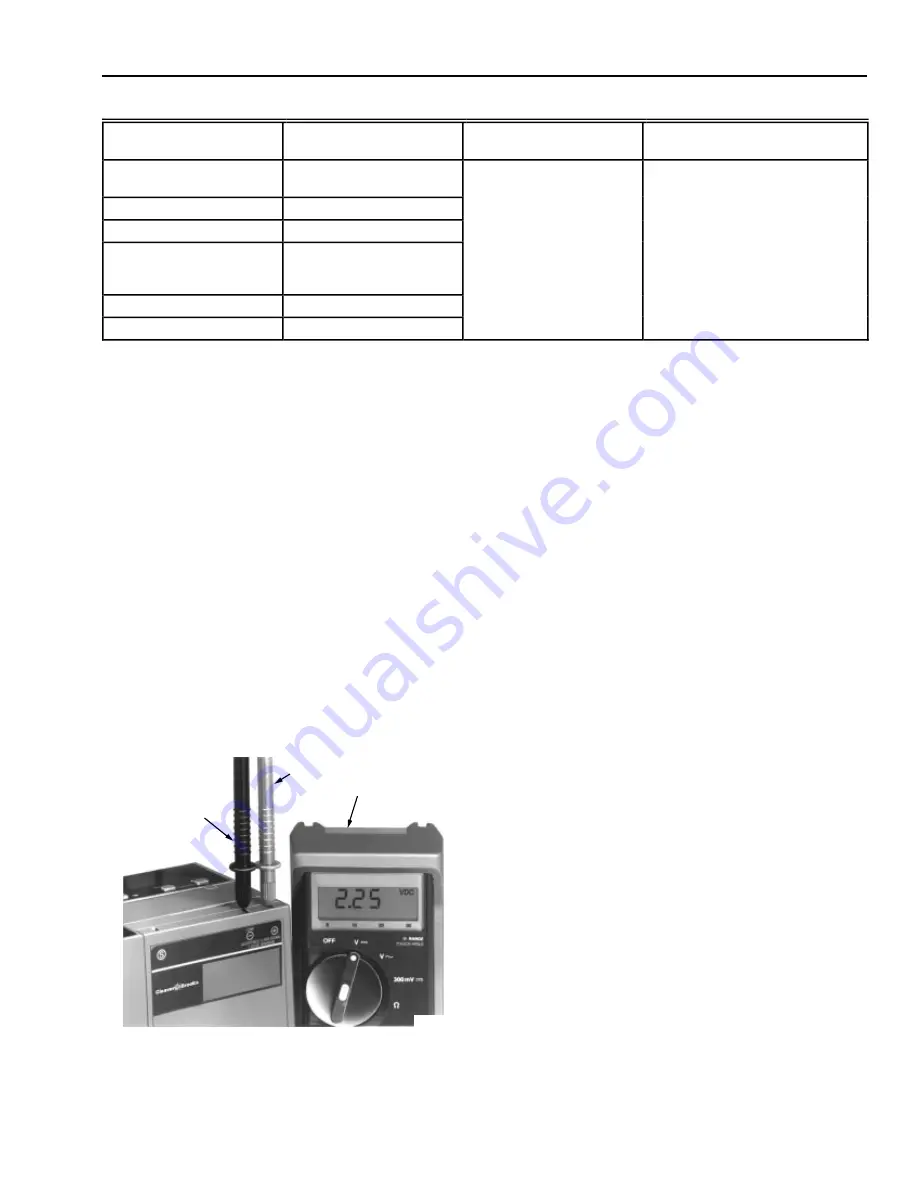
7800 SERIES EC7890A,B/RM7890A,B RELAY MODULE
65-0204–1
21
Table 5. Flame Signal (See Fig. 18).
Flame Detector
Flame Signal Amplifier
Minimum Acceptable
Steady dc Voltage
a
Maximum Expected
dc Voltage
Flame Rod Photocell
C7012A,C
R7847A,B
b
1.25 Vdc
5.0 Vdc at the Keyboard
Display Module.
C7012E,F
R7847C
c
or
C7015A
R7848A,B
b
5.0 Vdc at a 1M ohm/voltmeter.
C7027A
C7035A
C7044A
R7849A,B
b
C7061A
R7861
d
C7076A,D
R7886A
e
a
This minimum or a stronger signal should easily be obtained if the detector is correctly installed and positioned to properly
sense the flame. This voltage must be obtained before completing checkout.
b
The flame amplifiers are Ampli-Check® type.
c
The flame signal amplifier circuitry is tested one-half second every five seconds during burner operation and shuts down the
burner if the amplifier fails (all installations). R7847C is for use with RM7890A,B only.
d
Requires use of separate step-down transformer. See Fig. 13.
e
R7886A is for use with RM7890A,B only.
Flame Signal Measurement
Measure the flame signal at the appropriate times defined in
the following checkout tests. Read the flame signal Vdc at the
flame amplifier test jacks + and - (Com).
1
Use a 1M ohm/volt meter with a 0 to 10 Vdc capability.
2
Set the 1M ohm/volt meter to the 0 to 10 Vdc range.
3
Insert the positive (red) probe into the + jack of the
flame amplifier. Insert the negative (black) probe into
the - (Com) jack of the flame amplifier (see Fig. 18).
4
Allow a few seconds for the meter reading to stabilize.
5
If using Ampli-Check™ or shutter check amplifiers, read
the average stable voltage, disregarding the peaks and
valleys caused by the self-checking operation.
6
The meter reading must be as specified in Table 5 after
all tests are completed and all adjustments are made.
As an option, the flame signal can be checked by using the
optional Keyboard Display Module.
If the signal is unstable or less than the minimum acceptable
voltage, check the flame detector installation and circuitry.
1
Check the supply voltages at terminals 3 (L1) and L2
(N). Make sure the master switch is closed,
connections are correct, and the power supply is of the
correct voltage, frequency and is sinusoidal.
2
Check the detector wiring for defects including:
•
Deteriorated wire.
•
Incorrect connections.
•
Leakage paths caused by moisture, soot or
accumulated dirt.
•
Open circuits.
•
Short circuits.
•
Wrong type of wire.
3
For a flame rod, make sure:
•
Flame rod is properly located in the flame.
•
Ground area is large enough.
•
Temperature at the flame rod insulator is no
greater than 500
°
F (260
°
C).
4
For all optical detectors, clean the detector viewing
window and inside of the sight pipe as applicable.
5
With the burner running, check the temperature at the
detector. If it exceeds the detector maximum rated
temperature:
•
Add a heat block to stop conducted heat traveling
up the sight pipe.
•
Add a shield or screen to reflect radiated heat.
•
Add cooling (refer to sight pipe ventilation in the
detector Instructions).
6
Make sure that the flame adjustment is not too lean.
7
Make sure that the detector is properly sighting
the flame.
8
If necessary, resight or reposition the detector.
Initial Proved Pilot Lightoff Check
Perform this check on all installations that use a pilot. It
should immediately follow the preliminary inspection.
Fig. 18. Flame signal measurement.
NEGATIVE (-)
METER LEAD
POSITIVE (+)
METER LEAD
ONE
MEGOHM/VOLT
METER
M7383