maintenance (Form 160.54-O1)
.
Any malfunctions which occur during
STOP/RESET are also displayed.
CHILLER OPERATION
The unit capacity will vary to maintain the leaving
CHILLED LIQUID TEMPERATURE setpoint by the
Pre-rotation Vanes which are modulated by an actua-
tor under the control of the Microprocessor Board. The
vane control routine employs proportional plus deriva-
tive (rate) control action. A drop in chilled liquid tem-
perature will cause the actuator to close the Prerotation
Vanes to decrease chiller capacity. When the chilled
liquid temperature rises, the actuator will open the Pre-
rotation Vanes to increase the capacity of the chiller.
However, the current draw (amperes) by the compres-
sor motor is also limited to FLA setpoint by the micro-
processor.
If the load continues to decrease, after the Prerotation
Vanes are entirely closed, the chiller will be shut down
by the Leaving Chilled Liquid – Low Temperature
Control.
The coolant temperature inside any JCI-supplied liq-
uid-cooled motor starter must be maintained above the
dewpoint temperature in the equipment room to pre-
vent condensing water vapor inside the starter cabinet.
Therefore, an additional temperature-controlled throttle
valve is needed in the flow path for the starter heat ex-
changer to regulate cooling above the equipment room
dewpoint for applications using cooling sources other
than evaporative air-exchange methods, such as wells,
bodies of water, and chilled water. The temperature
control valve should be the type to open on increasing
drive coolant temperature, fail-closed, and set for a tem-
perature above dewpoint. It can be requested as factory-
supplied on a chiller order by special quotation.
CONDENSER WATER TEMPERATURE
CONTROL
The YORK chiller is designed to use less power by tak-
ing advantage of lower than design temperatures that
are naturally produced by cooling towers throughout
the operating year. Exact control of condenser water
such as a cooling tower bypass, is not necessary for
most installations. The minimum entering condenser
water temperature for full and part load conditions is
specified in the chiller engineering guide.
where:
Min. ECWT = LCWT – C RANGE + 5ºF + 12 ( )
Min. ECWT = LCWT – C RANGE + 2.8ºC + 6.6 ( )
ECWT = Entering Condensing Water Temperature
LCWT = Leaving Chilled Water Temperature
C Range = Condensing water temperature range at the
given load condition.
% Load
100
% Load
100
At start-up, the entering condenser water temperature
may be as much as 25°F (14°C) colder than the stand-
by return chilled water temperature. Cooling tower fan
cycling will normally provide adequate control of the
entering condenser water temperature on most instal-
lations.
Heat recovery chillers and chillers using optional head
pressure control would use a signal provided by the
microprocessor to control main condenser bundle heat
rejection or pressure, respectively.
OPERATING LOG SHEET
A permanent daily record of system operating condi-
tions (temperatures and pressures) recorded at regular
intervals throughout each 24 hour operating period
should be kept.
An optional status printer is available for this purpose
or
shows a log sheet used by
Johnson Controls Personnel for recording test data on
chiller systems. It is available from the factory in pads
of 50 sheets each under Form 160.44-F7 and may be
obtained through the nearest Johnson Controls office.
Automatic data logging is possible by connecting the
optional printer and programming the DATA LOG-
GER function.
An accurate record of readings serves as a valuable ref-
erence for operating the system. Readings taken when
a system is newly installed will establish normal condi-
tions with which to compare later readings.
For example, an increase in condenser approach tem-
perature (condenser temperature minus leaving con-
denser water temperature) may be an indication of
dirty condenser tubes.