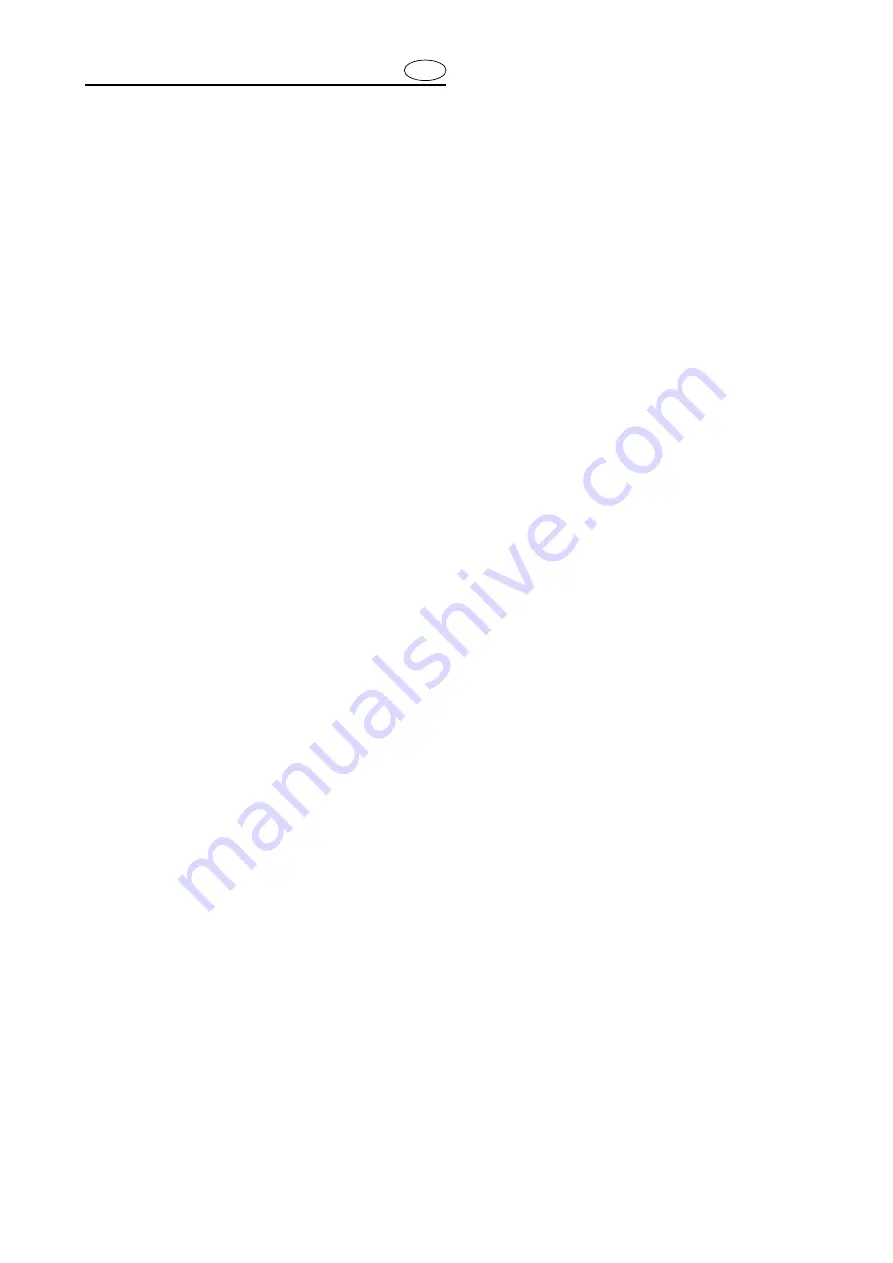
English
INTRODUCTION
All users must read these operating instructions carefully prior to the initial
operation. These instructions are intended to acquaint the user with the
product and enable him to use it to the full extent of its intended capabili-
ties. The operating instructions contain important information on how to
handle the product in a safe, correct and economic way. Acting in accord-
ance with these instructions helps to avoid dangers, reduce repair cost and
down time and to increase the reliability and lifetime of the product. Apart
from the operating instructions and the accident prevention act valid for the
respective country and area where the product is used, also the commonly
accepted regulations for safe and professional work must be adhered to.
CORRECT OPERATION
- The unit has been designed for lifting, lowering and transportation of loads.
- The capacity indicated on the product is the maximum safe working load
(W.L.L.) that may be lifted.
- The unit may only be operated within the beam range indicated on the
name plate (Tab. 1).
- Do not lift or transport loads while personnel are in the danger zone.
- Do not allow personnel to pass under a suspended load.
- After lifting, a load must not be left unattended for long periods.
- Start moving the load only after it has been attached correctly and all
personnel are clear of the danger zone.
- The operator must ensure that the load is attached in a manner that does
not expose himself or other personnel to danger by the hoist, chain(s) or
the load.
- The hoists can be operated in ambient temperatures between -10
°
C and
+50
°
C. Consult the manufacturer in case of extreme working conditions.
Note:
At ambient temperatures below 0
°
C the brake should be checked
for freezing.
