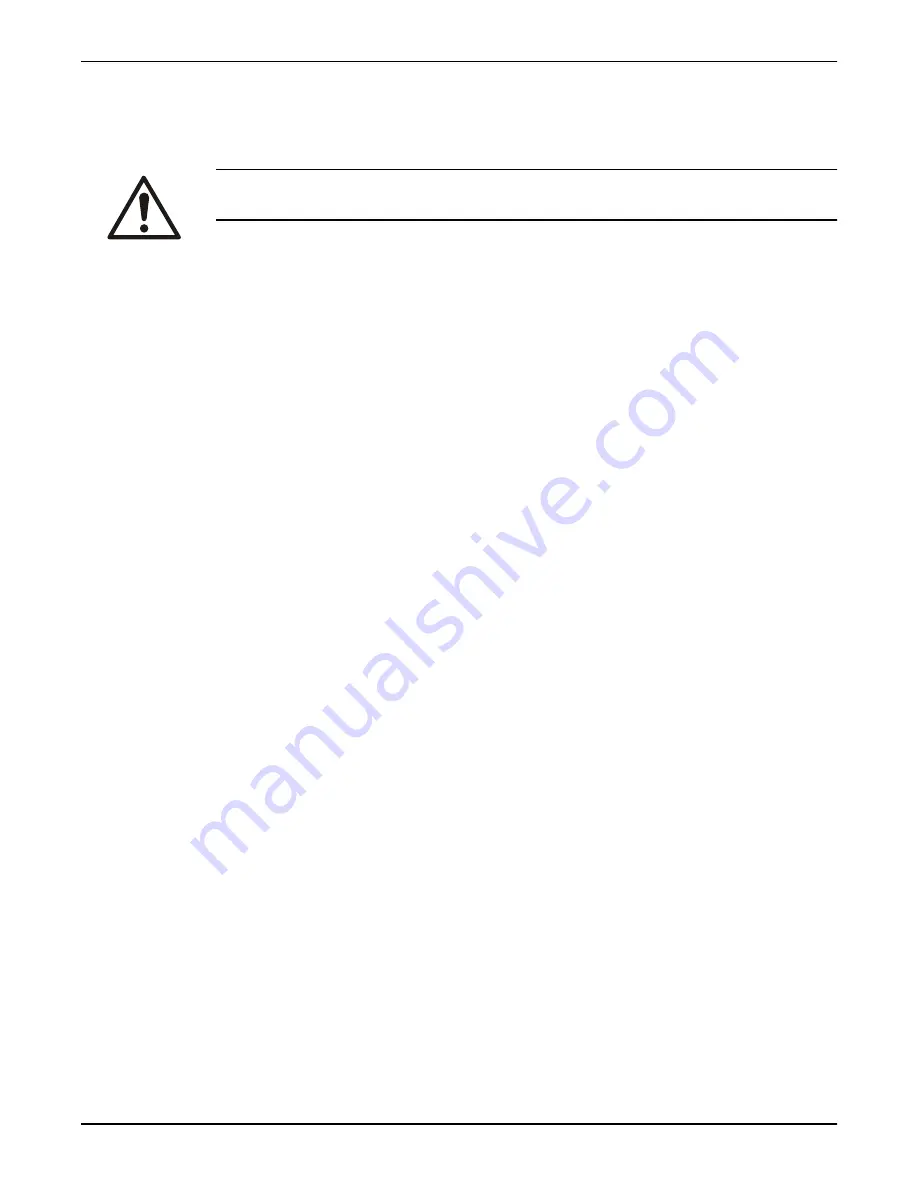
Replace the impeller
Remove the impeller
WARNING:
A worn impeller and/or pump housing can have very sharp edges. Wear protective gloves.
1. Lay the pump on its side.
2. Remove the nuts on the strainer bottom, and pull it off.
3. Remove the strainer.
4. Remove the nuts.
5. Remove the sleeves and the suction cover.
6. Remove the impeller nut.
7. Pull off the impeller.
Use an impeller puller or pry off carefully with two strong screwdrivers or bars.
Install the impeller
1. Prepare the shaft:
a) Polish off any flaws with a fine emery cloth.
The end of the shaft must be clean and free from burrs.
b) Grease the end of the shaft.
c) Insert the key in the keyway of the shaft.
d) Fit an appropriate number of adjusting washers on the shaft.
2. Fit the impeller onto the shaft.
Check that the impeller is firmly seated.
3. Tighten the impeller nut.
The impeller clearance should be minimal when the impeller is tightened. Use the
adjusting washers to adjust the clearance.
4. Check that the impeller can rotate easily.
Adjust the impeller
In order for the pump to perform at maximum capacity, the impeller must be adjusted
regularly. The impeller clearance should be minimal when the impeller is tightened. Use
the adjusting washers to adjust the clearance.
1. Fit an appropriate number of adjusting washers on the studs.
2. Press the suction cover against the impeller.
3. Place sleeves and nuts on the studs. Tighten the nuts evenly all around.
4. Check that the impeller can rotate easily.
5. Install the strainer.
6. Install the strainer bottom. Tighten the nuts evenly all around.
Maintenance
30
Flygt 3060 Installation, Operation, and Maintenance Manual
Содержание Flygt 3060
Страница 1: ...Flygt 3060 Installation Operation and Maintenance Manual ...
Страница 2: ......
Страница 41: ...Figure 7 MT CP DP Technical Reference Flygt 3060 Installation Operation and Maintenance Manual 39 ...
Страница 42: ...Figure 8 HT CS Technical Reference 40 Flygt 3060 Installation Operation and Maintenance Manual ...
Страница 43: ...Figure 9 MT CS DS Technical Reference Flygt 3060 Installation Operation and Maintenance Manual 41 ...
Страница 48: ......
Страница 49: ......