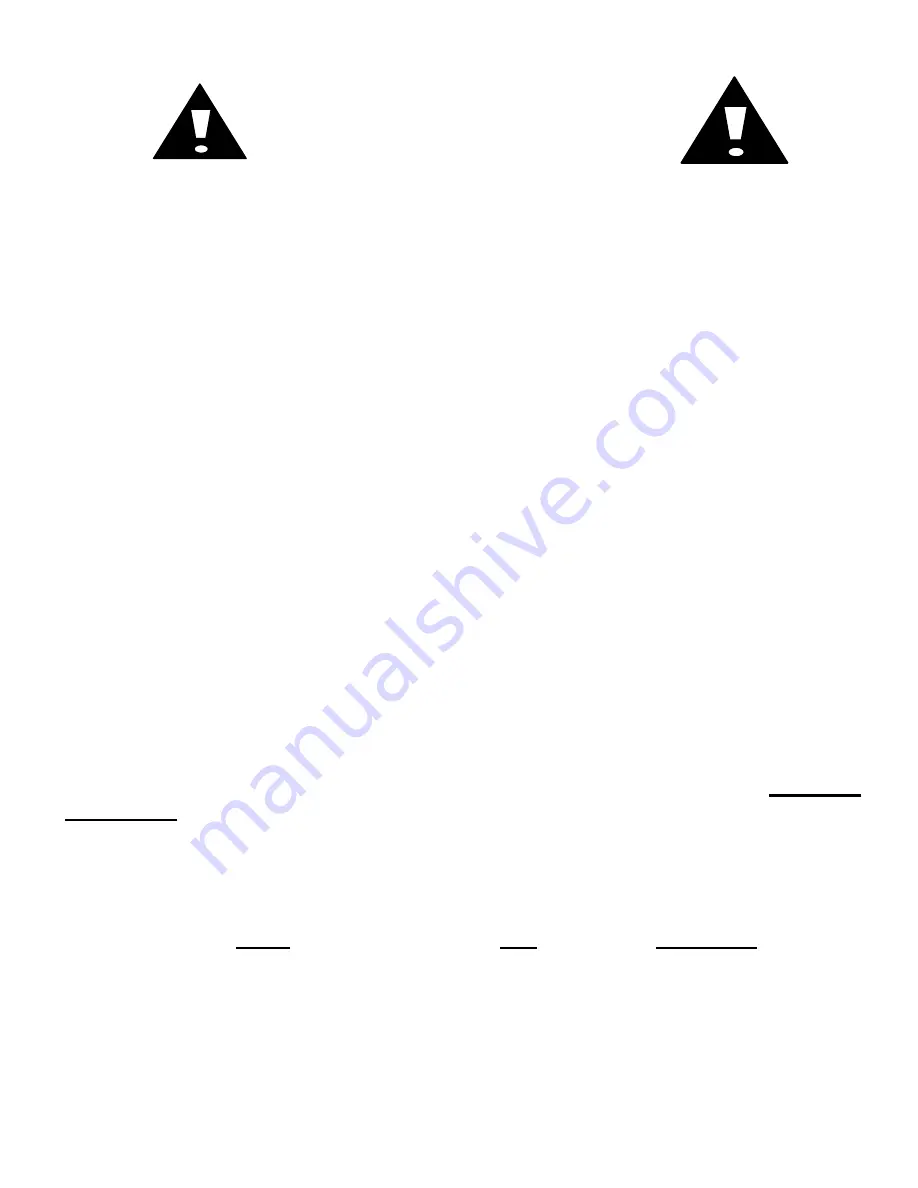
16
OPERATION PRECAUTIONS
STOP
Read this before using the Yetter product.
MACHINE OPERATION
Pneumatic System Check:
Make sure the toolbars compressor source is engaged. Allow the compressor to engage & complete 1 full
cycle before applying pressure to any circuit.
