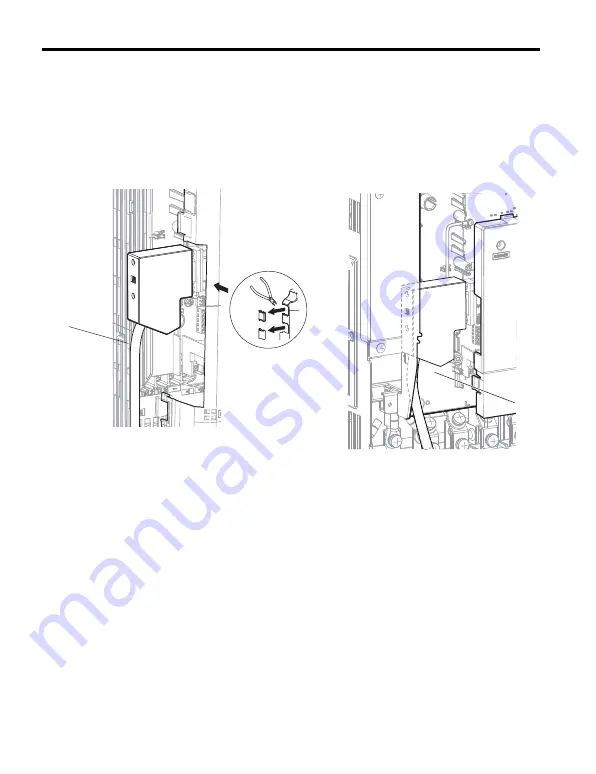
5 Installation Procedure
20
YASKAWA ELECTRIC
TOBP C730600 82B YASKAWA AC Drive Option SI-P3 Installation Manual
5.
Select the proper PROFIBUS-DP dedicated communication cable according to
.
Route the option wiring inside the enclosure as shown in
-B. Take proper
precautions so that the front covers will easily fit back onto the drive.
Users may also choose to route the option wiring through openings on the front
cover of some models. Remove the perforated tabs on the left side of the front cover
as shown in
-A to create the necessary openings on these models.
Refer to the Peripheral Devices & Options section of the drive instruction manual for
more information.
Figure 8
Figure 8 Wire Routing Examples
A – Route wires through the openings
provided on the left side of the
front cover.
<1> The drive will not meet Enclosed wall-mounted type (UL Type 1) requirements if wiring is exposed outside the
enclosure.
B – Use the open space provided
inside the drive to route option
wiring.
A
B