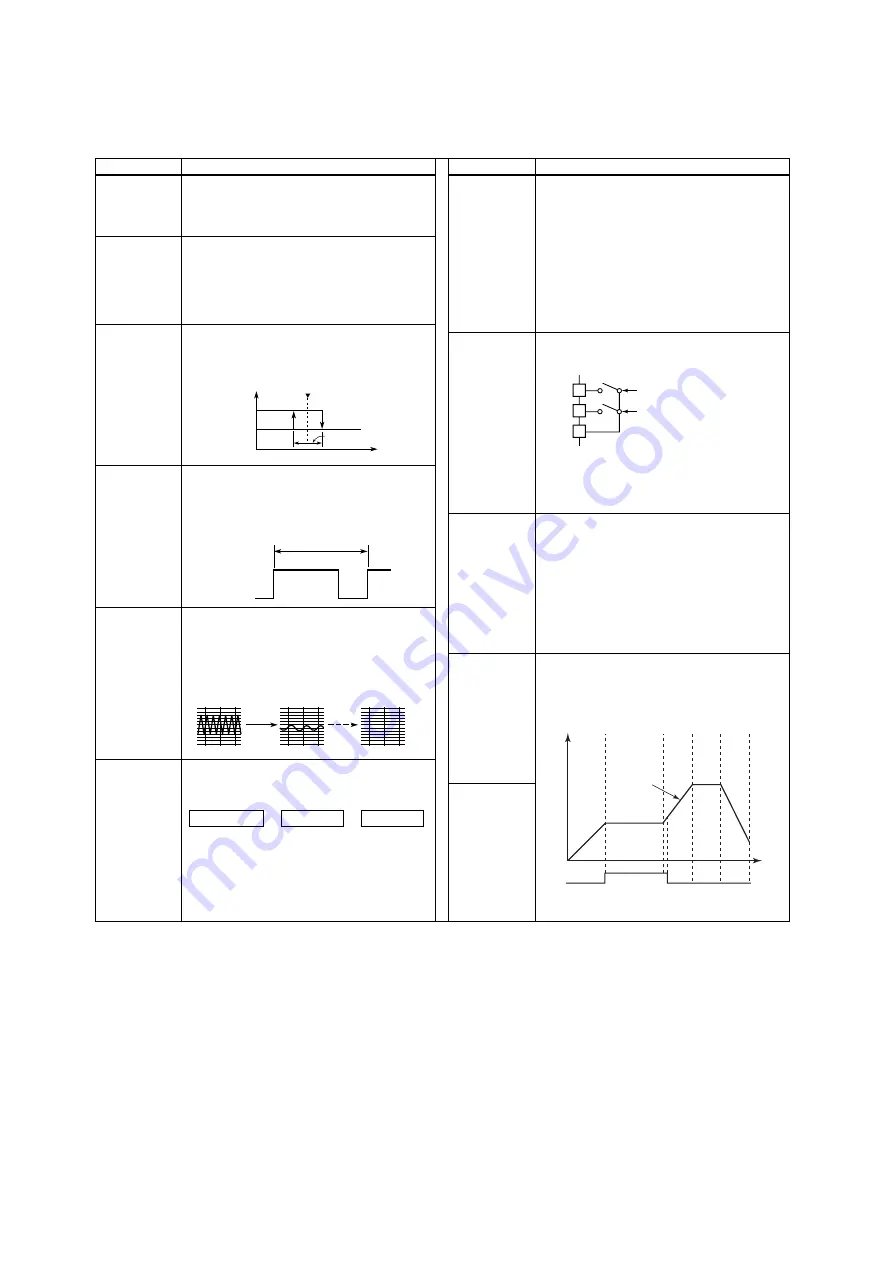
IM 5E1E70-01E
20
■
Description of Parameters
This section describes the parameter functions specific to the UP150 program controller.
(The functions described in other sections of this manual and the general functions are not discussed.)
Parameter
Function
Parameter
Function
Control mode
CTL
UP150 has two control mode.
Select one from the following:
a. PID control (PID)
b. On/off control
PV bias
BS
This function adds a bias value to the measured
input value, and the result is used for display and
control computation.
This function is useful for carrying out fine
adjustment when the PV value is within the
required accuracy but it differs from the value
obtained by other equipment.
Manual reset
MR
You can set this parameter only for control
without an integral action (when registered as
CTL=PID and I=0). The controller outputs the
manual reset (MR) value when PV=SP. For
example, if you set MR=50%, the controller
outputs (OUT) 50% when PV=SP.
Hysteresis for
on/off control
HYS
For on/off control (CTL=ONF), you can set a
hysteresis band around the on/off point (SP) to
prevent chattering.
Cycle time of
control output
CT
The cycle time is the period of on/off repetitions
of a relay or voltage pulse output in time
proportional PID control. The ratio of the ON time
to the cycle time is proportional to the control
output value.
Hysteresis for
alarm 1 and 2
HY1,
HY2
The alarms are output as relay outputs. Since a
relay has a limited life, excessive on/off actions
will shorten the life of the alarm. To prevent this,
you can set a hysteresis band to prevent excessive
on/off actions for both alarm 1 and alarm 2.
Digital input
selection
DIS
• When DIS=ON, Mode can be switched by only
digital input signal.
• In order to switch the Mode by key operation,
OFF must be set at DIS.
Note: UP150 can be switched into “RESET”
mode by key operation even if DIS=ON.
SUPER
function
selection
SC
The SUPER function is effective in the following cases:
a. An overshoot must be suppressed.
b. The rise-up time needs to be shortened.
c. The load often varies.
d. SP is changed frequently.
Note 1: The SUPER function will not work when
on/off control is selected, or I or D
constants is set at 0 in PID control.
Note 2: For some types of systems, the SUPER
function may not be so useful. If this is
the case, turn off the function.
Time event n*
on time
n*=1 or 2
EON1
EON2
Time event n*
off time
n*=1 or 2
EOF1
EOF2
The time event feature begins countdown when a
program starts running, and after the elapse of a
preset time, output an on-time event signal
(contact output ON) or off-time event signal
(contact output OFF).
On/off point (SP)
Hysteresis band
ON
OFF
Cycle time
t on
t off
Input
PV value inside the controller
measured input value
PV bias
+
=
Input filter
FL
This function should be used when the PV display
value may fluctuate greatly, for example, when the
measured input signal contains noise. The filter is
of the first-order lag type, and FB sets the time
constant. If a larger time constant is set, the filter
can remove more noise.
ON : HOLD , OFF : Cancel HOLD
COM
3
4
5
ON : RUN , OFF : RESET
SEG1
SEG2
SEG3 SEG4 SEG5
Time
Program
pattern
Time
event
ON time
OFF time
Time Event Diagram