Pull the selector valve knob for the row cleaner circuit. Pull the regulator knob (unlock) for the row cleaner up
pressure circuit adjustment & turn the knob until ALL row cleaners move to the up position. Push the regulator
knob back in to lock in place. Pull the regulator knob for the row unit down force circuit adjustment & turn the
knob until the row unit down force gauge reads 50psi on the cab controller. Push the regulator knob back in to
lock in place. Pull the selector valve knob for the rolling basket circuit. Pull the regulator knob for the rolling
basket up pressure circuit adjustment & turn the knob until ALL rolling baskets move to the up position. Push the
regulator knob back in to lock in place. Exit the tractor cab inspecting the bulkhead connector at the hitch & all 3
of the circuits that have air pressure applied (row cleaner up, row unit down force, & rolling basket up). Check for
leaks at the tee fittings, air fittings at the cylinders/air bags, & each cylinder/air bag. Repair leaks as needed.
Once each of these 3 circuits is leak free, return to the tractor cab.
Push the selector valve for the row cleaner & rolling basket in (all rolling baskets and row cleaners should lower).
Pull the regulator knob for the row cleaner down pressure circuit adjustment & turn the knob until the row cleaner
gauge reads 50psi. Push the regulator knob back in to lock in place. Pull the regulator knob for the rolling basket
down pressure circuit adjustment & turn the knob until the rolling basket gauge reads 50psi. Push the regulator
knob back in to lock in place. Exit the tractor cab inspecting the bulkhead connector at the hitch & the down
pressure circuit for the row cleaner & rolling baskets. Lift each row cleaner & rolling basket to ensure down
pressure in each cylinder is present & equally applied to each row. Check for leaks at the tee fittings, air fittings
at the cylinders, & each cylinder. Once all circuits are leak free, return to the tractor cab & return all adjustable
circuits to 0psi.
Row Unit Check:
Inspect each individual strip freshener CC unit for loose or damaged hardware. Make sure all pivot points (row
unit parallel linkage, row cleaner, rolling basket) travel freely.
IMPORTANT: failure to properly set the frame height and levelness can result in
less than successful operation of the Yetter product and may result in damaged
equipment. All operators should read and thoroughly understand the
instructions given prior to using the Yetter product.
NOTE:
DO NOT
use this product if the toolbar is not adjusted properly!
Leveling the Toolbar:
With the frame lowered to proper operating height
(Usually 22”-26”)
Check to be sure the toolbar
is level side to side.
Check
when the toolbar is in the
field
and has been
fully loaded
with fertilizer,
etc. Also, a field check with a bubble level on the frame should be made of the hitch height to
ensure level operation front to back.
It is important for the toolbar to operate level laterally. Tire pressure must be maintained at
pressures specified by the manufacturer.
Field conditions change and will dictate toolbar frame heights. Lower the toolbar and pull forward to
allow units to get to desired depth & then recheck toolbar levelness.
Row unit parallel linkage should be parallel to the ground or slightly downhill from front to back.
Содержание CAB CONTROL STRIP FRESHENER 2984-050-R
Страница 18: ...18 OPERATION Cab Control Operation...
Страница 21: ...21 2984 050 STRIP FRESHENER CC PART IDENTIFICATION...
Страница 22: ...22 2984 050 STRIP FRESHENER CC PART IDENTIFICATION...
Страница 23: ...23 2984 132 PARALLEL LINKAGE ASSEMBLY PART IDENTIFICATION...
Страница 24: ...24 NARROW ROW CLEANER ASSEMBLY PART IDENTIFICATION...
Страница 25: ...25 WIDE ROW CLEANER ASSEMBLY PART IDENTIFICATION...
Страница 26: ...26 GAUGE WHEEL ASSEMBLY PARTS IDENTIFICATION SHARKTOOTH MOUNT ASSEMBLY PART IDENTIFICATION...
Страница 27: ...27 ROLLING BASKET ASSEMBLY PART IDENTIFICATION...
Страница 28: ...28 ROW CLEANER MOUNT ASSEMBLY PART IDENTIFICATION DEPTH STOP ADJUST ASSEMBLY PART IDENTIFICATION...
Страница 30: ...30 HUB ASSEMBLY PART IDENTIFICATION SCREW ADJUST ASSEMBLY PART IDENTIFICATION...
Страница 31: ...31 PARTS IDENTIFICATION...
Страница 32: ...32 PARTS IDENTIFICATION...
Страница 34: ...34 NOTES...
Страница 35: ...35...
Страница 36: ...36 2565 968 11 2019...