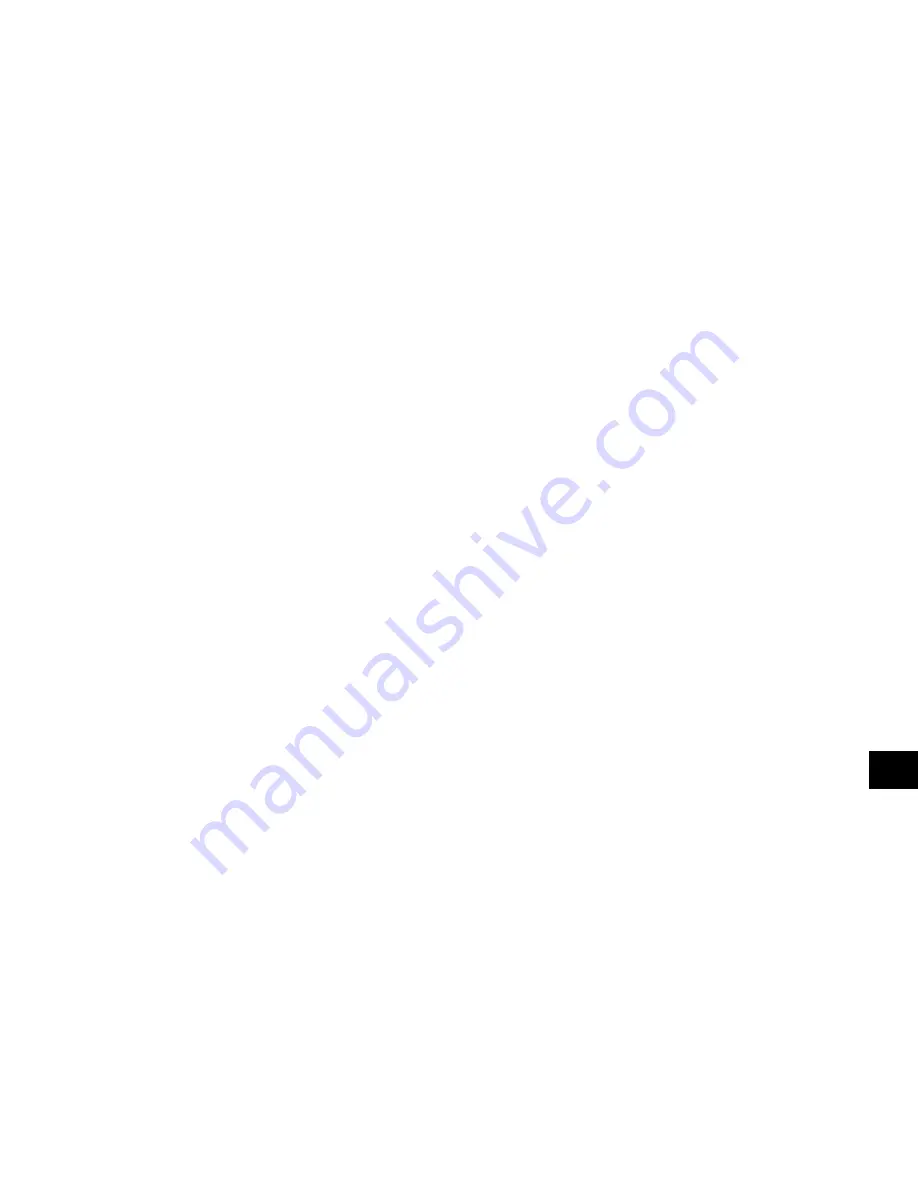
30
JOHNSON CONTROLS
INSTALLATION
LOCATION REQUIREMENTS
To achieve optimum performance and trouble-free
service, it is essential that the proposed installation site
meets with the location and space requirements for the
model being installed. For dimensions, weight and space
requirements, including service access details, refer to
the Technical Data Section.
It is important to ensure that the minimum service ac-
cess space is maintained for cleaning and maintenance
purposes.
OUTDOOR INSTALLATIONS
The units can be installed at ground level, or on a
suitable rooftop location. In both cases an adequate
supply of air is required. Avoid locations where the
sound output and air discharge from the unit may be
objectionable.
The location should be selected for minimum sun ex-
posure and away from boiler flues and other sources of
airborne chemicals that could attack the condenser coils
and steel parts of the unit.
If located in an area which is accessible to unauthorized
persons, steps must be taken to prevent access to the
unit by means of a protective fence. This will help to
prevent the possibility of vandalism, accidental damage,
or possible harm caused by unauthorized removal of
protective guards or opening panels to expose rotating
or high voltage components.
