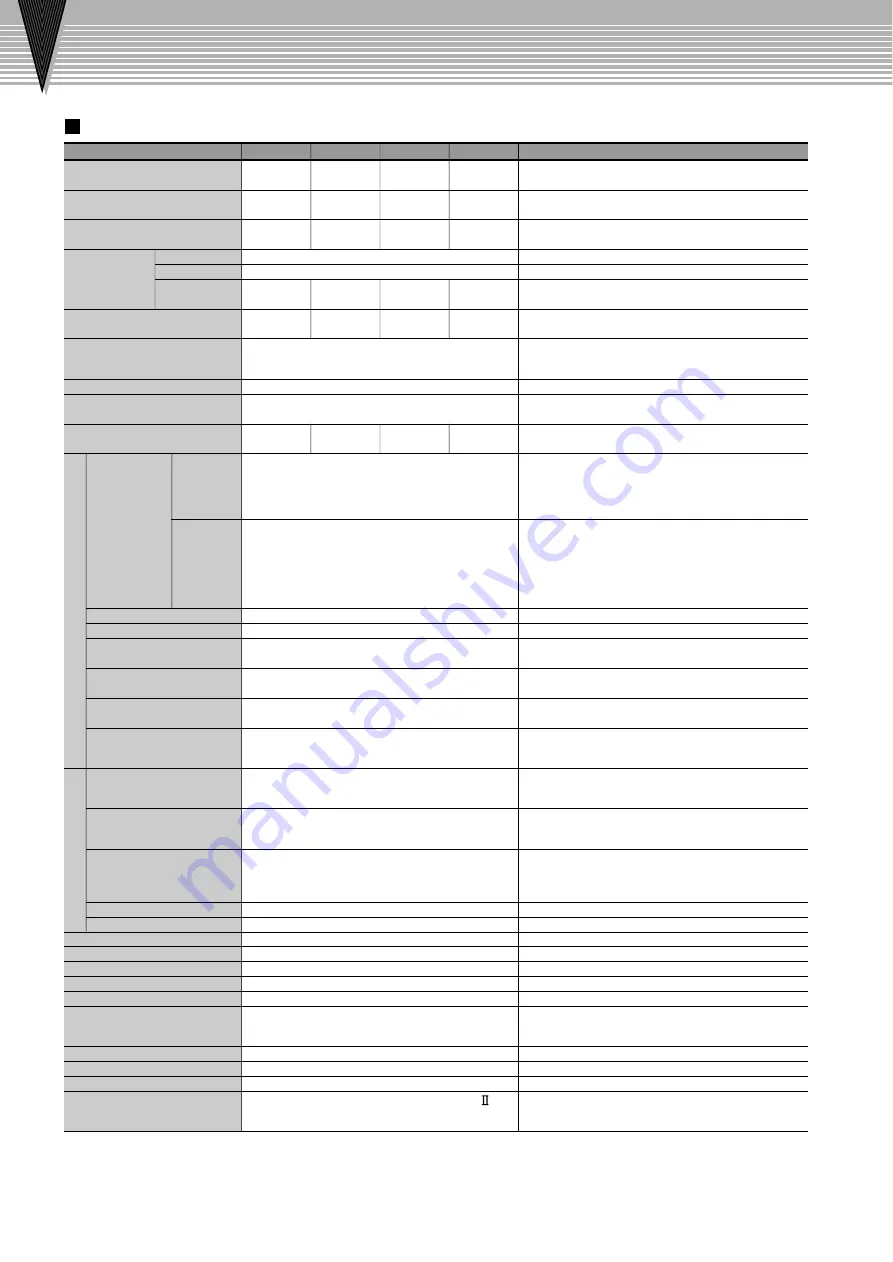
10
SERVOPACK model SJDE-
Description
01APA
02APA
04APA
08APA
Max. applicable servomotor
capacity [kW]
Cooling method
Operating temperature
Operating humidity
Storage temperature
Storage humidity
Installation site
Altitude
Vibration resistance
Shock resistance
Operating conditions
Power loss at rated output [W]
Input control method
Output control method
Voltage
Frequency
Capacity at rated
output [kVA]
Input power supply
(for main circuit
and control circuit)
Input signal
for reference
Pulse type
Pulse
resolution
Clear input signal
Servo ON input signal
Alarm output signal
Brake output signal
Origin output signal
Dynamic brake (DB)
LED display
Reference filter
Regenerative processing
0.1
0.2
0.4
0.75
0.40
0.75
1.2
2.2
14
16
24
35
0.6
×
10
-4
Allowable load inertia [kgm
2
]
*
1
3
×
10
-4
5
×
10
-4
10
×
10
-4
Select one of the following signals:
1. CCW + CW
2. Sign + pulse train
3. CCW + CW (logic reversal)
4. Sign + pulse train (logic reversal)
Capacitor-input type, single-phase full-wave
rectification with resistance to prevent inrush
currents.
