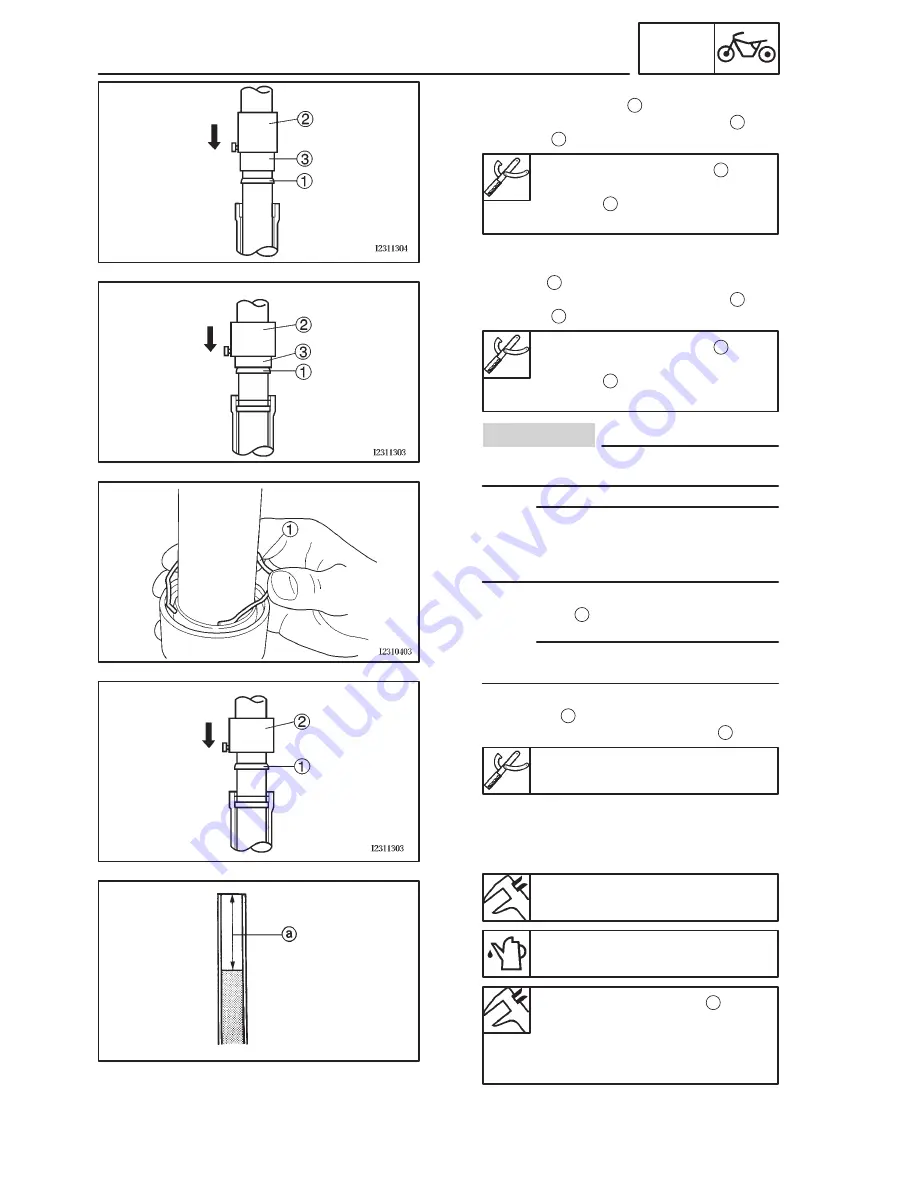
7-46
FRONT FORK
CHAS
CAUTION:
NOTE:
NOTE:
4. Install:
outer tube bushing
1
(with the fork seal driver weight
2
and
adapter
3
)
Fork seal driver weight
2
90890-01367
Adapter
3
90890-01381
5. Install:
washer
oil seal
1
(with the fork seal driver weight
2
and
adapter
3
)
Fork seal driver weight
2
90890-01367
Adapter
3
90890-01381
Make sure that the numbered side of the
oil seal, faces up.
Before installing the oil seal, apply lithium
soap base grease onto its lips.
Apply fork oil onto the outer surface of the
inner tube.
6. Install:
oil seal clip
1
Adjust the oil seal clip so that it fits into the
outer tube’s groove.
7. Install:
dust seal
1
(with the fork seal driver weight)
1
Fork seal driver weight
90890-01367
8. Fill:
front fork leg
(with the specified amount of the recom-
mended fork oil)
Quantity (each front fork leg)
0.475 L
Yamaha fork and shock oil
10 W or equivalent.
Front fork leg oil level
a
(from
the top of the inner tube, with
the inner tube fully compressed
and without the fork spring)
121 mm
Содержание FZS600'98
Страница 1: ......
Страница 2: ......
Страница 8: ......
Страница 9: ...GEN INFO 1 ...
Страница 11: ...GEN INFO ...
Страница 20: ...SPEC 2 ...
Страница 22: ...SPEC ...
Страница 45: ...2 23 1 2 3 4 LUBRICATION DIAGRAMS SPEC 1 Main axle 2 Drive axle 3 Camshaft 4 Oil delivery pipe ...
Страница 46: ...2 24 1 2 LUBRICATION DIAGRAMS SPEC 1 Camshaft 2 Crankshaft ...
Страница 54: ...SPEC ...
Страница 55: ...CHK ADJ 3 ...
Страница 57: ...CHK ADJ ...
Страница 109: ...CHK ADJ ...
Страница 110: ...ENG 4 ...
Страница 189: ...COOL 5 ...
Страница 191: ...COOL ...
Страница 202: ...CARB 6 ...
Страница 204: ...CARB ...
Страница 216: ...6 12 CARB ...
Страница 217: ...CHAS 7 ...
Страница 288: ...ELEC 8 ...
Страница 290: ...ELEC ...
Страница 292: ...8 2 CIRCUIT DIAGRAM ELEC CIRCUIT DIAGRAM ...
Страница 326: ...8 36 SIGNAL SYSTEM ELEC EB806000 SIGNAL SYSTEM CIRCUIT DIAGRAM ...
Страница 355: ...TRBL SHTG 9 ...
Страница 357: ...TRBL SHTG ...
Страница 363: ...TRBL SHTG ...