For ground level locations, the unit must be installed
on a suitable flat and level concrete base that extends
to fully support the two side channels of the unit base
frame. A one-piece concrete slab, with footings ex-
tending below the frost line is recommended. To avoid
noise and vibration transmission the unit should not be
secured to the building foundation.
On rooftop locations, choose a place with adequate
structural strength to safely support the entire operating
weight of the unit and service personnel. The unit can
be mounted on a concrete slab, similar to ground floor
locations, or on steel channels of suitable strength. The
channels should be spaced at the same centres as the
vibration mounting holes in the unit base frame and must
be at least 4-3/4” (120 mm) wide at the contact points.
This will allow vibration isolators to be fitted if required.
Any ductwork or attenuators fitted to the unit must not
have a total static pressure resistance, at full unit airflow,
exceeding the capability of the fans installed in the unit.
INDOOR INSTALLATIONS
The unit can be installed in an enclosed plant room
providing the floor is level and of suitable strength to
support the full operating weight of the unit. It is essen-
tial that there is adequate clearance for airflow to the
unit. The discharge air from the top of the unit must be
ducted away to prevent recirculation of air within the
plant room. If common ducts are used for fans, non-re-
turn dampers must be fitted to the outlet from each fan.
The discharge ducting must be properly sized with a
total static pressure loss, together with any intake stat-
ic pressure loss, less than the available static pressure
capability for the type of fan fitted.
The discharge air duct usually rejects outside the build-
ing through a louver. The outlet must be positioned to
prevent the air being drawn directly back into the air
intake for the condenser coils, as such recirculation will
affect unit performance.
LOCATION CLEARANCES
Adequate clearances around the unit(s) are required for
the unrestricted airflow for the air-cooled condenser
coils and to prevent recirculation of warm discharge
air back onto the coils. If clearances given are not
maintained, airflow restriction or recirculation will
cause a loss of unit performance, an increase in power
consumption and may cause the unit to malfunction.
Consideration should also be given to the possibility of
down drafts, caused by adjacent buildings, which may
cause recirculation or uneven unit airflow.
For locations where significant cross winds are expect
-
ed, such as exposed roof tops, an enclosure of solid or
louver type is recommended to prevent wind turbulence
interfering with the unit airflow.
4
Содержание YCAS 0138EB
Страница 36: ...36 JOHNSON CONTROLS POWER AND CONTROL PANEL LAYOUTS WYE DELTA TYPICAL FIG 8 POWER PANEL SECTION 00263VIP 4...
Страница 50: ...50 JOHNSON CONTROLS This page intentionally left blank...
Страница 61: ...61 JOHNSON CONTROLS FORM 201 18 NM7 This page intentionally left blank 7...
Страница 64: ...64 JOHNSON CONTROLS Technical Data ELEMENTARY DIAGRAM FIG 18 ELEMENTARY DIAGRAM ACROSS THE LINE START...
Страница 68: ...68 JOHNSON CONTROLS Technical Data ELEMENTARY DIAGRAM FIG 21 ELEMENTARY DIAGRAM WYE DELTA START...
Страница 70: ...70 JOHNSON CONTROLS Technical Data FIG 22A CONTROL PANEL COMPONENT LOCATIONS...
Страница 71: ...71 JOHNSON CONTROLS FORM 201 18 NM7 LD03280 FIG 22B POWER PANEL COMPONENT LOCATION 7...
Страница 72: ...72 JOHNSON CONTROLS Technical Data LEGEND LD03281...
Страница 73: ...73 JOHNSON CONTROLS FORM 201 18 NM7 LD03282 LD03283 LD03284 7...
Страница 74: ...74 JOHNSON CONTROLS Technical Data CONNECTION DIAGRAM SYSTEM WIRING LD06256 LD03231 LD03232...
Страница 75: ...75 JOHNSON CONTROLS FORM 201 18 NM7 COMPRESSOR TERMINAL BOX LD03233 7...
Страница 76: ...76 JOHNSON CONTROLS LD03285 Technical Data...
Страница 77: ...77 JOHNSON CONTROLS FORM 201 18 NM7 3 4 5 6 3 4 5 6 7 8 5 6 3 4 7 8 9 10 LD06840A 7...
Страница 113: ...113 JOHNSON CONTROLS FORM 201 18 NM7 COMPRESSOR COMPONENTS CONT D FIG 40 COMPRESSOR COMPONENTS LD03669 7...
Страница 114: ...114 JOHNSON CONTROLS COMPRESSOR COMPONENTS CONT D FIG 41 COMPRESSOR COMPONENTS LD03670 Technical Data...
Страница 181: ...181 JOHNSON CONTROLS FORM 201 18 NM7 NOTES...
Страница 182: ...182 JOHNSON CONTROLS This page intentionally left blank...
Страница 183: ...183 JOHNSON CONTROLS FORM 201 18 NM7 This page intentionally left blank...