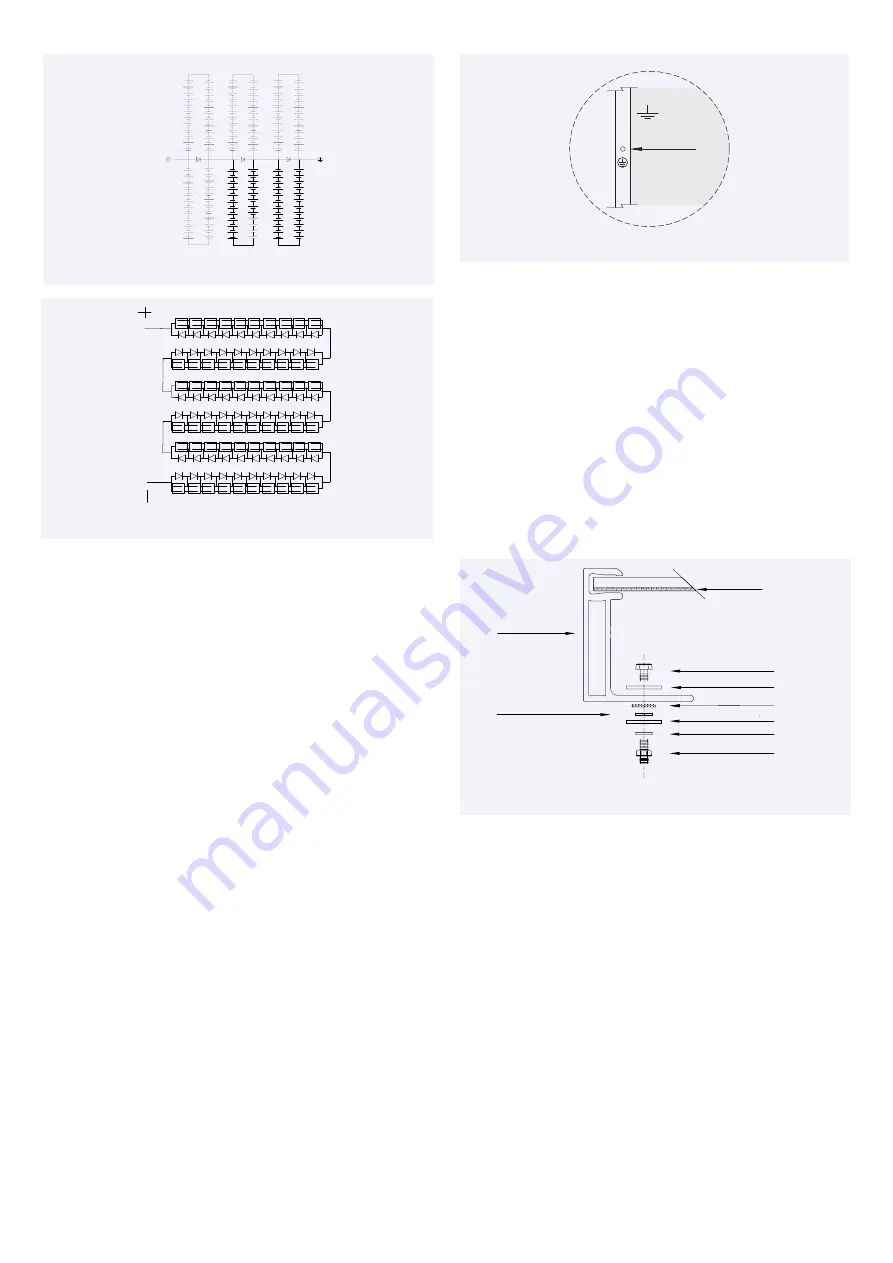
YINGLISOLAR.COM
© Yingli Energy Development Company Limited
GB Modules Installation and User Manual Page 4
Grounding Holes
Screw
Plain Washers
Spring Washers
Backing Nut
Piercing Washers
Plain Washers
Frame
Grounding Terminal
PV Laminate
Figure 7-1: Electrical circuitry of cell strings and bypass diodes
Figure 7-2: Electrical circuitry of cells and bypass diodes
In the event of a known or suspected diode failure, installers or maintenance
providers should contact the company the PV modules were purchased from.
Never attempt to open the junction box of a Yingli Solar PV module yourself.
PV Array Grounding
For optimal performance, Yingli Solar recommends that the negative pole of the
PV array be connected to ground.
Equipment Grounding
The frame of the PV module, as well as any exposed non-current-carrying metal
parts of fixed equipment that are able to become energized by the PV system,
must be connected to the equipment grounding conductor (EGC) in order to
prevent electrical shock. Even when applicable regulations, code requirements,
and standards do not require safety-related grounding, Yingli Solar recommends
grounding all PV
module frames in order to ensure the voltage between
electrically conductive equipment and earth ground is zero in all circumstances.
Proper equipment grounding is achieved by bonding all exposed non-current-
carrying metal equipment continuously to one another using an appropriately
sized EGC or racking system that can be used for integrated grounding (see
Option B in Grounding Methods below).
Yingli Solar PV modules employ a coated aluminum frame for corrosion
resistance. In order to properly ground the module frame, the coating must be
penetrated.
The potential for corrosion due to the electrochemical action between dissimilar
metals in contact is minimized if the electrochemical voltage potential between
the dissimilar metals is low. The grounding method must not result in the direct
contact of dissimilar metals with the aluminum frame of the PV module that
will result in galvanic corrosion. An addendum to UL Standard 1703 “Flat Plate
Photovoltaic Modules and Panels” recommends metal combinations not exceed
an electrochemical potential difference of 0.5 Volts.
The frame rails have pre-drilled holes marked with a grounding sign, as
illustrated in Figure 8. These holes should be used for grounding
purposes and
must not be used for installation the PV modules. Do not drill additional holes
into the frame rails.
Figure 8: Grounding hole detail
The following grounding methods are available:
Option A: Screw Assembly (see Figure 9)
1. The grounding screw must be installed on the designed grounding hole and
must be stainless steel screw.
2. The screw first passes through the stainless steel flat washers. The screw
rods pass through the grounding holes outwards, and then pass through
the stainless steel piercing washers, grounding terminal, stainless steel flat
washers, and stainless steel spring washers in turn, and finally fix them with
stainless steel backing nuts.
3. Tighten the backing nut to a torque of not less than 4 N∙m to ensure that the
backing nut can securely hold the screw.
4. Install piercing washers of appropriate size, and ensure that the protrusions of
the piercing washers reliably pierce the frame of the module.
Figure 9: Grounding screw assembly detail
Option B: Racking Manufacturer Integrated
Grounding Methods
Yingli Solar PV modules can be grounded by bonding PV modules to a grounded
racking system. Integrated grounding methods must be certified for grounding
PV modules and must be installed in accordance with the specified instructions
of their respective manufacturers.
Option C: Additional Third-party Grounding Devices
Yingli Solar PV modules can be grounded using third party grounding devices so
long as they are certified for grounding PV modules and the devices are installed
according to the manufacturer’s specified instructions.
M E C H A N I C A L I N S TA L L AT I O N
General
Yingli Solar PV Modules have been certified for a maximum static load on the
back of the module of up to 2400 Pa (i.e. wind load) and a maximum static load
on the front of the module of up to either 2400 Pa or 5400 Pa (i.e. wind and
Figure 7-1: Electrical circuitry of cells and bypass diodes