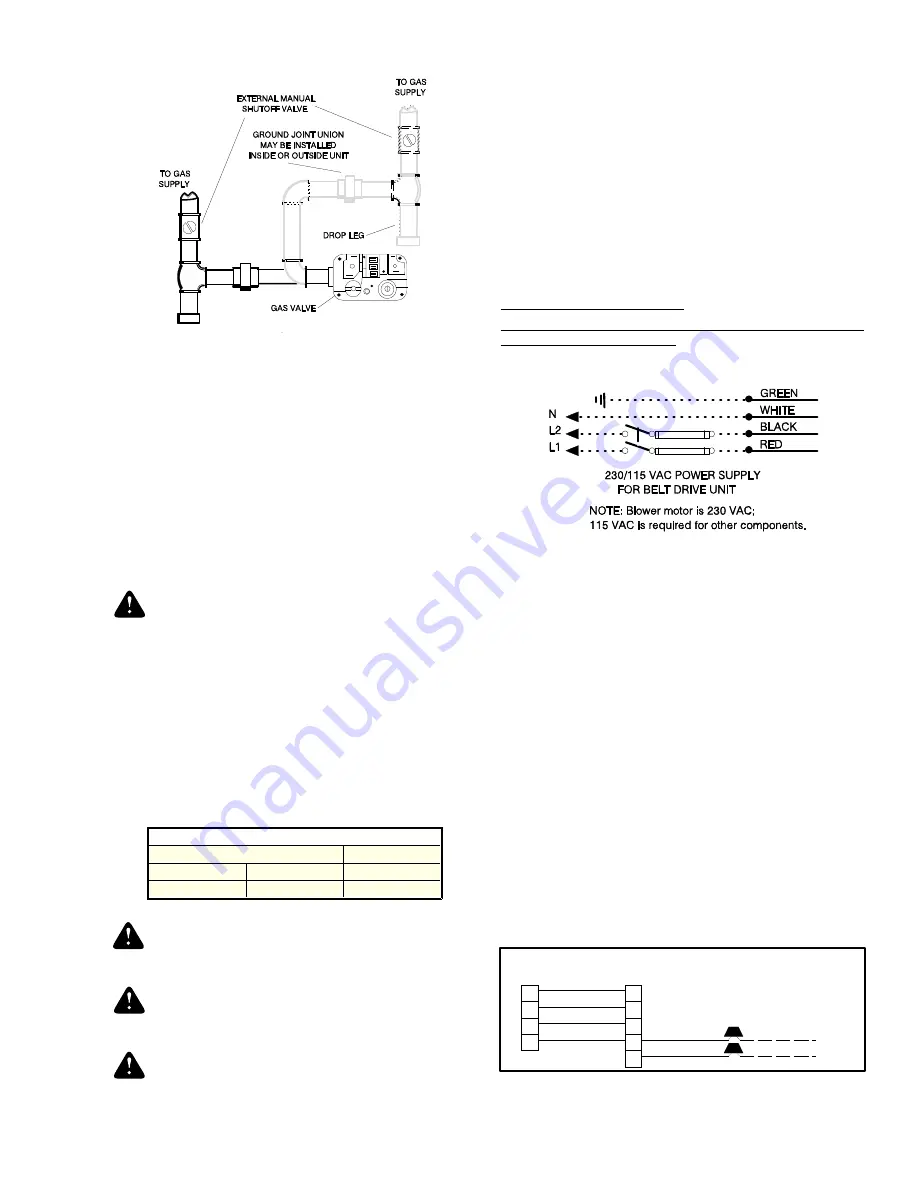
GAS PIPING
NOTE: An accessible manual shutoff valve must be
installed upstream of the furnace gas controls and
within 6 feet of the furnace. A 1/8" NPT plugged
tapping, accessible for test gauge connection,
should be installed immediately upstream of the
gas supply connection to the furnace.
