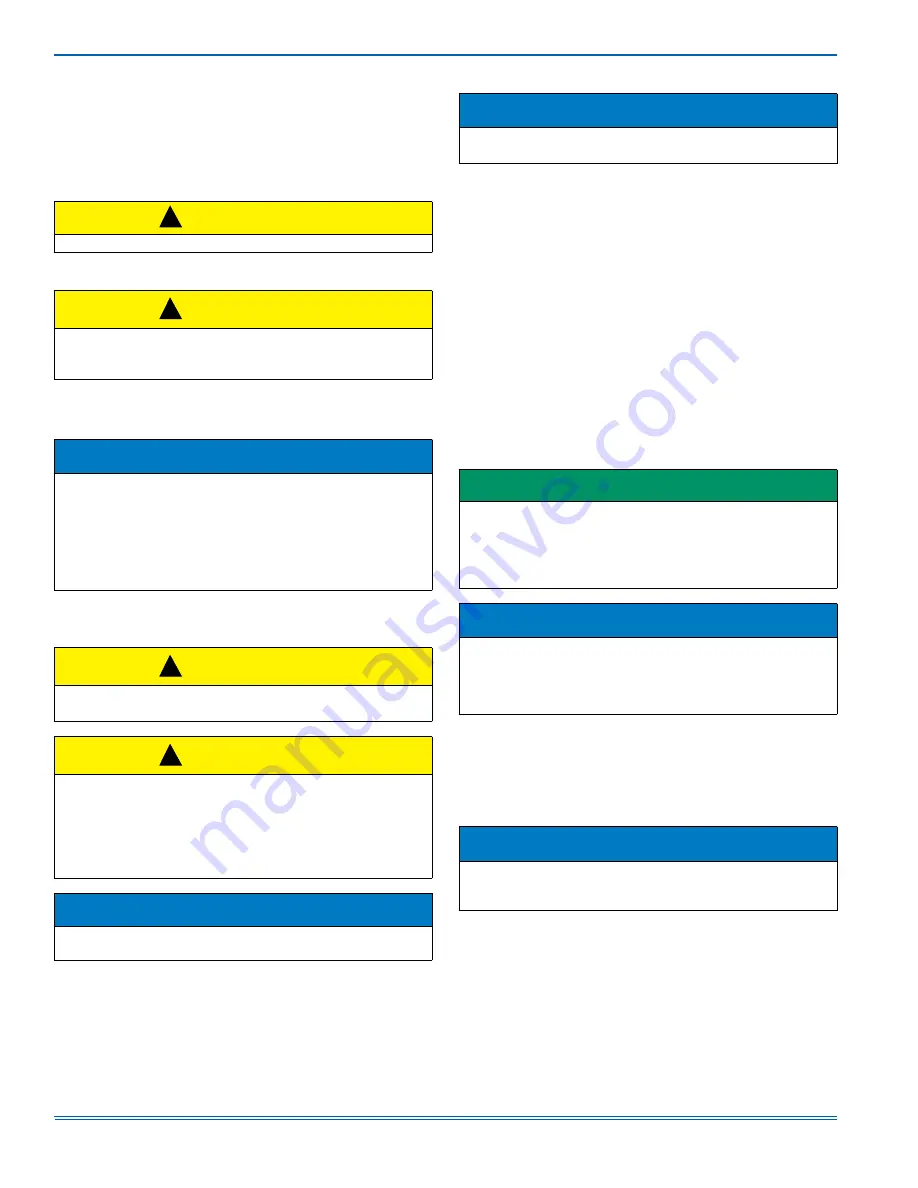
5292157-UIM-B-0317
8
Johnson Controls Unitary Products
AIR FILTERS
Return air filters are required and must be field supplied. Filtration can
be accomplished external to the unit or the integral filter rack may be
used. A 1" filter access rack has been built into the unit. Remove filter
access cover shown. Install proper size filter. Standard 1" size
permanent or throw away filter may be used, or permanent washable
filters are available using model numbers: 1PF0601, 602 or 603. See
Table 5 for filter size.
