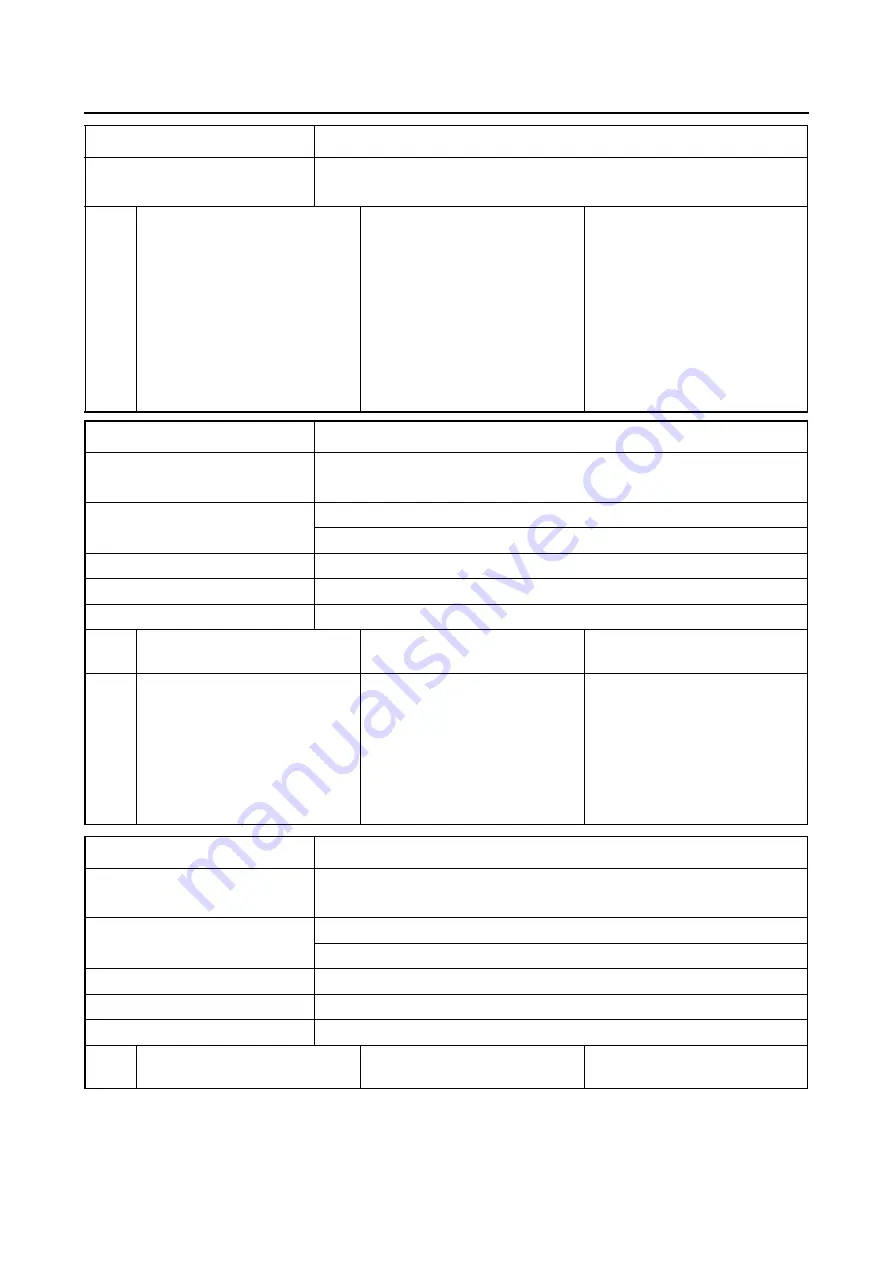
FUEL INJECTION SYSTEM
8-84
9
Delete the fault code.
Turn the main switch to “ON”,
and then rotate the front
wheel by hand.
Start the engine, and input
the vehicle speed signals by
operating the vehicle at 20 to
30 km/h (19 mph).
The fault code can also be
deleted by activating the di-
agnostic mode and selecting
diagnostic code number “63”.
Fault code No.
89 (Yamaha diagnostic tool)
Item
Multi-function meter: signals cannot be transmitted between
the ECU and the multi-function meter.
Fail-safe system
Able to start engine
Able to drive vehicle
Diagnostic code No.
—
Meter display
—
Procedure
—
Item
Probable cause of mal-
function and check
Maintenance job
Confirmation of service
completion
1
Locate the malfunction.
• “Err” is displayed
→
Exe-
cute the diagnostic mode.