The furnace and its individual shutoff valve must be disconnected
from the gas supply piping system during any pressure testing of
that system at test pressures in excess of 1/2 psig (3.48 kPa).
The furnace must be isolated from the gas supply piping
system by closing its individual external manual shutoff valve
during any pressure testing of the gas supply piping system at
test pressures equal to or less than 1/2 psig (3.48 kPa).
CAUTION: Never apply a pipe wrench to the body of
the combination automatic gas valve. A wrench must
be placed on the projection or wrench boss of the
valve when installing piping to it.
Gas piping may be connected from either side of the furnace.
Sizing and installation of the supply gas line should comply with
the local utility requirements.
The gas supply should be a separate line, installed in accord-
ance with the National Fuel Gas Code, ANSI Z223.1, or
CAN/CGA B149.1 or .2 Installation Codes - (latest editions).
Some utility companies, or local codes, require pipe sizes
larger than the minimum sizes listed. Using the properly sized
wrought iron, approved flexible or steel pipe, make gas con-
nections to the unit. Installation of a drop leg and ground union
is required (See Figure 4).
WARNING: Compounds used on threaded joints of
gas piping must be resistant to the action of liquified
petroleum gases.
WARNING: After all gas piping connections are com-
pleted, leak test all joints, fittings and furnace connec-
tions with rich soap and water solution, commercial
available bubble type leak detection fluid, or other
approved means.
WARNING: Do not use an open flame or other source
of ignition for leak testing.
ELECTRICAL POWER CONNECTION
Field wiring to the unit must conform to and be grounded in
accordance with the provisions of the National Electrical Code
ANSI/NFPA No. 70 -latest edition, Canadian Electric Code
C22.1 Part 1 - (latest edition) and/or local codes. Electrical
wires which are field installed shall conform with the tempera-
ture limitation for 63
°
F/35
°
C rise wire when installed in accord-
ance with instructions. Specific electrical data is given on the
furnace rating plate.
Provide a power supply separate from all other circuits. Install
overcurrent protection and disconnect switch per local/national
electrical codes. The switch should be reasonable close to the
unit for convenience in servicing. With the disconnect switch in
the OFF position, check all wiring against the unit wiring label.
Also, see the wiring diagram in this instruction.
Use copper conductors only.
This unit requires both 230 & 115 volt power supplies. A neutral
conduction must be provided.
NOTE: The furnace’s control system depends on
correct polarity of the power supply.
Connect the power supply as shown on the unit wiring label on
the inside of the blower compartment door and Figure 5. The
white furnace lead must be connected to neutral. Also, the
green equipment ground wire must be connected to the power
supply ground.
Remove the screw retaining the wiring box. Route the power
wiring through the unit side panel with a conduit connector or
other proper connection. Make wiring connections as shown in
Figure 5. Replace the wiring box and screw.
An alternate wiring method is to use a field provided 2 x 4 box
and cover on the outside of the furnace. Route the furnace
leads into the box using a protective bushing where the wires
pass through the furnace panel.
ELECTRICAL CONTROL CONNECTIONS
Install the field-supplied thermostat. The thermostat instruc-
tions for wiring are packed with the thermostat. With the
thermostat set in the OFF position and the main electrical
source disconnected, complete the low-voltage wiring from the
thermostat to the terminal board on the low-voltage transformer.
Connect Class 2 control wiring as shown in Figure 6.
INLET GAS PRESSURE RANGE
Natural Gas
Propane (LP)
Minimum
4.5 In. W.C.
11 In. W.C.
Maximum
13.8 In W.C.
13.8 In. W.C.
FIGURE 4 - GAS PIPING
FIGURE 5 - POWER CONNECTIONS
ROOM
THERMOSTAT
FURNACE
TRANSFORMER
CONDENSING
UNIT
TO AIR CONDITIONER
CONTROLS
R
W
G
Y
C
R
W
G
Y
FIGURE 6 - TYPICAL HEATING AND COOLING
650.64-N4
Unitary Products Group
7