.
SECTION V: COIL METERING DEVICES
This unit is supplied with a factory installed Electronic Expansion Valve
(EEV). The EEV, the temperature sensor, and the pressure transducer
are factory wired to the control board.
SECTION VI: REFRIGERANT LINE
CONNECTION
Connect lines as follows:
1.
Suction and liquid line connections are made outside the cabinet.
Leave the tubing connection panel attached to the cabinet. Coil
access panel should be removed for brazing. The lines are
expanded to receive the field line set tubes for most outdoor unit
matches.
2.
Remove grommets where tubes exit the cabinet to prevent burning
them during brazing. In some units, the vapor line grommet may be
shipped as a loose part with the unit. Refer to Figure 10.
3.
Cut the end of the suction tube using a tube cutter. Place the tube
cutter as close as possible to the end of the tube to allow as much
depth as possible for the connection and brazing of the suction line.
To ensure suction line fits into connection, deburr the stub out
(including inner pressure protrusion from cutting).
4.
Remove the liquid line copper cap which is soft soldered onto the
outside of the 3/8” stub protruding from front of the coil cabinet tub-
ing panel as follows:
a.
Screw a sheet metal screw into the center of the cap.
b.
Apply a small amount of heat to the cap while pulling on the
screw using slip joint pliers.
5.
Insert liquid and suction lines into the coil connections at the coil
cabinet tubing panel.
6.
Wrap a water soaked rag around the coil connection tubes inside
the cabinet to avoid transferring excess heat to the coil, the EEV,
the temperature sensor or the pressure transducer.
7.
Purge refrigerant lines with dry nitrogen.
8.
Braze the suction and liquid lines, and allow the joints to cool.
9.
Re-attach the grommets to the lines carefully to prevent air leak-
age. In some units, the vapor line grommet may be shipped as a
loose part with the unit. Refer to Figure 10.
CAUTION
Equipment should never be operated without filters.
CAUTION
COIL UNDER PRESSURE.
Verify that pressure has been released by depressing schrader valve
core.
NOTICE
To prevent moisture and contaminates from entering the system, the
coil should not be open to atmosphere for extended periods of time. If
the coil cannot be brazed into the refrigeration system during a rou-
tine installation period, the ends should be temporarily closed or
plugged. For a short term delay, use masking tape over the ends of
the copper tubing to close the tube from the air. For a longer term
delay, use plugs or caps. There is no need to purge the coil if this pro-
cedure is followed.
CAUTION
Coil is under inert gas pressure. Relieve pressure from coil by
depressing Schrader core at end of suction manifold stub out.
CAUTION
Dry nitrogen should always be supplied through the tubing while it is
being brazed, because the temperature required is high enough to
cause oxidation of the copper unless an inert atmosphere is provided.
The flow of dry nitrogen should continue until the joint has cooled.
Always use a pressure regulator and safety valve to insure that only
low pressure dry nitrogen is introduced into the tubing. Only a small
flow is necessary to displace air and prevent oxidation.
NOTICE
Avoid handling aluminum coil components after handling the copper
line set or other tubing without first cleaning hands.
!
!
!
!
NOTICE
Route the refrigerant lines to the coil in a manner that will not obstruct
service access to the coil, air handling system, furnace flue or filter.
IMPORTANT
The electronic expansion valve (EEV) in this unit is shipped in the
closed position to protect the valve during transportation. Prior to
brazing, line power must be applied to the air handler field wiring
terminals for 1 minute. The initial power causes the EEV to open
allowing nitrogen to flow through the system during the brazing pro-
cess.
NOTICE
If power cannot be applied to the EEV control board prior to brazing
refrigeration piping, a tool is available to manually operate the EEV.
An EEV manual operating tool can be purchased from Source 1 as
part number S1-02649686000. Six revolutions of the tool open the
valve fully.
NOTICE
All indoor coil connections are copper-to-copper and should be
brazed with a phosphorous-copper alloy material such as Silfos-5 or
equivalent. DO NOT use soft solder.