(Code No. “Err”)
• “Err” is not displayed
→
Re-
fer to “Abnormal meter as-
sembly communication” in
the troubleshooting when
“Err” is displayed.
Fault code No.
Err (multi-function meter center display)
Item
Abnormal meter assembly communication (meter assembly
cannot receive CAN communication data).
Fail-safe system
Able to start engine
Able to drive vehicle
Diagnostic code No.
—
Meter display
—
Procedure
—
Item
Probable cause of mal-
function and check
Maintenance job
Confirmation of service
completion
Fault code No.
69
Item
Front wheel sensor: no normal signals are received from the
front wheel sensor.
Содержание FJR 1300 AE 2014
Страница 1: ...2014 SERVICE MANUAL FJR1300AE FJR1300AEE 2PD 28197 E0 ...
Страница 6: ......
Страница 8: ......
Страница 104: ...LUBRICATION SYSTEM CHART AND DIAGRAMS 2 33 EAS20410 LUBRICATION DIAGRAMS 5 6 7 1 2 3 4 ...
Страница 106: ...LUBRICATION SYSTEM CHART AND DIAGRAMS 2 35 1 3 2 ...
Страница 107: ...LUBRICATION SYSTEM CHART AND DIAGRAMS 2 36 1 Main axle 2 Drive axle 3 Oil delivery pipe 1 ...
Страница 108: ...LUBRICATION SYSTEM CHART AND DIAGRAMS 2 37 6 5 4 3 2 1 ...
Страница 110: ...LUBRICATION SYSTEM CHART AND DIAGRAMS 2 39 1 2 3 4 5 6 7 8 9 ...
Страница 112: ...LUBRICATION SYSTEM CHART AND DIAGRAMS 2 41 4 5 3 2 1 9 8 6 7 ...
Страница 114: ...COOLING SYSTEM DIAGRAMS 2 43 EAS20420 COOLING SYSTEM DIAGRAMS 3 13 4 5 6 7 7 7 8 1 2 10 9 14 15 16 17 11 12 3 ...
Страница 116: ...COOLING SYSTEM DIAGRAMS 2 45 7 1 2 3 4 5 5 8 9 6 8 9 10 11 12 ...
Страница 122: ...CABLE ROUTING 2 51 Rear brake hose right side view 4 5 6 7 8 9 10 11 1 12 13 14 15 2 3 16 1 A B C F E D ...
Страница 124: ...CABLE ROUTING 2 53 Horn and radiator left side view A B 1 1 2 3 4 5 5 6 C 7 7 8 ...
Страница 132: ...CABLE ROUTING 2 61 Rear fender top view 7 D E 6 D 5 C 1 2 3 4 A B 8 3 F ...
Страница 138: ...CABLE ROUTING 2 67 ...
Страница 141: ......
Страница 300: ...SHAFT DRIVE 4 123 ...
Страница 322: ...CAMSHAFTS 5 19 11 Install Cylinder head cover plate 1 TIP Be sure the UP mark a is facing up New 2 2 a 1 3 a a 1 ...
Страница 361: ...SHIFT SHAFT 5 58 c Tighten both locknuts to specification T R Shift rod locknut 7 Nm 0 7 m kg 5 1 ft lb 1 2 c d a b ...
Страница 378: ...MIDDLE GEAR 5 75 Middle driven pinion gear shim Thickness mm 0 10 0 15 0 20 0 30 0 40 0 50 ...
Страница 414: ...BALANCERS 5 111 ...
Страница 430: ...WATER PUMP 6 15 ...
Страница 444: ...AIR INDUCTION SYSTEM 7 13 EAS27040 AIR INDUCTION SYSTEM 1 2 3 5 6 7 8 1 1 2 1 1 3 6 7 8 2 2 3 5 4 ...
Страница 457: ...IGNITION SYSTEM 8 6 ...
Страница 463: ...ELECTRIC STARTING SYSTEM 8 12 ...
Страница 467: ...CHARGING SYSTEM 8 16 ...
Страница 479: ...SIGNALING SYSTEM 8 28 ...
Страница 539: ...FUEL INJECTION SYSTEM 8 88 ...
Страница 557: ...CRUISE CONTROL SYSTEM 8 106 ...
Страница 569: ...ACCESSORY BOX SYSTEM 8 118 ...
Страница 579: ...IMMOBILIZER SYSTEM 8 128 ...
Страница 583: ...ABS ANTI LOCK BRAKE SYSTEM 8 132 ...
Страница 640: ...ELECTRICAL COMPONENTS 8 189 9 1 3 2 18 21 20 19 11 12 13 14 15 16 17 4 5 10 6 8 7 ...
Страница 690: ......
Страница 691: ......
Страница 692: ......