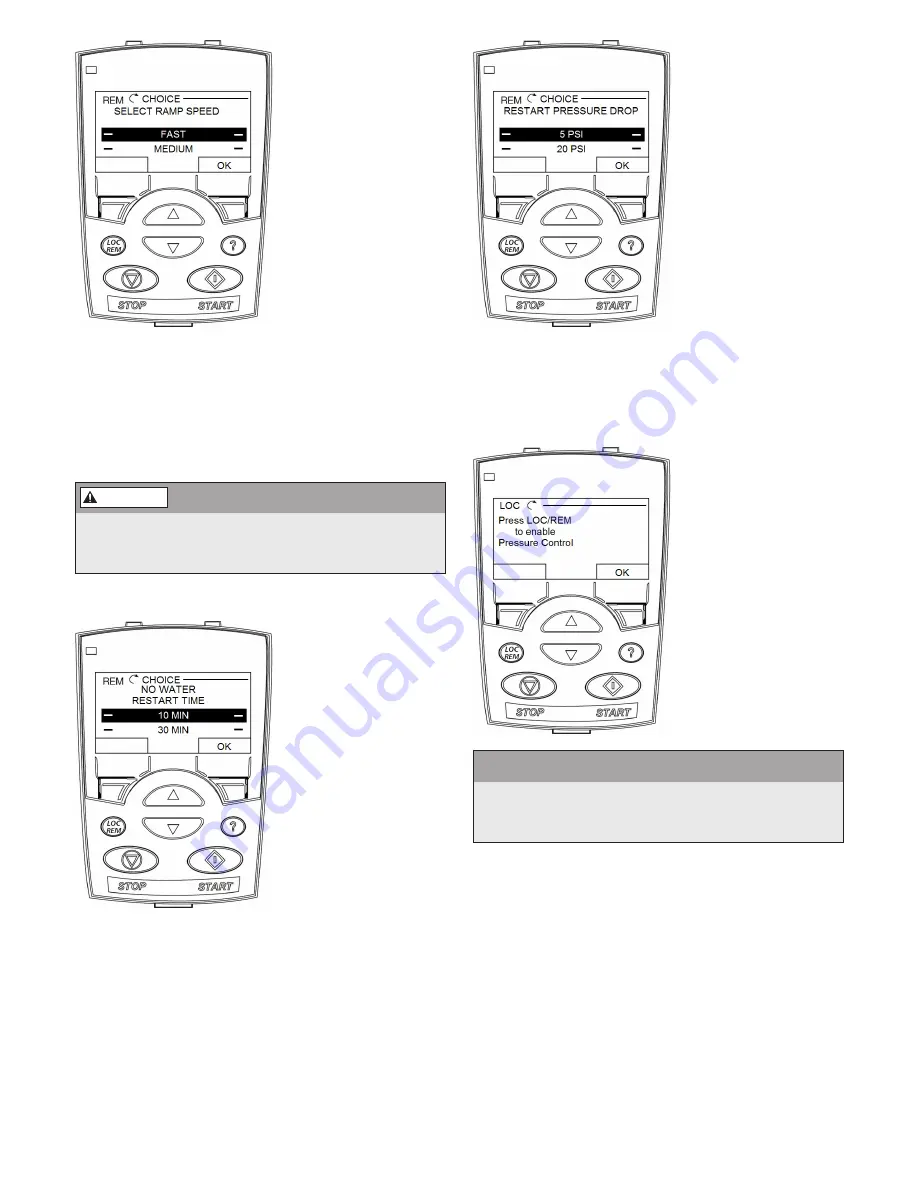
21
RAMP SPEED
SETTING:
Select
the ramp speed
based on the system
requirements. The
ramp speed sets the
acceleration and
deceleration time
for the motor. The
acceleration time
is the time for the
motor to transition
from 0Hz (stopped)
to 60Hz (full speed).
The deceleration time
is the time for the
motor to transition
from 60Hz (full speed) to 0Hz (full stopped). The
FAST ramp selection sets the acceleration ramp to 5
seconds and the deceleration ramp to 8 seconds. The
MEDIUM ramp selection sets both the acceleration
and the deceleration ramp to 25 seconds. The SLOW
ramp selection sets both the acceleration and the
deceleration ramp to 60 seconds.
Setting the Ramp Speed too fast can result in
unstable operation and can damage pump, motor
and piping.
NO WATER RESTART
TIME SETTING:
The
No Water Restart
Setting sets the time
between detection
of a No Water/Loss
of Prime fault and the
restart of the system.
For example, if the No
Water Restart Time
is set to 10 MIN, the
system will restart 10
minutes after a Water/
Loss of Prime fault has
been detected. This
parameter is typically
set according to the
recovery rate of the water source. The restart time can
be set to 10 minutes, 30 minutes or 1 hour using the
Start-Up Assistant.
RESTART PRESSURE
DROP SETTING:
The
Restart Pressure Drop
Setting allows the user
to select the amount of
pressure drop allowed
in the system before
the pump restarts after
a No Water Demand
condition is detected.
A No Water Demand
condition exists
when the pump has
satisfied the desired
system pressure and
reached the minimum
frequency. If the
Restart Pressure Drop is set to 5 PSI and the pump has
satisfied the desired system pressure and turned off
on no demand, the controller will turn the pump back
on after the system pressure has dropped 5 PSI below
the system pressure setting.
START REMINDER
SCREEN:
This is a
reminder screen.
This screen is shown
only if the controller
is set to local mode
(LOC). To change to
remote mode (REM)
and enable pressure
control, press the LOC/
REM button.
CAUTION
The controller ignores the pressure sensor feedback
signal and Start Signal on DI1 when operated in local
(LOC) mode. Hazardous pressure can result.
The controller is now set up and is ready to be started.
SETTING THE CONTROL MODE
The Control Mode can be set to either local (LOC)
or remote (REM). The Control Mode is indicated in
the upper left hand corner of the display screen. Use
REM for pressure control mode. This mode uses the
pressure transducer feedback on AI2 to control the
system pressure. Note that the start and stop buttons
on the display are disabled in REM mode. The start
enable on DI1 can be used to remotely start and stop
the motor. Use LOC for fixed speed mode. The speed
can be set with the up and down buttons on the
keypad. The motor can be started and stopped using
the start and stop buttons on the keypad. The in LOC
mode the start enable on DI1 is disabled.
WARNING
Содержание CentriPro SPD Plus
Страница 34: ...34 NOTES ...
Страница 35: ...35 NOTES ...