PWM control, sine wave power driven system
Feedback
Analog output encoder
Select one of the following signals:
1. 1000 pulses/rev
(Open collector/line driver) 75 kpps max.
2. 2500 pulses/rev
(Open collector/line driver) 187.5 kpps max.
3. 5000 pulses/rev (Line driver) 375 kpps max.
4. 10000 pulses/rev (Line driver) 750 kpps max.
Single-phase 200 V to 230 VAC, +10% to –15%
50/60Hz
±
5%
Clears the positioning error when turned ON.
Turns the servomotor on or off.
OFF if an alarm occurs.
Note: OFF for 2s when power is turned ON.
External signal to control brakes.
Turn ON to release the brake.
Positioning
completed output signal
ON if the current position is equal to the reference
position
±
10 pulses.
ON if the motor is at the origin. (Width: 1/500 rev)
Note: Use the pulse edge that changes the signal from OFF
to ON.
Optional
(If the regenerated energy is too large, install a
regenerative unit.)
5 (PWR, REF, AL1, AL2, AL3)
Select one of eight levels with FIL switch.
Forced cooling (built-in fan)
0˚C to +55˚C
90% RH or less (with no condensation)
–20˚C to +70˚C
90% RH or less (with no condensation)
Operated at main power OFF, servo alarm, servo
OFF.
(OFF after motor stops; ON if the motor power is off.)
• Free of corrosive gases
• Free of dust and iron powder
• Clean and dry
1000 m or below
4.9m/s
2
19.6m/s
2
Designated
pulse type
and pulse
resolution
with PULSE
switch.
Motor capacity that the SERVOPACK can drive.
Continuous output current
[Arms]
0.84
1.1
2.0
3.7
Current that the SERVOPACK can output continuously.
Instantaneous max.
output current [Arms]
2.5
3.3
6.0
11.1
Maximum current that the SERVOPACK can output
instantaneously.
Power supply capacity required to operate a motor at
the rated output.
Electric power emitted as heat from the SERVOPACK while
operating the motor at the rated torque and rated speed.
Type of pulse train signal to drive motor, input into the
SERVOPACK.
For CCW+CW, input both forward and reverse
rotation pulse trains.
Number of reference pulses required to rotate the
motor one turn
Only one point of origin per rotation
Method that stops the motor by short-circuiting
the internal circuit of the SERVOPACK.
Function to consume rotational power generated when
the motor is rotated by external force. This function is
required for a high load moment of inertia.
Protection
*
2
Speed errors, overload, encoder errors, voltage
errors, overcurrents, disablement of the built-in
cooling fan, system errors.
Note: No built-in circuit for ground protection.
–
–
–
–
–
–
–
–
–
–
–
–
–
–
–
–
–
–
–
–
–
–
SERVOPACKs
SERVOPACKs
I/O Signals
Built-in functions
Ratings and Specifications
*
1: Be sure to use the motor with in the allowable load inertia moment.
The operation of the motor will become unstable if the allowable load Inertia moment is exceeded.
*
2: The ground protection circuit is designed for ground fault inside the motor windings while the motor is running.
Therefore, it may not protect the system under the following conditions.
• A low-resistance ground fault occurs in the main circuit cable or in the connector of the cable for the servomotor.
• The power supply is turned ON during a ground fault.
To configure a safer system, install an earth leakage breaker to protect against both overloads and shortcircuits, or install an earth
leakage breaker for ground protection and a molded-case circuit breaker.
Installation category (overvoltage category):
Pollution degree: 2
Protection class: IP1X (EN50178)
Speed or position detector fixed on the motor shaft
opposite the load side.
Maximum allowable moment of inertia converted into
the moment of inertia at the motor shaft of the machine.