- The accident prevention act and/or safety regulations of the respective
country for using manual hoists must be strictly adhered to.
- lf defects are found stop using the product immediately.
- The selection and calculation of suitable carrying beams is the responsi-
bility of the user.
INCORRECT OPERATION
- Do not exceed the rated capacity of the trolley hoist.
- Do not use the trolley hoist for transportation of people (Fig. 1).
- Welding on hook and load chain is strictly forbidden. The load chain must
never be used as ground connection during welding (Fig. 2).
- Welding on trolley is strictly forbidden (Fig. 3).
- Avoid side pull, i. e. side load on housing or bottom block (Fig. 4).
- The load chain must not be used for lashing purposes (sling chain)
(Fig. 5).
- Do not knot or shorten the load chain by using bolts/screws/screwdrivers
or other devices (Fig. 6). Do not repair load chains installed in the hoist.
- Do not remove the safety latch from the top or bottom hooks (Fig. 7).
- Never attach the load on the tip of the hook (Fig. 8).
- Do not use the chain stop as an operational limit device (Fig. 11).
- Do not allow the trolley to be dropped or thrown, always place it properly
on the ground.
- Enlarging the clearances, e. g. to enable the trolley to negotiate larger
curves, is forbidden.
INSTALLING THE TROLLEY
LHP/G (Fig. 4 and Fig. 5)
The units are delivered pre-assembled and are built to fit beam range A or
B which is given on the name plate (Tab. 1). Prior to installation make sure
that the flange width is within the limits indicated.
1.
Unscrew the locking nuts (10) and hex. nuts (19) from the suspension
bolts and remove both side plates from the trolley.
2.
Measure the width "b" of the beam flange.
3.
Adjustment/pre-adjustment of dimension "B" between the outer flang-
es of the round nuts (16) on the free threaded ends of the suspension
bolts (20).
GB
Make sure that the four drill holes in the round nuts face away from the
suspension bar. Dimension "B" between the outer flanges of the round
nuts on the suspension bars has to be determined in a way that it
corresponds to flange width "b" plus 4 mm lateral play (dim. A = 2
mm on either side). Ensure that the suspension bar (14) is centered
between the round nuts (16).
4.
Assembly of one side plate:
The roll pins (17) fitted to the side plate (12) must be seated in one of
the four drill holes of the round nuts (16). If necessary the position of
the round nuts must be slightly re-adjusted.
5.
Positioning of the washer (18) and tightening of the hex. nuts (19).
Finally screw on the locking nuts (10) by hand and tighten by
1
/
4
to
1
/
2
rotation.
Attention: The locking nuts (10) must always be fitted !
6.
Pre-assembly of the second side plate onto the suspension bolts:
Washers (8), hex. nuts (9) and locking nuts (10) can be screwed on
loose to facilitate the asssembly to the beam flange.
7.
Positioning of the complete pre-assembled unit on the beam flange.
Attention:
For Model LHG please pay attention to which side of the
beam the operator will work and position the trolley accordingly.
8.
Assembly of the second side plate:
The roll pins (17) fitted to the side plate must be seated in one of the
four drill holes of the round nuts (16). If necessary the position of the
round nuts must be slightly re-adjusted.
9.
Tightening of the hex. nuts (19) on the second side plate:
Finally screw on the locking nuts (10) by hand and tighten by
1
/
4
to
1
/
2
rotation.
Attention:
The locking nuts (10) must always be fitted.
10. In order to adjust the support roller (21) to the beam, loosen the screw
(22) and position the support roller directly underneath the beam by
turning the eccentric bolt. Now tighten the screw (22) again.
11. Finally control operation of the trolley hoist by rolling it along the beam
with load and check the following:
- The preset lateral play (dim. "A" = 2 mm on either side) between the
flange of the trolley wheel and the outer edge of the beam flange must
be maintained.
- The suspension bar and hoist must be positionened centrally under
the beam flange.
- Tighten all four hex. nuts (19) and locking nuts (10).
- The trolley may not tilt under load.
Attention:
Under no circumstances may a trolley be fitted to a beam which
exceeds the maximum allowable width.
INSPECTION PRIOR TO INITIAL OPERATION
Each unit must be inspected prior to initial operation by a competent per-
son. The inspection is visual and functional. This inspection shall establish
that the unit is safe and has not been damaged by incorrect transport or
storage.
Ensure that the rollpins are correctly fitted to the suspension bar. The side
plates must be parallel to each other and all troilley wheels must be in
contact with the beam.
Inspections should be made by a representative of the manufacturer or the
supplier although the company can assign its own suitably trained person-
nel.
INSPECTION BEFORE STARTING WORK
Every time before starting work, inspect the trolley, hoist and all load bear-
ing constructions for visual defects, e. g. deformations, damage, cracks,
wear or corrosion marks.
Furthermore check that hoist and load are correctly attached. The selection
and calculation of the proper beam construction are the responsibility of
the user.
Especially check the correct assembly of the suspension bolts and also the
adjustment of the trolley on the beam.
Load chain inspection
Inspect the load chain for sufficient lubrication and visually check for external
defects, deformations, superficial cracks, wear or corrosion marks.
4